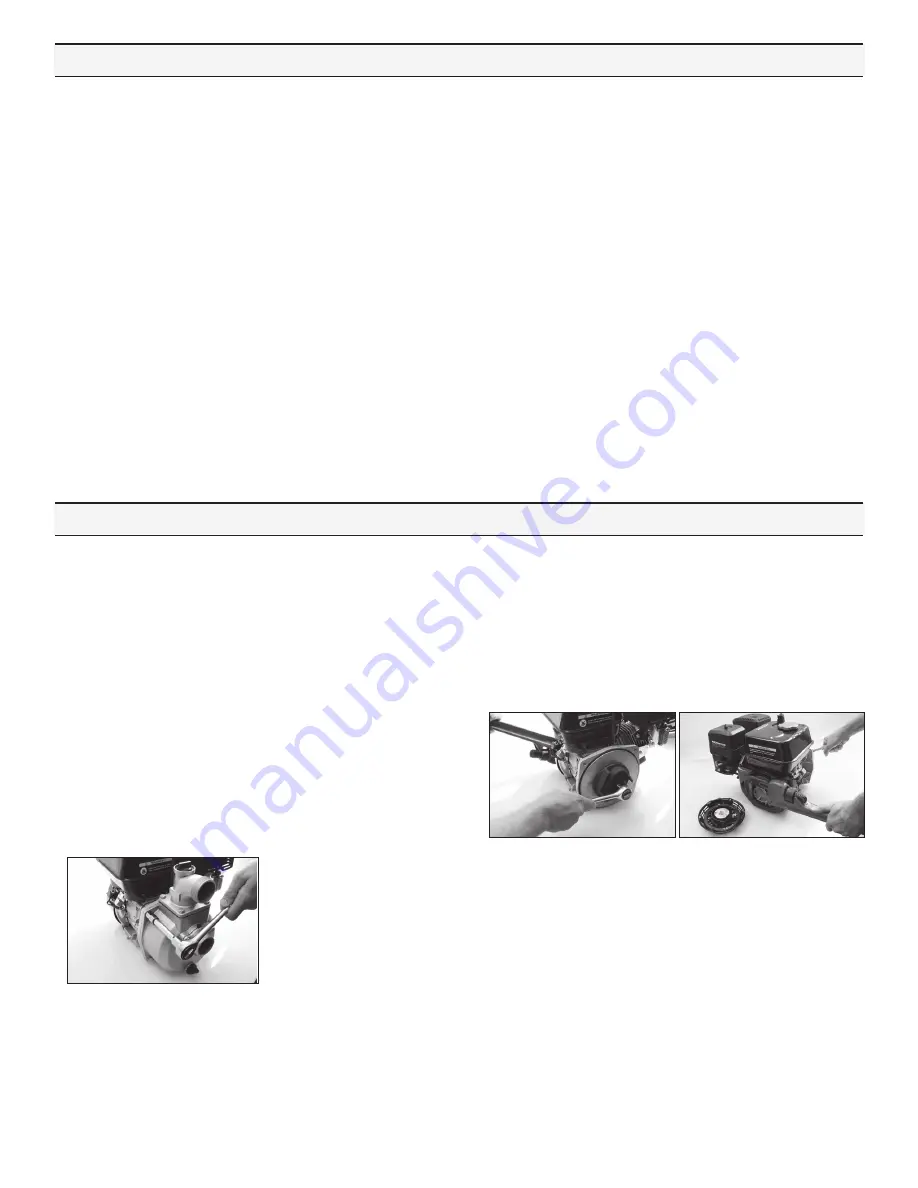
3
(Operation and Maintenance Continued)
Stopping the Pump
1. Stop pump for a short time:
Run engine throttled all the way down (fully to the right).
Turn engine switch to OFF position.
2. Stopping pump for storage:
Turn fuel cock to OFF position instead of turning the engine
switch off.
Let the engine idle for 2 to 3 minutes until fuel in carburetor
is depleted and engine stops. If a valve is installed on the
discharge hose, you may run pump with valve closed during
this procedure.
Note: Pump must not be run dry. Make sure there is water
in the priming chamber.
Storage
1. Drain pump. Flush Pump after Use.
One of the most common causes for faulty pump
performance is gumming or corrosion inside the pump.
Flush the pump and entire system with a solution that will
chemically neutralize the liquid pumped. Mix according
to the manufacturer’s directions. This will dissolve most
residues remaining in the pump, leaving the inside of the
pump clean and ready for use.
To Prevent Corrosion:
After cleaning the pump as directed above, flush it with
permanent-type automotive antifreeze (Prestone, Zerex,
etc.) containing a rust inhibitor. Use a 50% solution; half
antifreeze and half water, or fill the pump with FLUID FILM
and drain it. A protective coating of FLUID FILM will remain
on the inner pump surfaces. Save the excess FLUID FILM
for the next application. Plug ports to keep out air during
storage. For short periods of idleness, noncorrosive liquids
may be left in the pump, BUT AIR MUST BE KEPT OUT. Plug
the ports or seal port connections.
2. Drain all the fuel from the fuel tank, fuel lines, and filter.
3. Store pump in a clean, dry environment
Operation and Maintenance
Always flush pump with water or neutralizing agent
before servicing.
Pump Housing Disassembly
For this pump model, seal replacement requires that the
pump be fully removed from the engine. Observe carefully the
disassembly process, (orientation and order of part assembly)
to ensure an easy assembly process.
1.
Pull spark plug wire off spark plug for safety
considerations.
Remove the four bolts holding the casing
to the casing cover and frame using a 14mm socket wrench.
Tap pump casing on the discharge port with a rubber
hammer, if necessary, to break it loose from the casing cover.
Check inside pump casing. If badly eroded or damaged,
pump casing should be replaced. Remove O-rings from
casing cover and volute.
2. Remove volute and inspect for wear. Replace if eroded.
3. Remove impeller by turning the bolt counterclockwise using
a socket and impact wrench. If an impact wrench is not
available, it may be necessary to hold the crankshaft from
turning. To keep the crankshaft from turning during
disassembly, remove the three bolts holding the recoil
starter using a 10mm socket wrench. Then, using a pipe
wrench or another tool, hold the starter hub and turn the
impeller bolt off. Using a pry bar on each side of impeller
closest to the crankshaft slide impeller off. Use caution
during the removal so to not damage the impeller. Remove
the key from crankshaft keyway. Look for shims that may
be present between the impeller and shaft. This shim is
for obtaining the proper clearance between the impeller
and volute. Be careful not to damage the starter hub while
gripping it with the wrench.
4. Between the impeller and casing cover is the mechanical
seal. On the backside of the impeller is the seal’s ceramic
seat. If either part of the seal is damaged, with cracked or
scuffed surfaces, the seal will fail to perform satisfactory
and will leak. To remove the seal seat from the impeller,
use a small blade screwdriver and wedge the seal seat out
and discard. To remove the mechanical seal, it is necessary
to first remove the casing cover by removing the four bolts
holding it to the engine, using 13mm socket wrench. Note
that these bolts have seal washers on them and must not be
damaged. From the backside of the casing cover, press the
mechanical seal out and discard it.
Repair Instructions