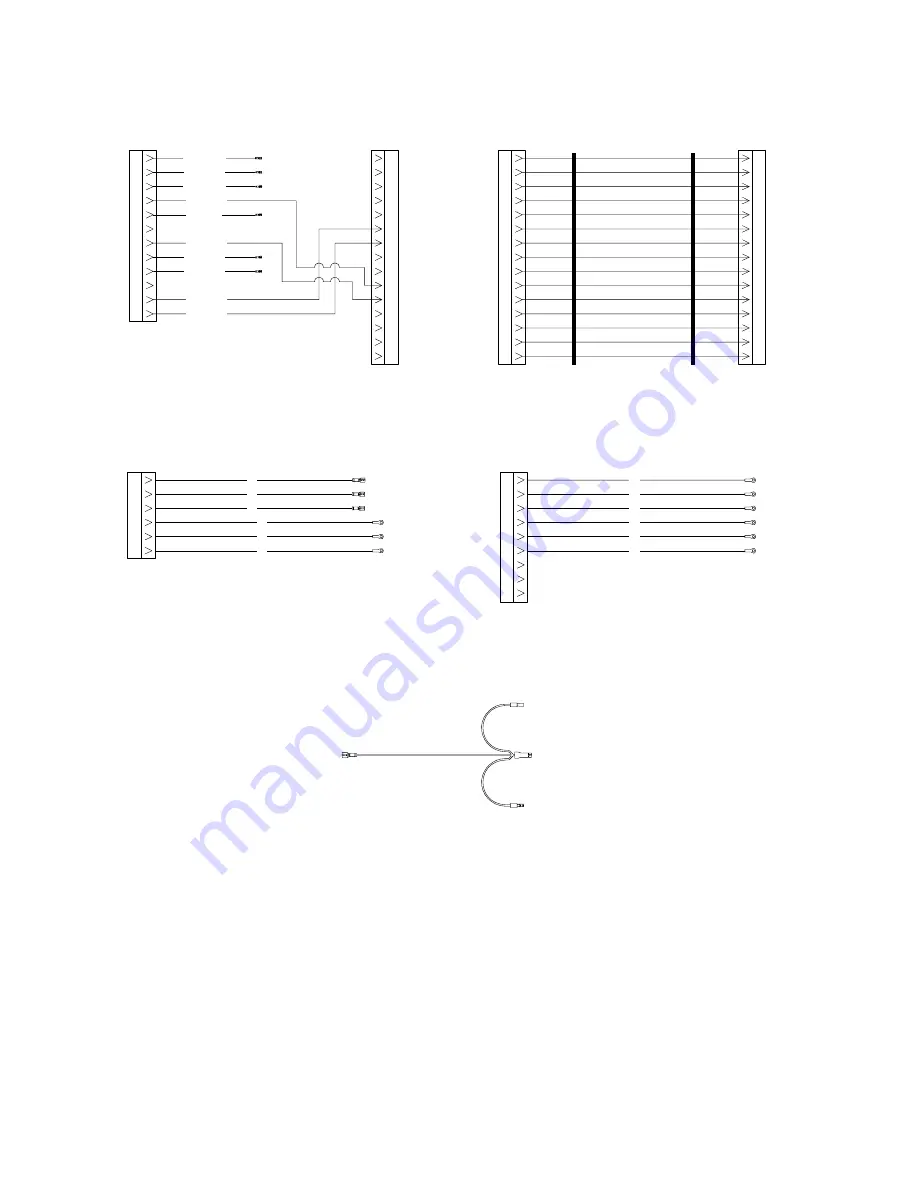
8-8
8.6
Wiring Assemblies and Bundles
CONTACTOR BOX WIRING
8068346
CONTROLLER CABLE ASSEMBLY
(15-Pin Male and Female Connectors, 9-Inches Long)
1
2
3
4
5
6
7
8
9
10
11
12
13
14
15
1
2
3
4
5
6
7
8
9
10
11
12
13
14
15
8068345
J2 WIRING HARNESS
(12-Pin Male and 15-PinFemale Connector, 18-Inches Long)
1
2
3
4
5
6
7
8
9
10
11
12
1
2
3
4
5
6
7
8
9
10
11
12
13
14
15
40C ORG
22C RED
41C ORG
4C RED
76C RED
70C RED
8068243
TRANSFORMER WIRE ASSEMBLY
8067189
LEFT ELEMENT CONTACTOR WIRE ASSEMBLY
(6-Pin Female with 6 Wires)
8067187
RIGHT ELEMENT CONTACTOR WIRE ASSEMBLY
(9-Pin Female with 6 Wires)
WIR0286
WIRE BUNDLE, CONTROLS CIRCUIT
WIR0195
WIRE BUNDLE, HEAT CONTACTOR
WIR0184
WIRE BUNDLE, LATCH CONTACTOR
1H
2H
3H
4H
5H
6H
1
2
3
4
5
6
1H
2H
3H
4H
5H
6H
1
2
3
4
5
6
7
8
9
25C RED
24C RED
27C RED
26C RED