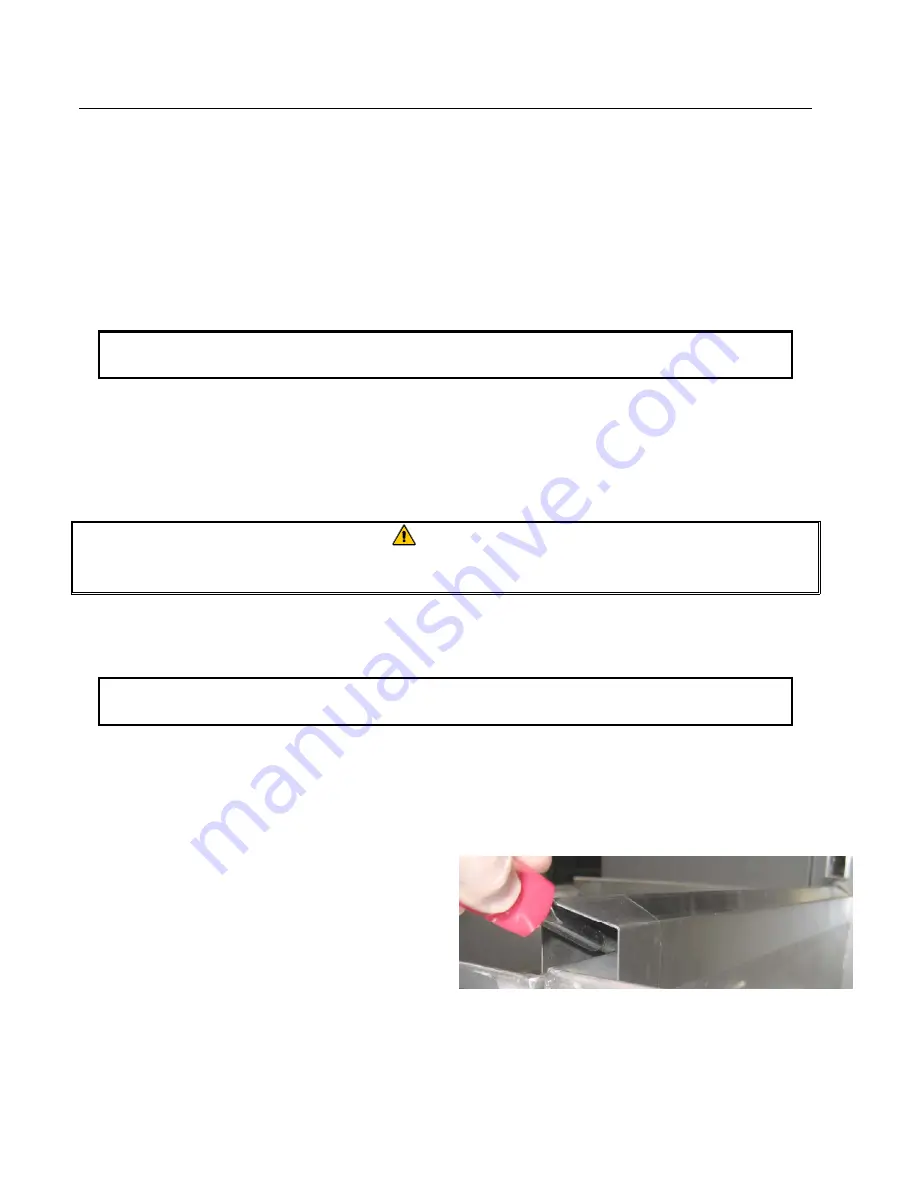
FGP55 SERIES GAS RETHERMALIZERS
CHAPTER 1: SERVICE PROCEDURES
1-12
1.6.6 Replacing the Pilot Assembly
1.
Remove the pilot tubing from the bottom of the pilot assembly.
2.
If the pilot is an electronic ignition pilot, disconnect the ignition cable and the sense wire.
3.
Remove the two pilot mounting screws from the pilot mounting-bracket and remove the pilot.
4.
Reverse the procedure to replace the pilot assembly.
NOTE:
The above procedure is applicable to standing, electronic ignition and trailing
pilot assemblies.
1.6.7 Replacing the Cookpot
1.
Ensure computer and all power switches are off. Drain water from all cookpots prior to moving
rethermalizer.
DANGER
Hot water will cause severe burns. Never attempt to move this appliance when filled
with hot water or to transfer hot water from one container to another.
2.
Turn gas valve off, then turn gas off at supply valve or meter. Disconnect supply line from gas
manifold at rear of rethermalizer.
NOTE:
If restraints are installed on the rethermalizer, disconnect restraints prior to
disconnecting the gas supply line.
3.
Unplug rethermalizer from electrical supply source.
4.
Remove rethermalizer door for access to cabinetry components. Lift door up, disengage rod
from lower door bracket, remove and set door aside.
5.
Remove upper cookpot cover and bracket.
6.
Carefully pry up capping strip if
disassembling an FGP255 with a
screwdriver or similar tool.
Remove capping strip and set
aside.
Removing capping strip.