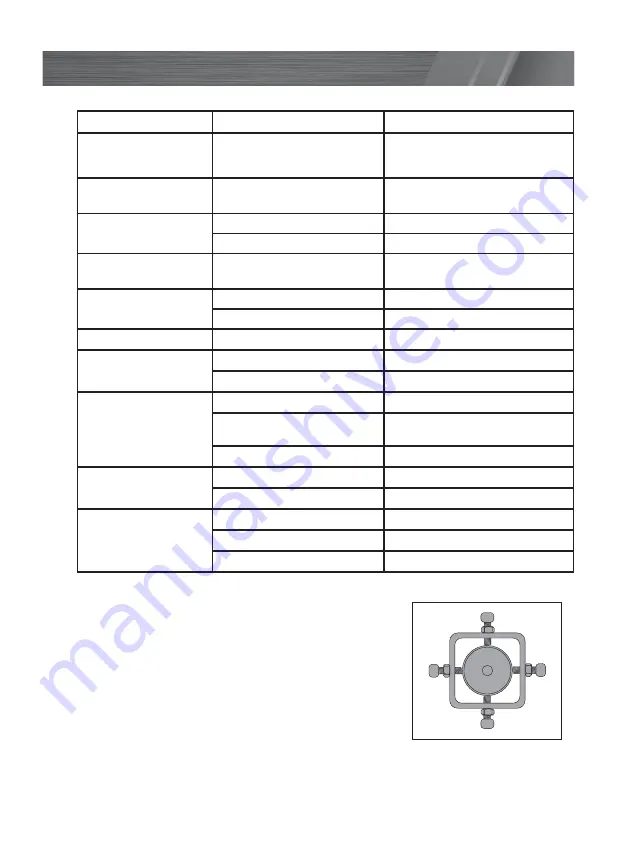
22
KNOW YOUR PRODUCT
Advanced blade tracking:
Most tracking adjustments can be done by simply adjusting the top
wheel tracking knob as the lower wheel comes correctly adjusted
from the factory. However there may come a time when adjustment is
necessary such as if the blade keeps falling off the drive wheels.
At the back of the unit you will find 4 screws that allows fine
adjustment to the lower pulley tacking. The upper and lower screws
adjust the vertical angle and the left and right screws adjust the
horizontal angle. If the lower wheel tracking is out, only adjust the
upper and lower screws. However if the wheels keep throwing the
blade, you will have to adjust horizontal angle using the left and
right screws. When adjusting the angle ensure you only make small
adjustments, being careful to tighten and loosen in the direction you wish to align. For example,
loosening the left screw then tightening the right screw. This is to ensure there is no movement in
the wheels angle during operation. Be sure all adjustment screws are tight before use and you have
manually spun the wheels by hand to check the alignment.
TROUBLESHOOTING
Problem
Cause
Remedy
Bandsaw is not
working
No power supplied
Make sure the power plug is
connected and power outlet is in
working order
Cannot adjust
tracking
Tracking lock knob is on
Unlock the tracking lock by turning
the tracking lock knob anti-clockwise
Premature and
excessive tooth wear
Feed Pressure too high
Slow down feed rate
Guide hitting teeth alignment
Readjust blade tracking and guides
Finished surface too
rough
Feed rate too high
Slow down feed rate
Premature blade
breakage
Band tension too high
Readjust blade tension
Excessive feed pressure
Slow down feed rate
Cutting rate too slow
Damaged or worn blade
Replace blade
Gullets loaded with
chips
Speed too slow
Use faster speed
Chip brush not working properly
Clean or replace brushes
Belly shaped cuts
Improper blade tension
Readjust blade tension
Guide arm is too far from work
piece
Move guide arm closer to work piece
Excessive feed force
Use less feed force
Band stalls in work
Feed pressure too great
Use less feed force
Improper blade tension
Readjust blade tension
Blade vibration
Guides poorly adjusted
Readjust blade tracking and guides
Blades tension too low
Readjust blade tension
Work piece not properly secured
Secure work piece properly
Summary of Contents for FBBS-750
Page 25: ...25...