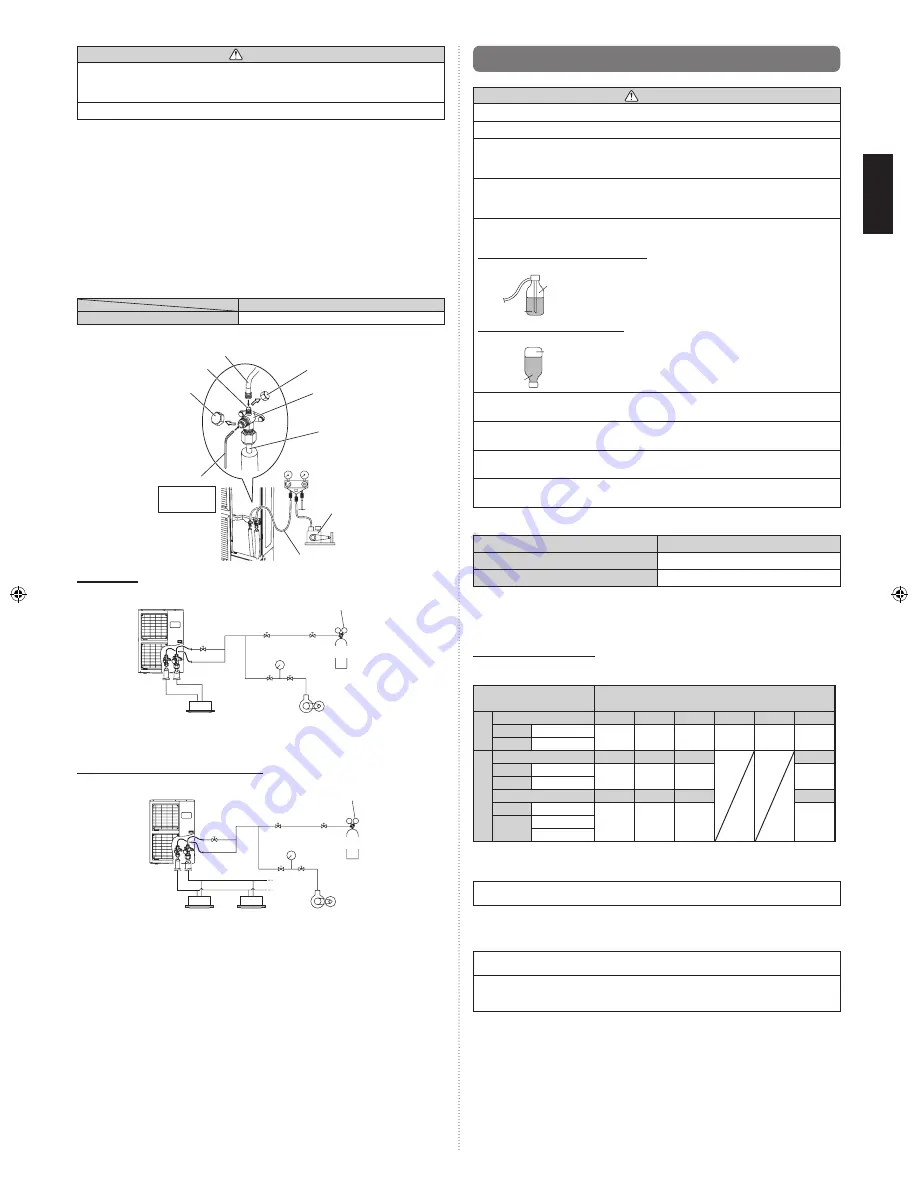
En-9
5.7. Additional charging
CAUTION
After vacuuming the system, add refrigerant.
Do not reuse recovered refrigerant.
When charging the refrigerant R410A, always use an electronic scales for refrigerant
charging (to measure the refrigerant by weight). Adding more refrigerant than the
specified amount will cause a malfunction.
When charging the refrigerant, take into account the slight change in the composition
of the gas and liquid phases, and always charge from the liquid phase side whose
composition is stable. Adding refrigerant through the gas pipe will cause a malfunction.
Check if the steel cylinder has a siphon installed or not before filling. (There is an
indication “with siphon for filling liquid” on the steel cylinder.)
Filling method for cylinder with siphon
R410A
Gas
Liquid
Set the cylinder vertical and fill with the liquid.
