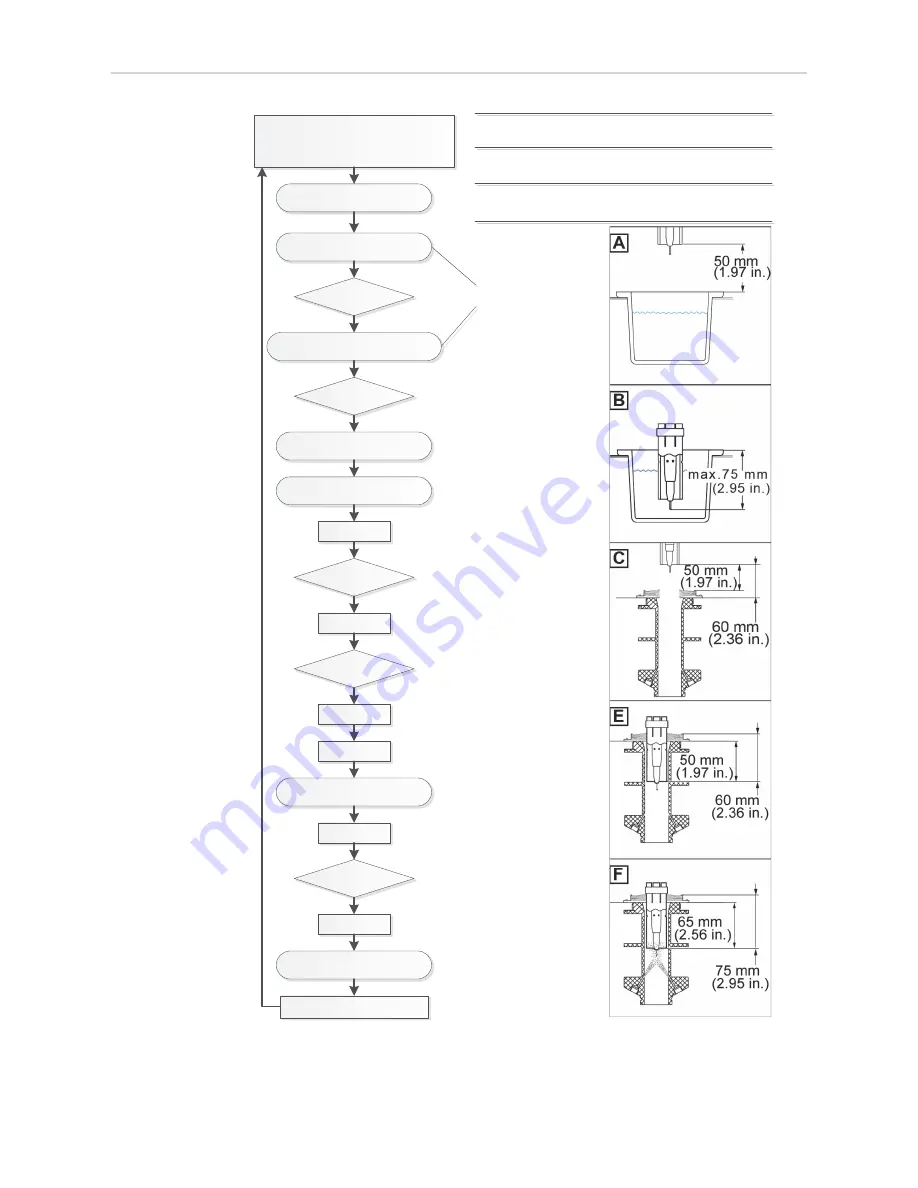
50
Cleaning program
sequence with
dipping bowl
6WDUW
:HOGLQJWRUFK
FOHDQLQJSURJUDP
0RYHWRSRVLWLRQ$
6HW
:DLWV
6HW
:DLWV
5HVHW
5HVHW
0RYHWRSRVLWLRQ&
(QG
6HW5HVHW
%ORZFRPSUHVVHGDLUWKURXJKZHOGLQJWRUFK
6HW5HVHW
6WDUWFOHDQLQJVLJQDO
0RYHWRSRVLWLRQ%
:DLWV
0RYHWRSRVLWLRQ$
:DLWV
0RYHWRSRVLWLRQ&
9
PD[
FPV
LSP
6HW5HVHW
6SUD\SDUWLQJDJHQWVLJQDO
0RYHWRSRVLWLRQ(
6HW
:DLWV
5HVHW
0RYHWRSRVLWLRQ)
Summary of Contents for Robacta TC 2000
Page 2: ...2 ...
Page 4: ...4 ...
Page 15: ...General ...
Page 16: ......
Page 25: ...Controls connections and mechani cal components ...
Page 26: ......
Page 34: ...34 ...
Page 35: ...Installation and commissioning ...
Page 36: ......
Page 41: ...41 EN 4 Tightening torque 1 3 Nm 5 Tightening torque 0 5 Nm 6 4 5 6 ...
Page 55: ...Troubleshooting maintenance and disposal ...
Page 56: ......
Page 62: ...62 ...
Page 63: ...Technical data ...
Page 64: ......
Page 66: ...66 ...
Page 67: ...Appendix ...
Page 68: ...68 Spare parts list Robacta TC 2000 ...
Page 69: ...69 ...
Page 70: ...70 ...