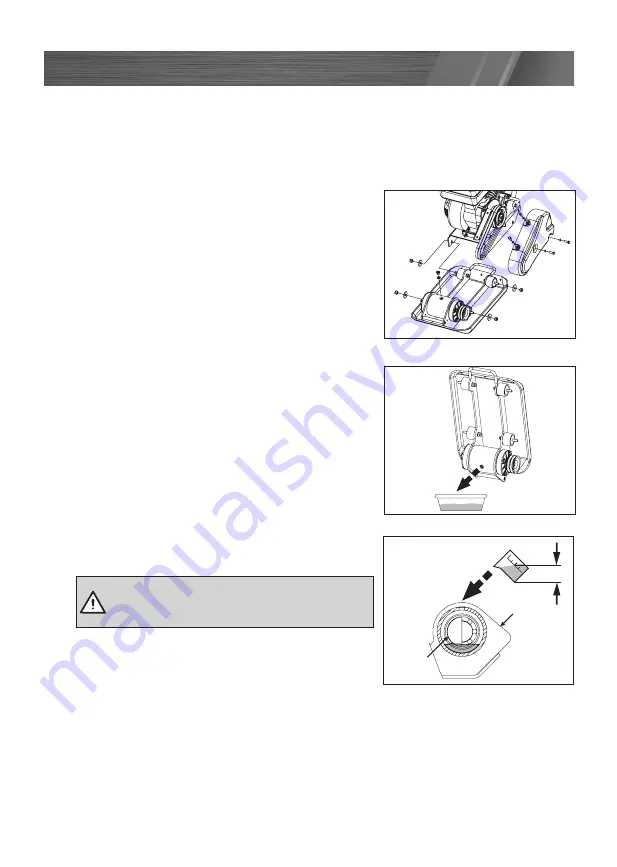
18
Exciter lubrication
The exciter housing is pre-serviced using Automatic Transmission Fluid Dextron III,
Mercon, EXXON (ESSO) NUTO H-32 or its equivalent. Change fluid after 200 hours
of operation.
1.
Let exciter (9) cool before changing exciter oil.
2.
Remove the belt guard and V-belt(s).
3.
Loosen the bolts that hold the engine deck (6)
to the compacting plate (7).
4.
Lift the engine deck (6), with the engine
attached, from the compacting plate (7) (fig. 16).
5.
Remove the drain plug from the top of the
exciter housing (9). Tilt the compacting plate (7)
upside down so oil can drain from the exciter
housing. Examine oil for metal chips as a
precaution to future problems. (fig. 17)
6.
Return compacting plate to the upright
position.
7.
Fill the exciter housing (9) with the
recommended exciter oil. (150ml capacity)
(fig. 18)
8.
Apply pipe sealant to drain plug and reinstall
into top of exciter housing.
9.
Reinstall engine deck (12), V-belt(s) and belt
guard. Ensure all bolts are fully tightened.
MAINTENANCE (cont.)
V-belt
Clutch pulley
Exciter pulley
A
B
EXCITER
EXCITER
SHAFT
150 ml
Fig. 16
V-belt
Clutch pulley
Exciter pulley
A
B
EXCITER
EXCITER
SHAFT
150 ml
Fig. 18
WARNING!
Do not overfill - overfilling
can result in excessive temperatures in
the exciter.
V-belt
Clutch pulley
Exciter pulley
A
B
EXCITER
EXCITER
SHAFT
150 ml
Fig. 17