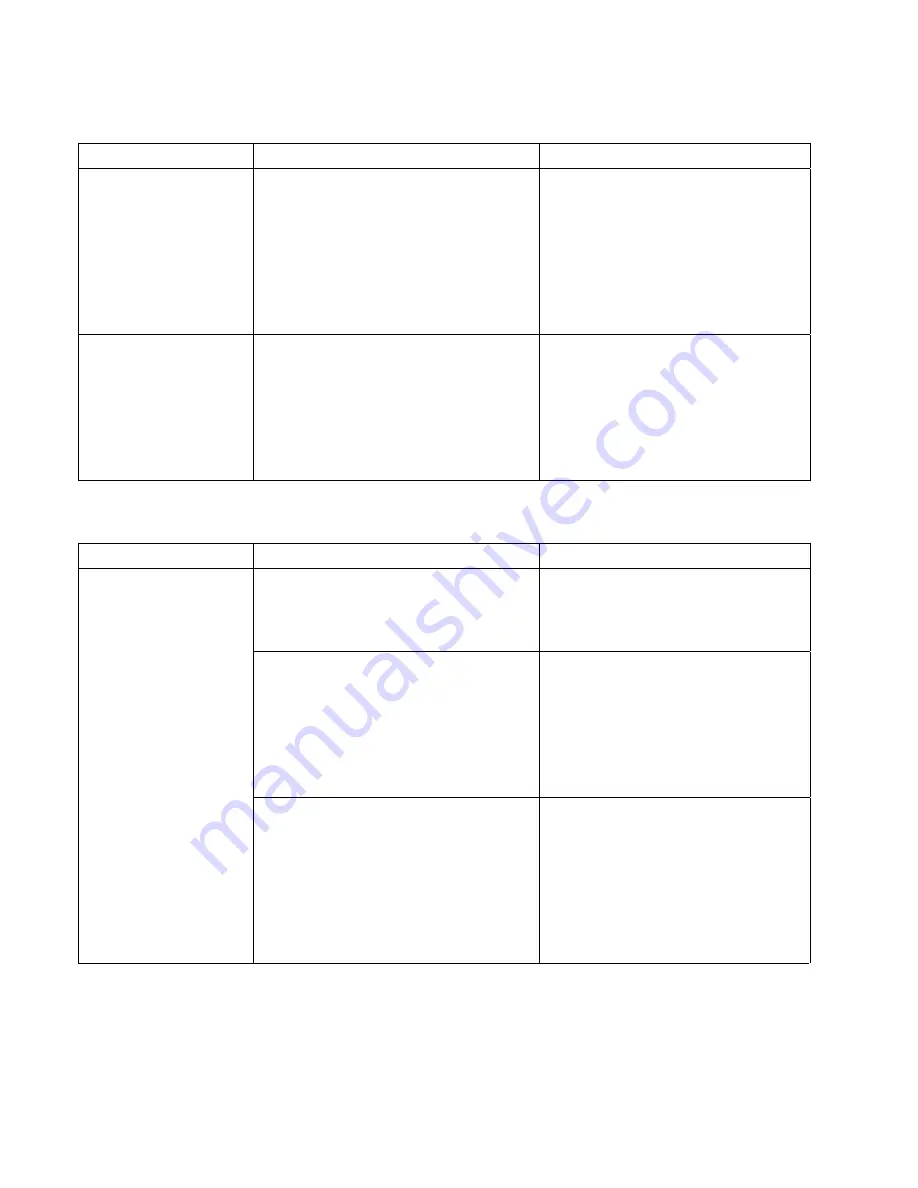
6-4
6.2.2 Error Messages and Display Problems
Problem
Probable Causes
Corrective Action
Controller trouble
light ON.
Oil temperature above acceptable
range or a problem with the
temperature measuring circuitry.
This in an indication of a
malfunction in the temperature
measuring or control circuitry,
including a failure of the high limit
thermostat. Determining the
specific problem is beyond the
scope of operator troubleshooting.
Shut the fryer down immediately.
Controller trouble
light ON and heating
mode light ON.
Open drain valve or problem with
latching circuits
Verify that the drain valve is fully
closed. The fryer will not function
if the drain valve is not fully
closed. If the drain valve is fully
closed, the problem is within the
latching circuitry and is beyond the
scope of operator troubleshooting.
6.2.3 Filtration
Problems
Problem
Probable Causes
Corrective Action
A.
Power cord is not plugged in or
circuit breaker is tripped.
A.
Verify that the power cord is
fully plugged in. If so, verify
that circuit breaker is not
tripped.
B.
Pump motor has overheated
causing the thermal overload
switch to trip.
B.
If the motor is too hot to touch
for more than a few seconds, the
thermal overload switch has
probably tripped. Allow the
motor to cool at least 20
minutes then press the Pump
Reset Switch.
Filter pump won't
start.
C.
Blockage in filter pump.
Test:
Close the drain valve and
pull the filter pan out from the
fryer. Activate the pump. If the
pump motor hums for a short time
then stops, the probable cause is
blockage of the pump itself.
C.
Pump blockages are usually
caused by sediment buildup in
the pump due to improperly
sized or installed filter paper
and failure to use the crumb
screen.
(continued on following page)
Summary of Contents for 8196203
Page 48: ...7 18 7 14 Wiring Diagram Wiring Harness...
Page 59: ...8 10 8 3 2 Drain Valve Assembly and Assoc Parts cont Units with Built In Filtration...
Page 70: ...8 21 8 5 Filtration System Components 8 5 1 FPH17 Filtration Components...
Page 74: ...8 25 8 6 Frypot Assembly and Thermostat Frypot P N 823 5359SP Thermostat P N 806 7543...
Page 75: ...8 26 8 7 Oil Return System Components...