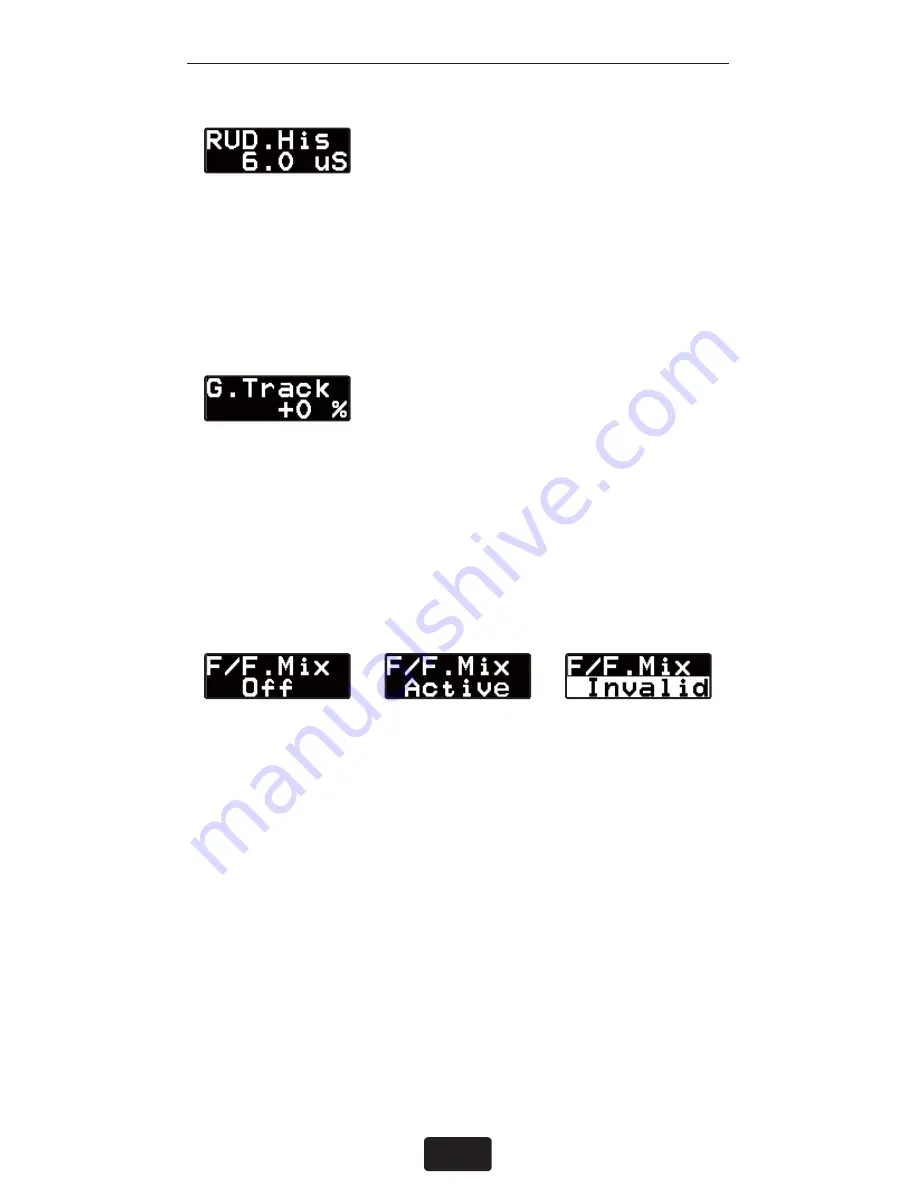
R
UDDER
G
YRO
E
XPERT
S
ETTING
95
(13) Rudder histeresis
default: 7 uS
ranges: 0
~
50 uS
<(? ( > %%'(
PNQPQ>? (%
(14) Gain tracking
default: 0 %
ranges: -20%
~
+20%
<(? ('(%'=%' '%=
'( (PNQPQ>
? (%
(15) F/F mixing
default: off
<(%(;:#F'
(%('D'(
#F'D=('#
##('=#
;#F'(%:(()*+$,0
# % %#F'
:( #(:%% %%?
( '%('
Summary of Contents for CGY750
Page 1: ...1M23N24902 INSTRUCTION MANUAL ...
Page 13: ...CONTENTS Extension Cord Sensor Mounting Bracket Magnets 2 Revolution Sensor 13 ...
Page 23: ...OPENING SCREEN 23 K D H D I M D I 0 D K M I F ...
Page 57: ...SWASH SERVO INSTALLATION AND SETUP D U D H D D M D D M D D M 57 ...
Page 64: ...BEFORE FLIGHT CHECKLIST D K I K 7 D F K P K A Q K F D M H M H D H 64 ...
Page 67: ...ADJUSTMENTS DURING THE TEST FLIGHT F H 0 H 0 D D L D H D M D J M D M D I H D F M 67 ...
Page 81: ...MOUNTING THE MAGNET AND SENSOR 81 D U D H D U F J D D H D D ...
Page 83: ...FUSELAGE SETTING PRECAUTIONS 83 H M D D ...
Page 85: ...GOVERNOR OPERATION 85 Deviation from set speed D I W U F H H D W H D ...
Page 98: ...RUDDER GYRO EXPERT SETTING 98 22 Gyro data reset D PNQ P7F ddQ PNQ D ...
Page 124: ......