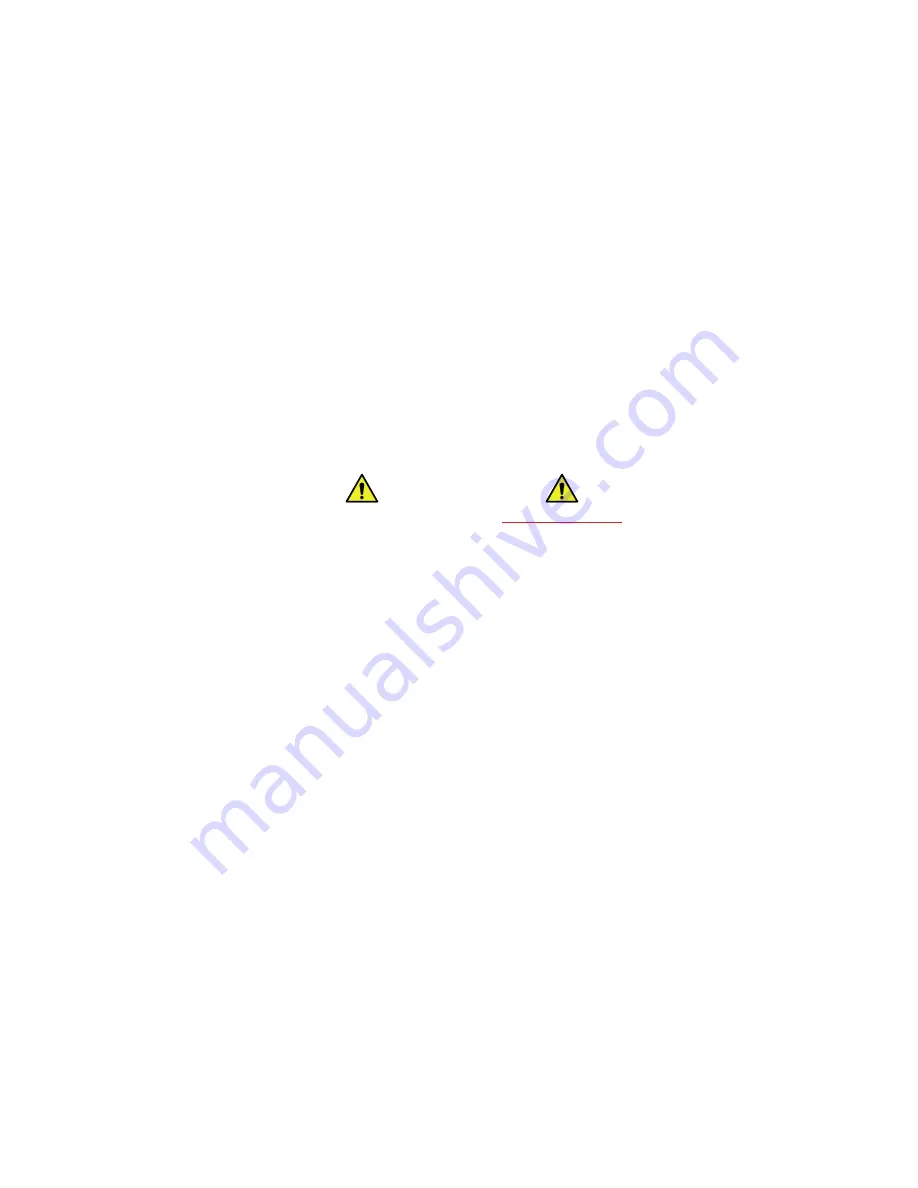
1
IMPORTANT SAFETY INSTRUCTIONS BELOW
WARNING:
Failure to provide adequate structural strengthening, prior to installation can result in
serious personal injury or damage to the equipment. It is the installer’s responsibility to ensure the
structure to which the component is affixed can support four times the weight of the component and
any additional apparatus mounted to the component.
WARNING:
Do not exceed the weight capacity for this product as listed below. This can result in serious
personal injury or damage to the equipment. It is the installer’s responsibility to ensure that the total
combined weight of all attached components does not exceed that of the maximum figure stated.
WARNING:
Risk of death or serious injury may occur when children climb on audio and/or video
equipment or furniture. A remote control or toys placed on the furnishing may encourage a child to
climb on the furnishing and as a result the furnishing may tip over on to the child.
WARNING:
Risk of death or serious injury may occur. Relocating audio and/or video equipment to
furniture not specifically designed to support audio and/or video equipment may result in death or
serious injury due to the furnishing collapsing or over turning onto a child or adult.
SAFETY
DISCLAIMER
ADDITIONAL WARNINGS:
1.
Keep all documentation/instructions after fitting.
2. Read all technical instructions fully before installation and use. It is the installer’s responsibility to ensure that all
documentation is passed on to the end user and read fully before operation.
3.
Do not use near water or outdoors unless the product has been specifically designed to do so.
4. Protect any cables or cords being used near this bracket from being walked on or pinched to prevent damage and
risk of injury.
5. Use this product only for its intended purpose as described in the product instructions and only use attachments/
accessories specified by the manufacturer.
6. Do not operate the product if it is damaged in any way, liquid has been spilled or objects have fallen into the
apparatus, the apparatus has been exposed to rain or moisture, does not operate normally, or has been dropped.
Contact the original installer/manufacturer to arrange repair or return.
WARNING - To reduce the risk of burns, fire, electric shock, or injury to persons:
1. Clean only with a dry cloth and always unplug any electrical items being used in conjunction with this product before
cleaning.
Future Sound & Vision trading as Future Automation intend to make this and all documentation as accurate as
possible. However, Future Automation makes no claim that the information contained herein covers all details,
conditions or variations, nor does it provide for every possible contingency in connection with the installation or use
of this product. The information contained in this document is subject to change without prior notice or obligation of
any kind. Future Automation makes no representation of warranty, expressed or implied, regarding the information
contained herein. Future Automation assumes no responsibility for accuracy, completeness or sufficiency of the
information contained in this document.
WARNING – RISK OF INJURY!
Only for use with equipment weighing
22LBS (10KG) OR LESS
.
Use with heavier projectors/equipment may lead to instability causing
tip over or failure resulting in death or serious injury.
Bracket Suitable for Residential and Commercial Use.
Summary of Contents for SPS & SA
Page 2: ......
Page 29: ...NOTES...