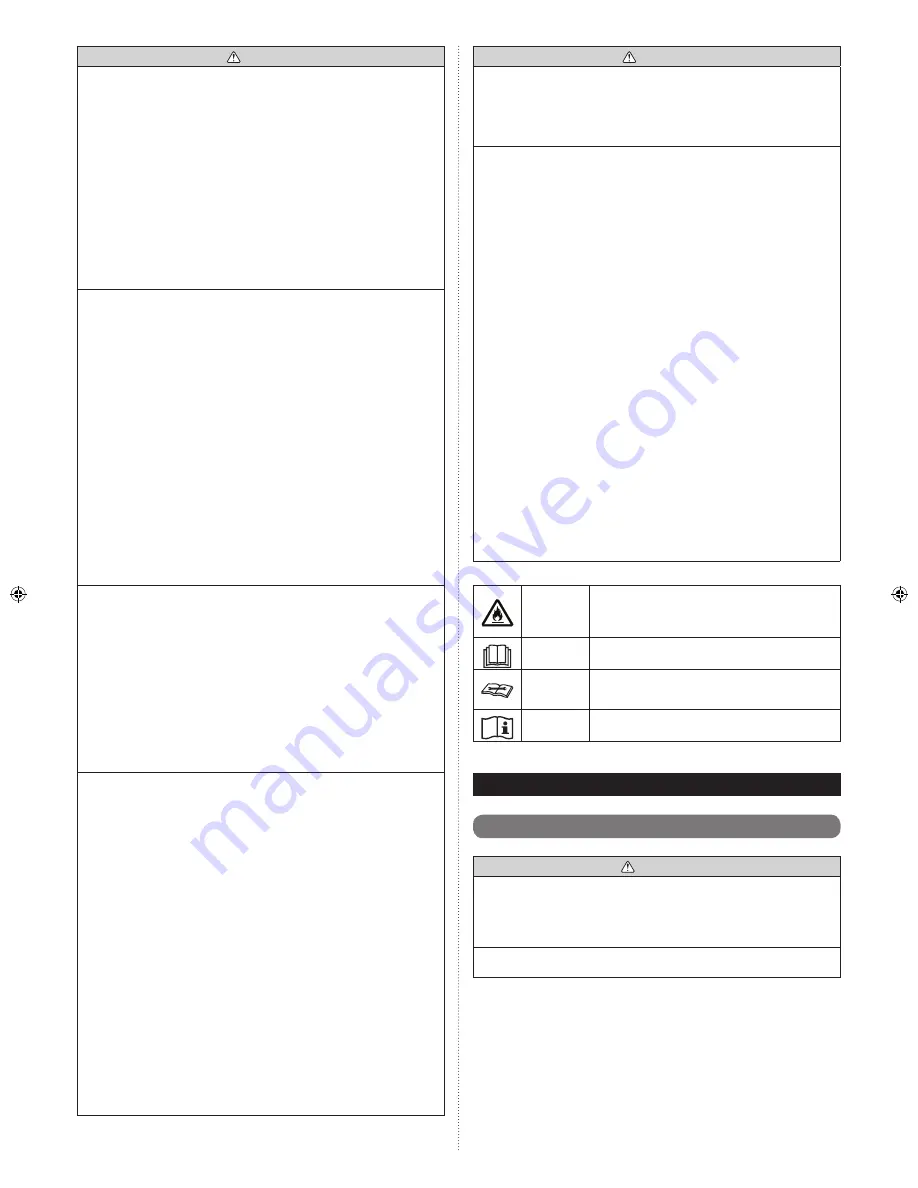
En-3
CAUTION
7.Leak detection methods
• Electronic leak detectors shall be used to detect
fl
ammable refrigerants, but the
sensitivity may not be adequate, or may need re-calibration. (Detection equipment
shall be calibrated in a refrigerant-free area.)
• Ensure that the detector is not a potential source of ignition and is suitable for the
refrigerant used.
• Leak detection equipment shall be set at a percentage of the LFL of the refrigerant
and shall be calibrated to the refrigerant employed and the appropriate percentage
of gas (25 % maximum) is con
fi
rmed.
• Leak detection
fl
uids are suitable for use with most refrigerants but the use of
detergents containing chlorine shall be avoided as the chlorine may react with the
refrigerant and corrode the copper pipe-work.
• If a leak is suspected, all naked
fl
ames shall be removed/extinguished.
• If a leakage of refrigerant is found which requires brazing, all of the refrigerant shall
be recovered from the system, or isolated (by means of shut off valves) in a part of
the system remote from the leak.
Oxygen free nitrogen (OFN) shall then be purged through the system both before
and during the brazing process.
8.Removal and evacuation
• When breaking into the refrigerant circuit to make repairs – or for any other
purpose –conventional procedures shall be used.
However, it is important that best practice is followed since
fl
ammability is a consid-
eration.
The following procedure shall be adhered to:
• remove refrigerant
• purge the circuit with inert gas
• evacuate
• purge again with inert gas
• open the circuit by cutting or brazing
• The refrigerant charge shall be recovered into the correct recovery cylinders.
• The system shall be “
fl
ushed” with OFN to render the unit safe.
• This process may need to be repeated several times.
• Compressed air or oxygen shall not be used for this task.
• Flushing shall be achieved by breaking the vacuum in the system with OFN and
continuing to
fi
ll until the working pressure is achieved, then venting to atmosphere,
and
fi
nally pulling down to a vacuum.
• This process shall be repeated until no refrigerant is within the system.
