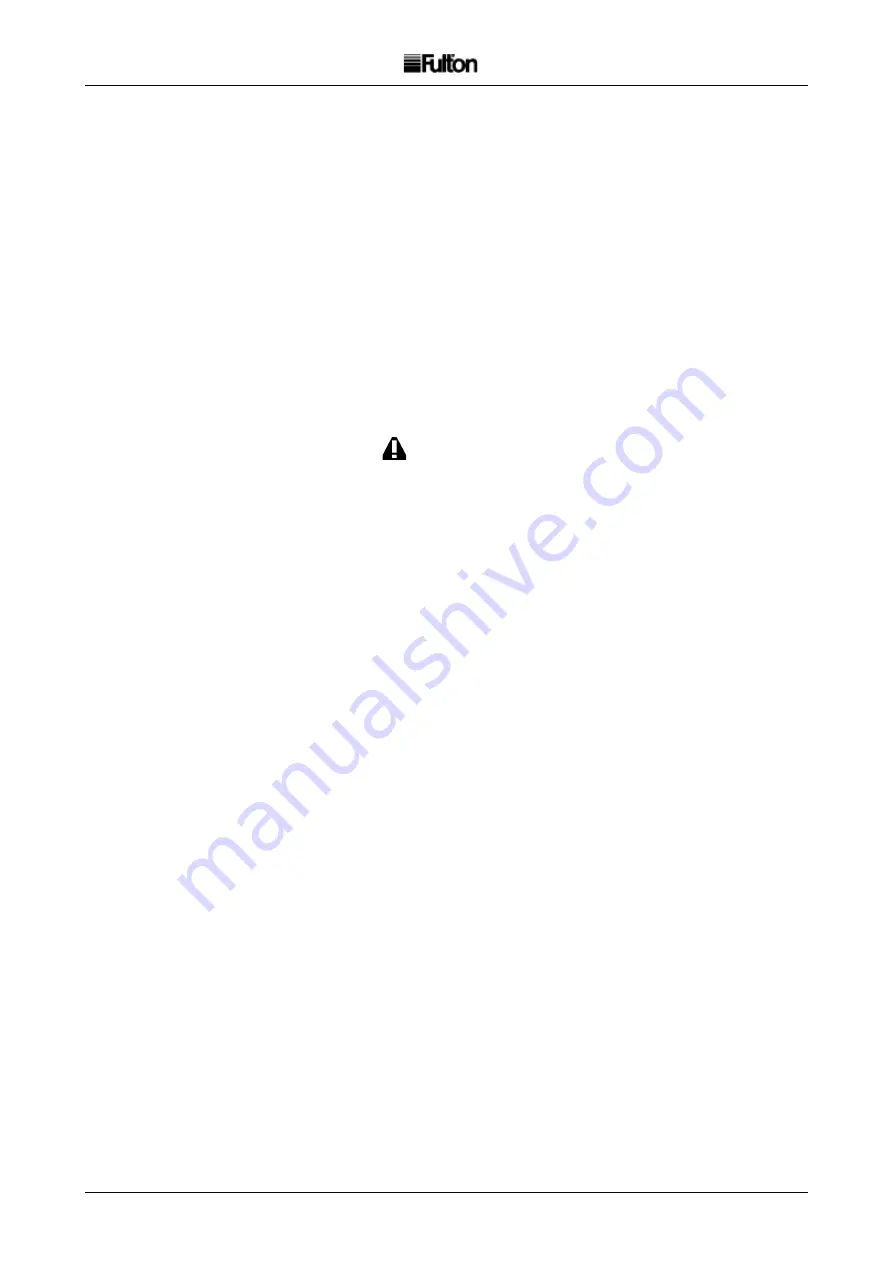
J OIL-E-08 2008
2.7 MAIN STEAM VALVE
The main steam stop valve should be inserted in the steam line approximately 12in. (305 mm) from
the top of the boiler.
2.8 STEAM SAFETy VALVES
Safety Valves are factory fitted and preset, they MUST NOT be adjusted. The discharge outlet
should be piped to a safe discharge point and the piping so arranged that any condensate trapped
in the pipework will drain away from the valve.
Note:
It is recommended that the safety valve discharge pipework is installed to the requirements of BS806
clause 4.9.7.
(a) The lift pressure is indicated on the safety valve.
(Do not adjust).
(b) The safety valve fitted to the boiler is designed to prevent the boiler exceeding it's design
pressure.
(c)
Any system connected to the boiler not capable of accepting boiler pressure must be
protected by a separate safety valve set to the required pressure.
(d) Long radius fittings to be used with a minimumof 6 diameters to the first fitting.
2.9 WATER gAUgE SET
(The design may vary from that illustrated)
Numbers may vary due to individual countries regulations.
Boilers are normally supplied with two complete water gauge sets. The water gauge blowdown
cock should be connected to the auxiliary blowdown line from the water column blowdown valve in
soft copper tubing. The connection to the gauge cock is 6mm (0.25in.).
2.10 OIL SUPPLy
The positioning of the oil storage tank will be dependent on site conditions and local regulations. The
burner fuel pump is of the bypass type requiring the installation of feed and return lines between the oil
storage tank and the boiler. These lines should be in tubing of a minimum bore of 10 mm.
A fire valve, stop valve and check valves should be inserted in the oil feed line.
To avoid blockages in the fuel pump and burner nozzle, a metal cartridge oil filter should be fitted.
Fibrous cartridge filters are not recommended.
The final connections between the fuel pump and the feed and return lines should be made with
the flexible fuel lines supplied. If the oil storage tank is positioned higher than the boiler, a non-return
valve should be fitted to the return line.
To overcome suction problems at the fuel pump, all vertical lifts in the feed pipe should be made as
close to the boiler as possible. The burner fuel pump pressure is preset at the factory and should not
require adjustment.
2.11 ELECTRICAL REQUIREMENTS
An individual wiring diagram for the boiler is located on the inside cover of the control box.
When referring to the electrical specification of the boiler, the reference number located on the rear
inside wall of the control box and the wiring diagram number should be quoted.
The audible alarms provided are mounted on the side of the control panel, if not audible they
should be repositioned where they can be heard by a person competent to take the appropriate
action should the alarm be activated.
Unless otherwise specified, the alarms supplied will be mains voltage models. Unless otherwise
specified all models are supplied with burner motors and feed water pump motors arranged for
operation on a three phase supply.
The power ratings and requirements are given in Technical Data - Section 5.
WARNINg
Factory fitted safety valves are preset to protect the boiler only and
must not be used to protect any other items not capable of
accepting boiler pressure.
10
2
2
Summary of Contents for 10J
Page 42: ...J OIL E 08 2008...
Page 56: ...J OIL E 08 2008 A0 2 1 BOILER OIL 1 2 3 4 5 6 December 12 2004...
Page 76: ...J OIL E 08 2008 F1 4 1 WATER LEVEL GAUGE ASSEMBLY 6 60 350mm and 300mm Clifton December 2004...
Page 84: ...J OIL E 08 2008 H1 1 1 PUMP FEED WATER 1 December 2004...
Page 86: ......