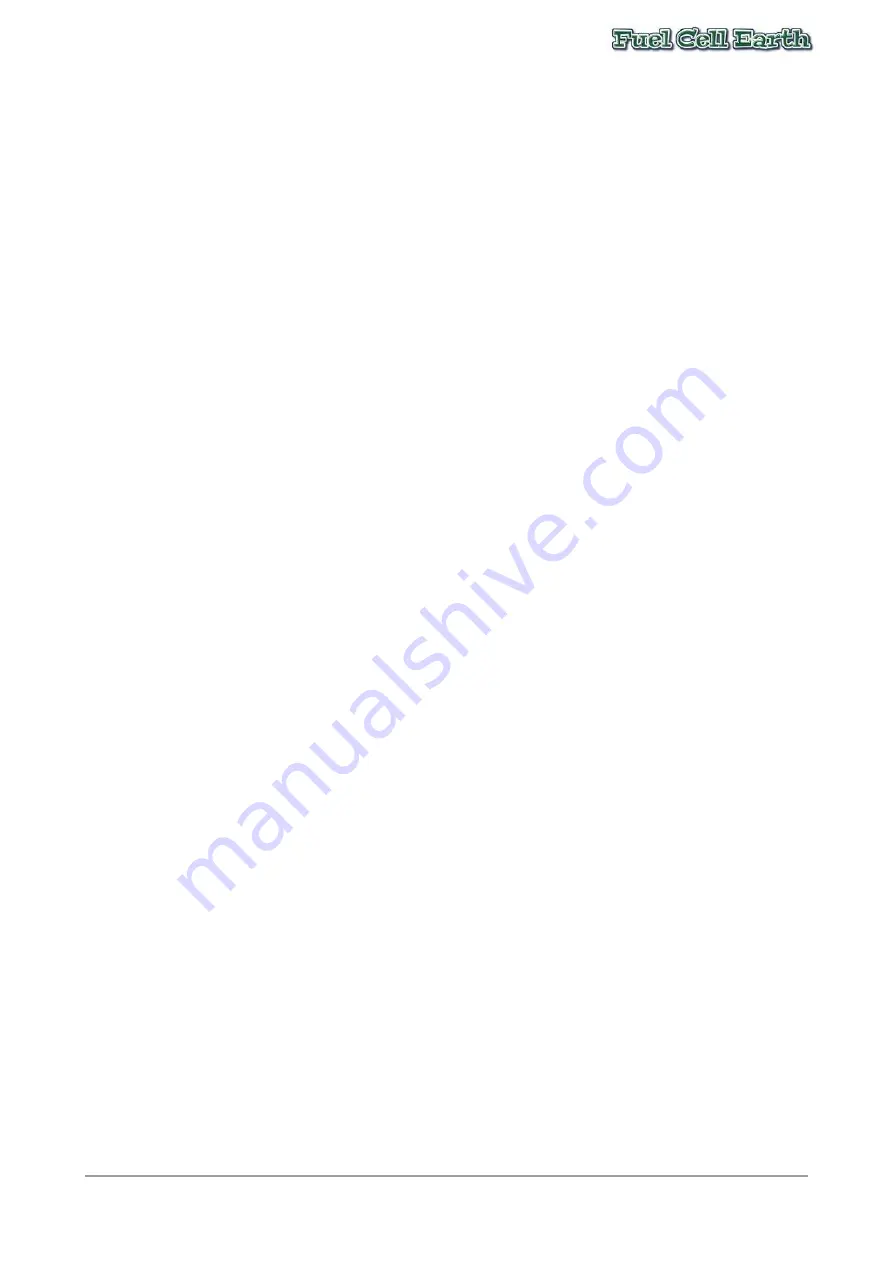
Manual_FCS-C1000_V1.1_EN
5
1.8 High Temperature
The fuel cell stack is designed to operate at 65ºC. At this operating temperature, the air exhaust stream
temperature can reach 55ºC and the cooling air stream can reach 17ºC above ambient conditions. These
temperatures are sufficient to cause burns or severe discomfort. Accordingly, avoid contact with the fuel
cell stack, or components that convey process or cooling air.
WARNING!
Avoid contact with the fuel cell stack or components that convey process or cooling air.
Summary of Contents for H-1000
Page 4: ...Manual_FCS C1000_V1 1_EN 1 1 Safety ...
Page 5: ...Manual_FCS C1000_V1 1_EN 2 ...
Page 6: ...Manual_FCS C1000_V1 1_EN 3 ...
Page 7: ...Manual_FCS C1000_V1 1_EN 4 ...
Page 12: ...Manual_FCS C1000_V1 1_EN 9 ...
Page 13: ...Manual_FCS C1000_V1 1_EN 10 ...
Page 14: ...Manual_FCS C1000_V1 1_EN 11 4 Technical Specification ...
Page 24: ...Manual_FCS C1000_V1 1_EN 21 7 System setup diagram SCU Short Circuit Unit GND Grounding ...
Page 26: ...Manual_FCS C1000_V1 1_EN 23 ...
Page 27: ...Manual_FCS C1000_V1 1_EN 24 ...
Page 31: ...Manual_FCS C1000_V1 1_EN 28 ...
Page 34: ...Manual_FCS C1000_V1 1_EN 31 12 Fuel Cell Drawing ...