• When the
fi
nal OFN charge is used, the system shall be vented down to atmos-
pheric pressure to enable work to take place.
• This operation is absolutely vital if brazing operations on the pipe work are to take place.
• Ensure that the outlet for the vacuum pump is not close to any ignition sources and
there is ventilation available.
9.Charging procedures
• In addition to conventional charging procedures, the following requirements shall be
followed.
- Ensure that contamination of different refrigerants does not occur when using
charging equipment.
- Hoses or lines shall be as short as possible to minimize the amount of refrigerant
contained in them.
- Cylinders shall be kept upright.
- Ensure that the refrigeration system is earthed prior to charging the system with
refrigerant.
- Label the system when charging is complete (if not already).
- Extreme care shall be taken not to over
fi
ll the refrigeration system.
• Prior to recharging the system it shall be pressure tested with OFN.
• The system shall be leak tested on completion of charging but prior to commissioning.
• A follow up leak test shall be carried out prior to leaving the site.
10.Decommissioning
• Before carrying out this procedure, it is essential that the technician is completely
familiar with the equipment and all its details.
• It is recommended good practice that all refrigerants are recovered safely.
• Prior to the task being carried out, an oil and refrigerant sample shall be taken in
case analysis is required prior to re-use of reclaimed refrigerant.
• It is essential that electrical power is available before the task is commenced.
a) Become familiar with the equipment and its operation.
b) Isolate system electrically.
c) Before attempting the procedure ensure that:
• mechanical handling equipment is available, if required, for handling refriger-
ant cylinders;
• all personal protective equipment is available and being used correctly;
• the recovery process is supervised at all times by a competent person;
• recovery equipment and cylinders conform to the appropriate standards.
d) Pump down refrigerant system, if possible.
e) If a vacuum is not possible, make a manifold so that refrigerant can be removed
from various parts of the system.
f) Make sure that cylinder is situated on the scales before recovery takes place.
g) Start the recovery machine and operate in accordance with manufacturer’s
instructions.
h) Do not over
fi
ll cylinders. (No more than 80 % volume liquid charge).
i) Do not exceed the maximum working pressure of the cylinder, even temporarily.
j) When the cylinders have been
fi
lled correctly and the process completed, make
sure that the cylinders and the equipment are removed from site promptly and
all isolation valves on the equipment are closed off.
k) Recovered refrigerant shall not be charged into another refrigeration system
unless it has been cleaned and checked.
CAUTION
11.Labelling
• Equipment shall be labelled stating that it has been de-commissioned and emptied
of refrigerant.
• The label shall be dated and signed.
• Ensure that there are labels on the equipment stating the equipment contains
fl
am-
mable refrigerant.
12.Recovery
• When removing refrigerant from a system, either for servicing or decommissioning,
it is recommended good practice that all refrigerants are removed safely.
• When transferring refrigerant into cylinders, ensure that only appropriate refrigerant
recovery cylinders are employed.
• Ensure that the correct number of cylinders for holding the total system charge are
available.
• All cylinders to be used are designated for the recovered refrigerant and labelled for
that refrigerant (i.e. special cylinders for the recovery of refrigerant).
• Cylinders shall be complete with pressure relief valve and associated shut-off valves
in good working order.
• Empty recovery cylinders are evacuated and, if possible, cooled before recovery
occurs.
• The recovery equipment shall be in good working order with a set of instructions
concerning the equipment that is at hand and shall be suitable for the recovery of
fl
ammable refrigerants.
• In addition, a set of calibrated weighing scales shall be available and in good work-
ing order.
• Hoses shall be complete with leak-free disconnect couplings and in good condition.
• Before using the recovery machine, check that it is in satisfactory working order, has
been properly maintained and that any associated electrical components are sealed
to prevent ignition in the event of a refrigerant release.
Consult manufacturer if in doubt.
• The recovered refrigerant shall be returned to the refrigerant supplier in the correct
recovery cylinder, and the relevant Waste Transfer Note arranged.
• Do not mix refrigerants in recovery units and especially not in cylinders.
• If compressors or compressor oils are to be removed, ensure that they have been
evacuated to an acceptable level to make certain that
fl
ammable refrigerant does
not remain within the lubricant.
• The evacuation process shall be carried out prior to returning the compressor to the
suppliers.
• Only electric heating to the compressor body shall be employed to accelerate this
process.
• When oil is drained from a system, it shall be carried out safely.
Explanation of symbols displayed on the indoor unit or outdoor unit.
WARNING
This symbol shows that this equipment uses a
fl
ammable
refrigerant.
If the refrigerant is leaked, together with an external igni-
tion source, there is a possibility of ignition.
CAUTION
This symbol shows that the Operation Manual should be
read carefully.
CAUTION
This symbol shows that a service personnel should be
handling this equipment with reference to the Installation
Manual.
CAUTION
This symbol shows that there is information included in the
Operation Manual and/or Installation Manual.
2. ABOUT THE UNIT
2.1. Special tools for R32
WARNING
To install a unit that uses R32 refrigerant, use dedicated tools and piping materials that
have been manufactured speci
fi
cally for R32(R410A) use. Because the pressure of
R32 refrigerant is approximately 1.6 times higher than R22, failure to use dedicated
piping material or improper installation can cause rupture or injury. Furthermore, it can
cause serious accidents such as water leakage, electric shock, or
fi
re.
Do not use a vacuum pump or refrigerant recovery tools with a series motor, since it
may ignite.
9319205151-04_IM.indb 3
9319205151-04_IM.indb 3
1/12/2017 11:49:07 AM
1/12/2017 11:49:07 AM