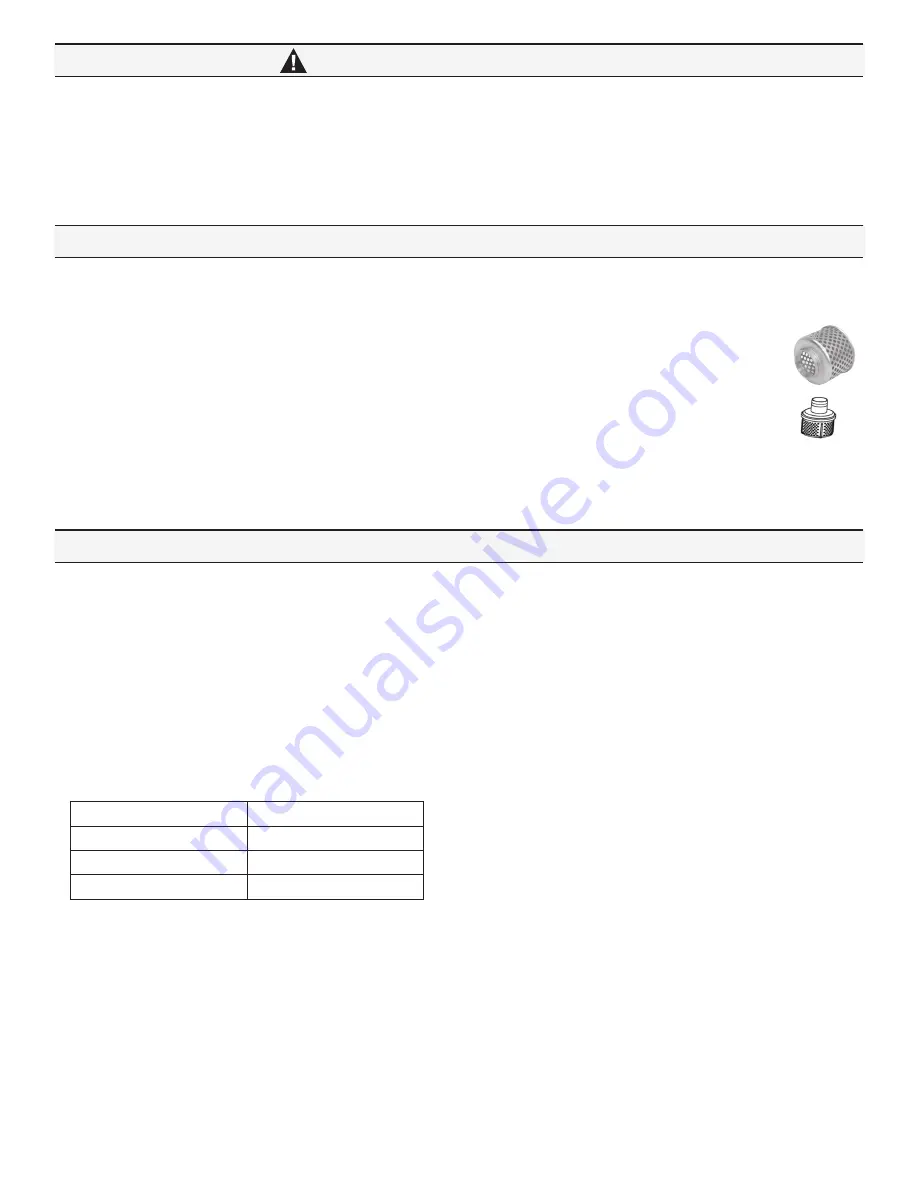
2
Please Note: It is illegal to ship or transport any hazardous
chemicals without United States Environmental Protection
Agency Licensing.
1. Always drain and flush pumps before servicing or
disassembling for any reason.
2. Before returning unit for repair, drain out all liquids and
flush unit with neutralizing liquid. Then, drain the pump.
Attach a tag or include a written notice certifying that this
has been done.
3. Never store pumps containing a hazardous chemical.
Hazardous Substance Alert
Prior to Mounting
Before setting up the pump for operation, check to see that
the motor and pump turn freely by hand. If it cannot be turned
over by pulling on the recoil starter, open casing to check for
obstructions lodged in pump.
Selecting the Suction Line
To get full capacity of the pump, the suction line should be the
same size as the pump suction port. If suction hose is longer
than approximately 6 feet, use next size larger hose.
The suction line must be free of air leaks. All joints and
connections of the suction line must be tightened securely so
that no additional air may enter the suction side through a
loose connection. Use a good grade of suction hose that will
not collapse.
Basket Strainer
The basket strainer supplied with this pump is
to be used when transferring solutions that may
contain debris and solids which could become
lodged in the pump or damage the impeller.
Because of the high flow capacity of this
pump, unknown debris could be siphoned off
the bottom of the tank. Install the strainer on the suction side
of the pump whenever possible to avoid pump damage.
Plumbing Installation
Preparations before Starting the Engine
1. Fuel: Check fuel level in tank. Do no over fill tank. Use fresh,
clean automotive fuel. Note:
DO NOT FILL FUEL TANK
WHEN ENGINE IS RUNNING.
2. Engine Oil: Before checking or refilling with engine oil,
make sure the engine is stopped and placed on a stable,
level surface. Use oil recommended for ambient air
temperatures that the engine will be running at. See
chart below. Change oil according to manufacturer’s
recommendation. (Once after the first 20 hours and every
100 hours thereafter.)
2. Priming Water:
IMPORTANT: PUMP MUST NOT BE RUN DRY.
On self-priming pumps, only the chamber needs to be filled
with liquid. The pump must not run unless the priming
chamber is completely filled with liquid because there is a
danger of damaging the mechanical seal, which depends on
the liquid for its lubrication.
Self-priming models can be primed by removing the filler
cap, located at the top of the pump where the discharge line
is mounted to the pump, and filling the priming chamber
with liquid. The priming chamber will fill to the level of the
inlet port. After use, the priming chamber should be flushed
and drained to avoid chemical corrosion and damage from
freezing. Drain by removing the lower drain plug located at
the bottom of the casing.
Starting the Pump
IMPORTANT: Before starting engine, be sure the priming
chamber is filled with liquid and the discharge hose is secure.
1. Turn engine switch located by recoil starter to ON position.
2. Turn the fuel cock to ON.
3. Push the throttle lever to a slightly open position.
4. Operation of choke lever.
When engine is cold:
In cold weather, start engine with choke in fully closed
position.
In warm weather, start engine with choke in half- closed
position.
When engine is warm:
Start engine with choke in fully open position.
5. Start engine by pulling recoil starter out quickly and
forcefully. Repeat pulling until the engine starts.
Operation of the Pump
1. Idle the engine for 3 to 5 minutes to warm it up.
2. Open the throttle lever to the upper zone after engine
has warmed up.
3. Once the pump has primed, you will note a load on the
engine; adjust RPMs to proper speed for your pumping
application.
Operation and Maintenance
Air Temperature
Single-grade Oil
85° F
#40W
60° F
#30W
32° F
#20W