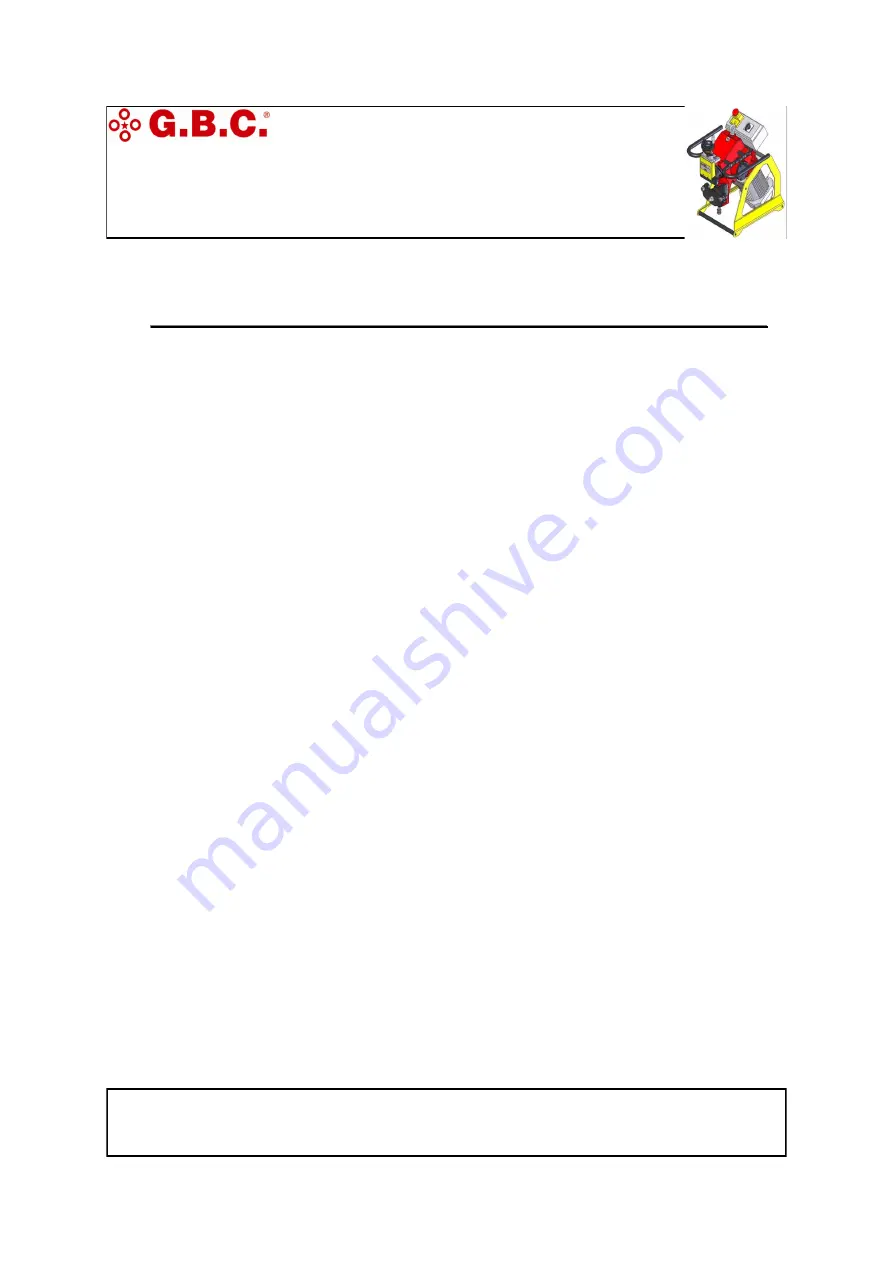
25
CHALLENGE 12
Original Instructions
—
rev.2011
—
in compliance with the paragraph 1.7.4 of the Machinery
Directive 2006/42/CE
G.B.C. Industrial Tools S.p.A.
Via Artigiani,17
–
25030 Torbiato di Adro (Bs)
–
Italia
–
Tel. + 39 030 7451154
–
Fax. + 39 030 73 56 629
TROUBLESHOOTING AND ACOUSTIC EMISSION
TROUBLESHOOTING AND ACOUSTIC EMISSION
TROUBLESHOOTING AND ACOUSTIC EMISSION
The machine does not run :
Check the power supply is connected and sui-
table in regard to the motor power consumption.
The machine does not run properly :
Check the condition of the shaft and
verify it to perfectly spins around its axis of rotation.
The machine does not bevel :
Check the milling tools conditions and ensure
that the plate you are working does not require special bevelling tools due to
its composition.
Always ask suggestions to your referent in G.B.C. as we are at your com-
plete disposal.
The acoustic emissions are within the maximum limits provided by the current
Machinery Directive.
The tests are performed on every single machine and the results are stored in
our archives.