(Liquid can be filled without turning bottom up with the
siphon inside.)
Filling method for other cylinders
R410A
Gas
Liquid
Turn bottom up and fill with liquid.
(Be careful to avoid turning over the cylinder.)
Be sure to use the special tools for R410A for pressure resistance and to avoid mixing
of impure substances.
If the units are further apart than the maximum pipe length, correct operation can not be
guaranteed.
Make sure to back closing valve after refrigerant charging. Otherwise, the compressor
may fail.
Minimize refrigerant release to the air. Excessive release is prohibited under the Freon
Collection and Destruction Law.
5.7.1. For Pre-charge length
Refrigerant pipe size
Piping length (L) *Pre-Charge [m]
Standard
30
Size up (Liquid pipe)
15
5.7.2. If additional refrigerant is required
When the piping is longer than Pre-charge length, additional charging is necessary.
•
For the additional amount, see the table below.
•
Additional charging amount
Single type
L1 (*1) > Pre-charge length
Refrigerant pipe size
[mm (in.)]
Piping length
Standard
~30 m
40 m
50 m
60 m
70 m
g/m
Liquid
9.52 (3/8)
None
500 g
1,000 g 1,500 g 2,000 g 50 g/m
Gas
15.88 (5/8)
Size up
~30 m
40 m
50 m
g/m
Liquid
9.52 (3/8)
None
500 g
1,000 g
50 g/m
Gas
19.05 (3/4)
~15 m
25 m
35 m
g/m
Liquid
12.70 (1/2)
None
1,000 g 2,000 g
100 g/m
Gas
15.88 (5/8)
19.05 (3/4)
*1: Refer to “View” in the table of “4.3.1. Single type installation”.
Simultaneous operation multi type
Twin : L1+L2+L3 (*2) > Pre-charge length
Triple : L1+L2+L3+L4 (*3) > Pre-charge length
*2 : Refer to “View” in the table of “4.3.2. Simultaneous operation multi type installation.”
*3 : Refer to “View” in the table of “4.3.2. Simultaneous operation multi type installation.”
The additional charging amount for twin / triple type will be calculated as follows:
Additional charging amount (g)
= (A x 100) + (B x 50) + (C x 30) - 1,500
• A = Piping length (m) of liquid pipe [12.70 mm (1/2 in.)]
• B = Piping length (m) of liquid pipe [9.52 mm (3/8 in.)]
• C = Piping length (m) of liquid pipe [6.35 mm (1/4 in.)]
CAUTION
Use a clean gauge manifold and charging hose that were designed specifically for use
with R410A. Using the same vacuum equipment for different refrigerants may damage
the vacuum pump or the unit.
Do not purge the air with refrigerants, but use a vacuum pump to evacuate the system.
(1) Check that the valves are closed by removing the blank caps from the gas and
liquid pipes.
(2) Remove the charging port cap, and connect the gauge manifold and the vacuum
pump to the charging valve with the service hoses.
(3) Vacuum the indoor unit and the connecting pipes until the pressure gauge indicates
–0.1 MPa (–76 cmHg).
(4) When –0.1 MPa (–76 cmHg) is reached, operate the vacuum pump for at least
60 minutes.
(5) Disconnect the service hoses and fit the charging port cap to the charging valve to
the specified torque. (Refer to below table)
(6) Remove the blank caps, and fully open the 3-way valves with a hexagon wrench
[Torque: 6 to 7 N·m (60 to 70 kgf·cm)].
(7) Tighten the blank caps of the 3-way valve to the specified torque. (Refer to Table A
on page 8.)
Tightening torque [N·m (kgf·cm)]
Charging port cap
10 to 12 (100 to 120)
Service hose
Service hose with valve core
Charging port
Blank cap
Hexagon wrench
Connecting pipe
Gauge manifold
Vacuum pump
Charging port cap
3-way valve
Use a 4 mm
hexagon
wrench
Single type
Pressure regulating valve
Pressure gauge
Nitrogen
Indoor unit
Outdoor unit
Vacuum pump
Simultaneous operation multi type
Outdoor unit
Indoor unit
Indoor unit
Vacuum pump
Pressure gauge
Pressure regulating valve
Nitrogen
9379069274-04_IM.indb 9
28/11/2555 10:57:06
Summary of Contents for AOYG36LATT
Page 17: ......