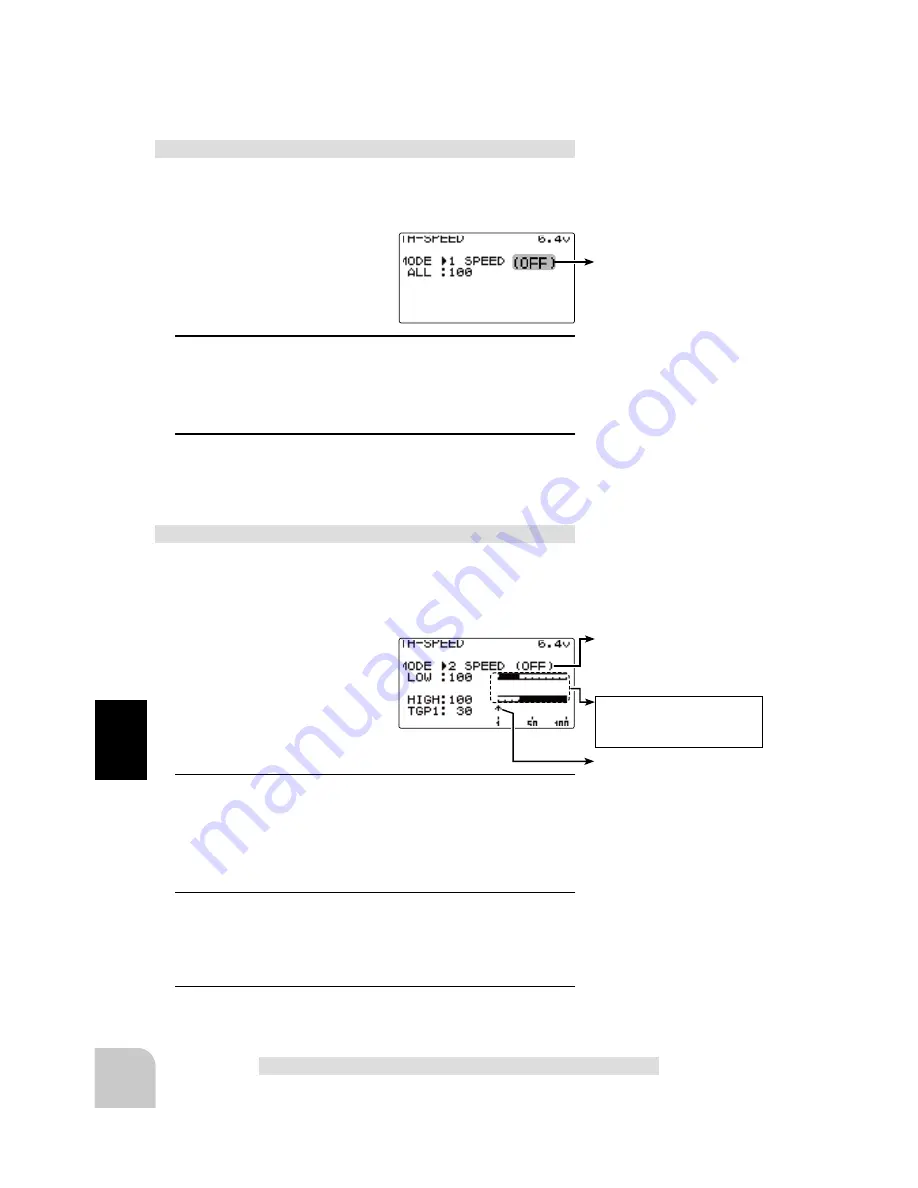
Setting item
MODE :Speed type selection
ALL :Speed
adjustment
Setup item selection
- Select by (JOG) button up or
down operation.
Setting item
MODE :Speed type selection
LOW
:Low side range speed
adjustment
HIGH
:High side range speed
adjustment
TGP1
:Low and medium speed
switching point
Setup item selection
- Select by (JOG) button up or down operation.
When a value of 99 or less is set
at either LOW or HIGH, the dis-
play is switched from OFF to ON
by trigger operation.
Throttle trigger position
The LOW and HIGH ranges
are linked to the TGP1 set
point and displayed.
64
Fu
n
c
tio
n
Throttle Speed "THSPD"
(Preparation)
- Select the setting item "MODE" by (JOG) button up or down
operation. Press the (+) or (-) button and select "1 SPEED".
1
("ALL" delay adjustment)
Select "ALL" by (JOG) button up or down operation.
Use the (+) or (-) button to adjust the delay of the entire
throttle forward side range.
2
When ending setting, return to the initial screen by pressing
the (END) button twice (for direct selection, press the (END)
button once).
Adjustment method for 1 SPEED
When a value of 99 or less is
set at ALL setting, the display
is switched from OFF to ON by
trigger operation.
Adjustment range
LOW :1~100
HIGH :1~100
At 100%, there is no delay.
TGP1 :1~100
(Preparation)
- Select the setting item "MODE" by (JOG) button up or down
operation. Press the (+) or (-) button and select "2 SPEED".
1
("LOW" and "HIGH" delay adjustment)
Select "LOW" or HIGH" by (JOG) button up or down opera-
tion.
Use the (+) or (-) button to adjust the delay of the entire
throttle forward side range.
2
(Speed switching point adjustment)
When you want to change the "LOW" and "HIGH" switching
point, select the setting "TGP1" by (JOG) button up or down
operation.
3
When ending setting, return to the initial screen by pressing
the (END) button twice (for function menu screen, press the
(END) button once).
Adjustment method for 2 SPEED
Adjust button
- Adjust with the (+) and (-) but-
tons.
- Return to the initial value by
pressing the (+) and (-) buttons
simultaneously (approx. 1 sec).
Initial value
LOW, HIGH :"100"
TGP1 :30
Speed type Select button
- Select with the (+) or (-) but-
tons.
Adjust button
- Adjust with the (+) and (-) but-
tons.
- Return to the initial value "100"
by pressing the (+) and (-) but-
tons simultaneously for about 1
second.
Adjustment range
1~100% (each direction)
At 100%, there is no delay.
Speed type Select button
- Select with the (+) or (-) but-
tons.