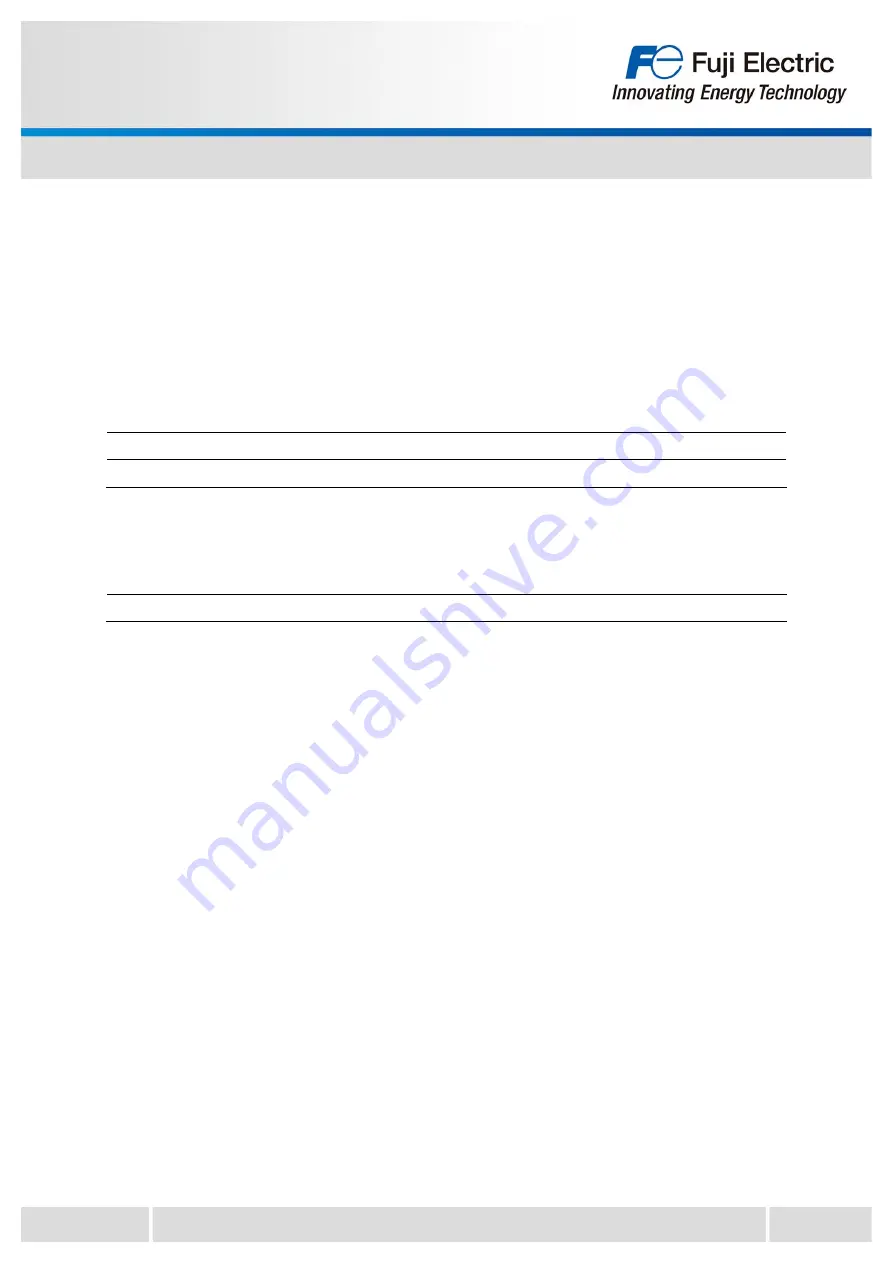
MT6M14904b
© Fuji Electric Co., Ltd. All rights reserved.
CONTENTS
1
2. Related Types
3
3-1. Surface conditions of heat sink
5
3-2. Application of thermal grease
6
3-3. Screw tightening to heat sink
7
3. Mounting to heat sink
5
1. Scope of application
2
4. Mounting the module to printed circuit board
8
4-1. Soldering to printed circuit board
8
4-2. Screw tightening to printed circuit board
9
5. Warning
11
6. Storage and transportation notes
12