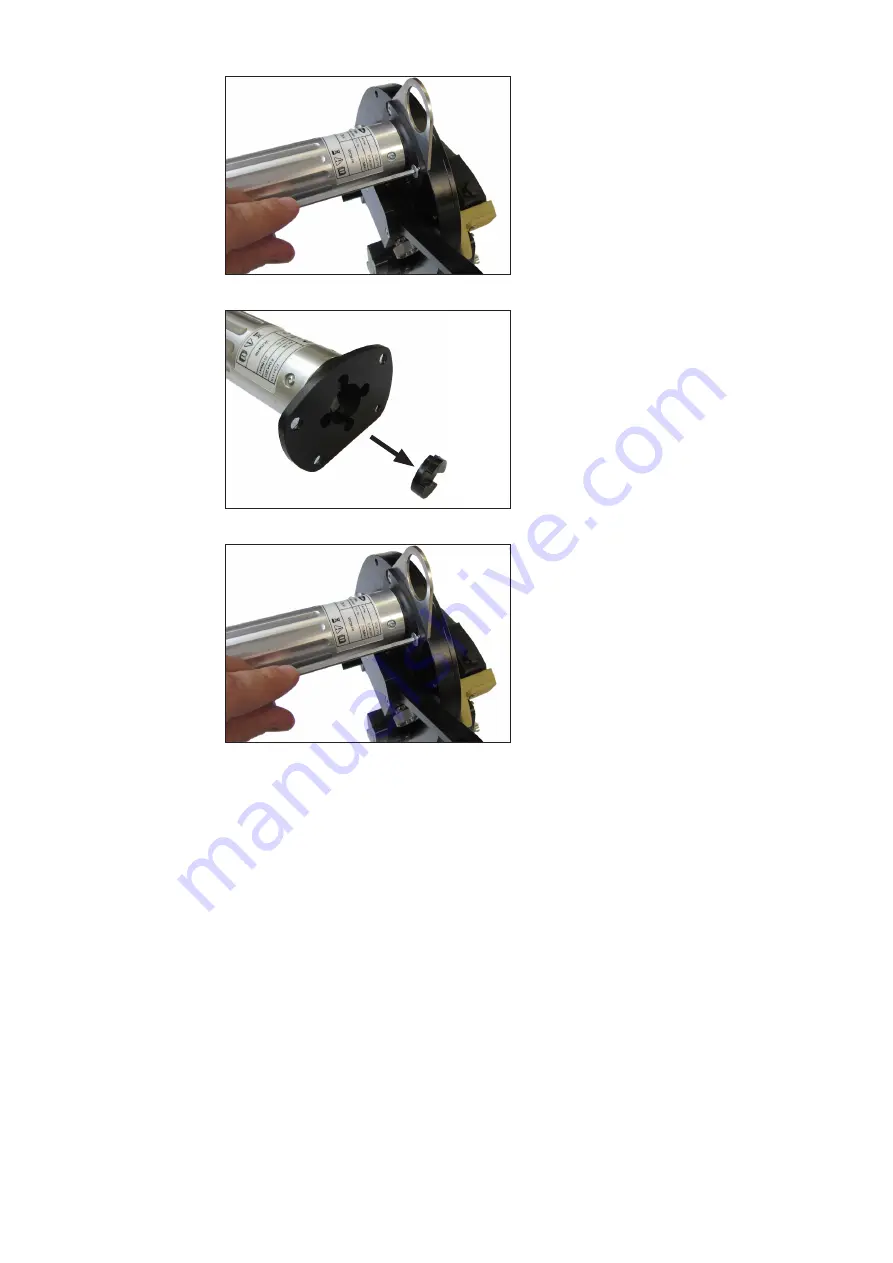
64
Replacing the
plastic coupling
1. Use an Allen key (3 mm) to
unscrew the retaining bolts of the
drive motor.
2. Pull the drive motor out of the
housing.
3. Remove the faulty coupling.
4. Fit the new coupling to the drive
motor.
5. Push the drive motor back into the
housing.
6. Retighten the retaining bolts of the
drive motor using an Allen key.
4x
Summary of Contents for FOH 10-76
Page 2: ......
Page 4: ...4...
Page 8: ...8...
Page 9: ...9 General information...
Page 10: ...10...
Page 22: ...22...
Page 23: ...23 Safety...
Page 24: ...24...
Page 30: ...30...
Page 31: ...31 Description of the open weld heads...
Page 32: ...32...
Page 41: ...41 Commissioning...
Page 42: ...42...
Page 49: ...49 Operation...
Page 50: ...50...
Page 56: ...56...
Page 57: ...57 Troubleshooting maintenance and disposal...
Page 58: ...58...
Page 65: ...65 Technical data...
Page 66: ...66...
Page 70: ...70...
Page 71: ...71 Spare parts circuit diagram...
Page 72: ...72...
Page 86: ...86 Wire adjustment unit FOH Orbital welding torch TTWO 2000 F 58 0913 7000...
Page 87: ...87 Wire feeding Orbital TTWO 2000 38 0100 0440 Extension hose pack FCH FOH 10m...
Page 94: ...94 FRONIUS INTERNATIONAL GMBH TechSupport Automation www fronius com addresses www fronius com...