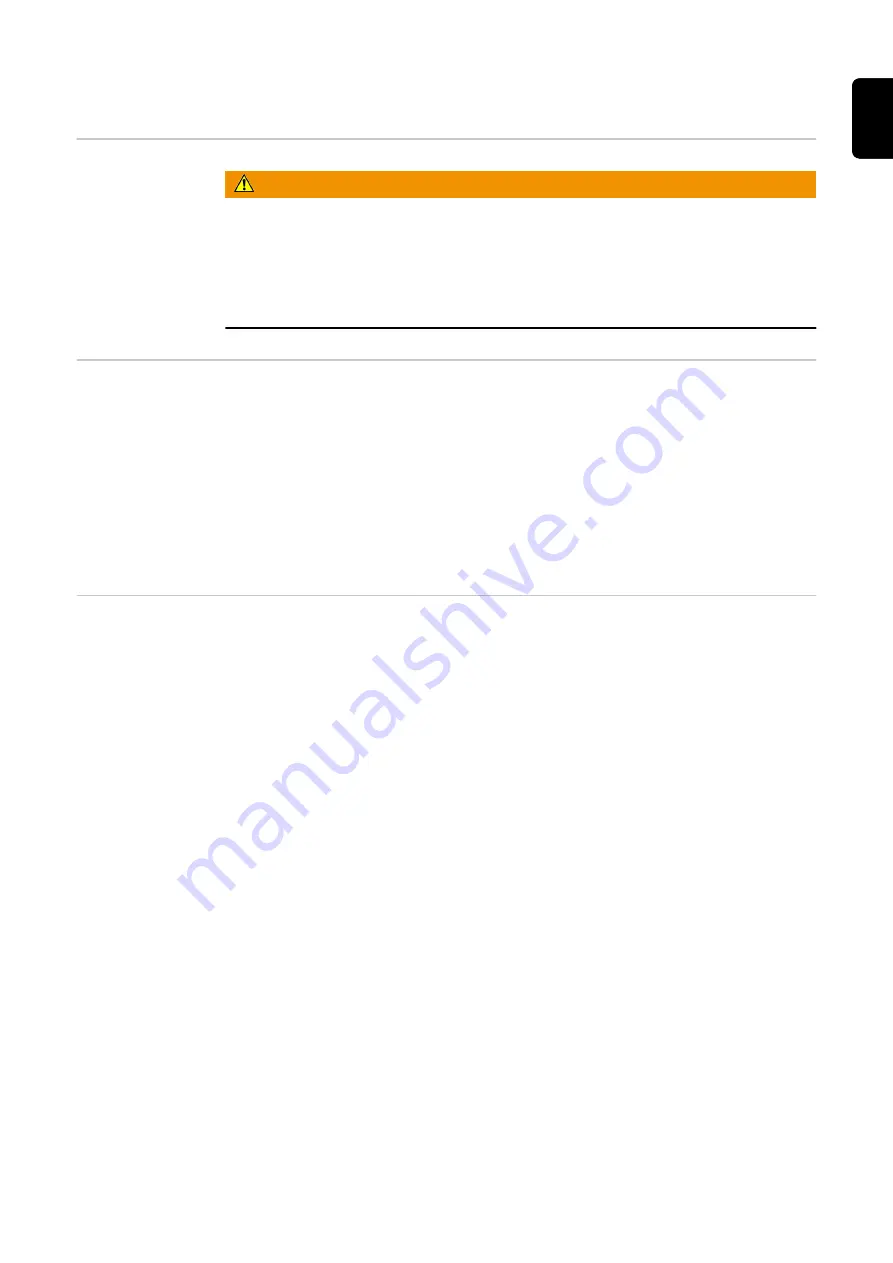
Start-up
Safety
WARNING!
Danger due to incorrect operation and incorrectly performed work.
This can result in severe personal injury and damage to property.
▶
All the functions described may only be used by trained and qualified personnel.
▶
Fully read and understand this document.
▶
Fully read and understand all the Operating Instructions for the system components,
especially the safety rules.
Prerequisites
When commissioning the wire-feed unit, the following requirements must be met:
-
Wire-feed unit connected to the power source using the interconnecting hosepack
-
Welding torch connected to wire-feed unit
-
Feed rollers inserted in the wire-feed unit
-
Wirespool or basket-type spool and adapter inserted in the wire-feed unit
-
Wire electrode threaded in
-
Feed roller contact pressure set
-
Brake adjusted
-
All covers closed, all side panels in place, all protection devices intact and in their
proper place
General
The wire-feed unit is started by pressing the torch trigger (for manual applications) or by
means of a welding start-up signal (for automatic applications).
51
EN
Summary of Contents for WF 25i Case D200
Page 2: ......
Page 16: ...16...
Page 17: ...General 17...
Page 18: ...18...
Page 22: ...22...
Page 23: ...Controls connections and mechan ical components 23...
Page 24: ...24...
Page 32: ...OPT i WF Stand ard control panel 1 9 8 5 6 10 11 12 2 3 4 7 14 13 32...
Page 37: ...Installation and commissioning 37...
Page 38: ...38...
Page 52: ...52...
Page 53: ...Troubleshooting maintenance and disposal 53...
Page 54: ...54...
Page 61: ...Technical data 61...
Page 62: ...62...
Page 65: ...65 EN...
Page 66: ...66...
Page 67: ...67 EN...