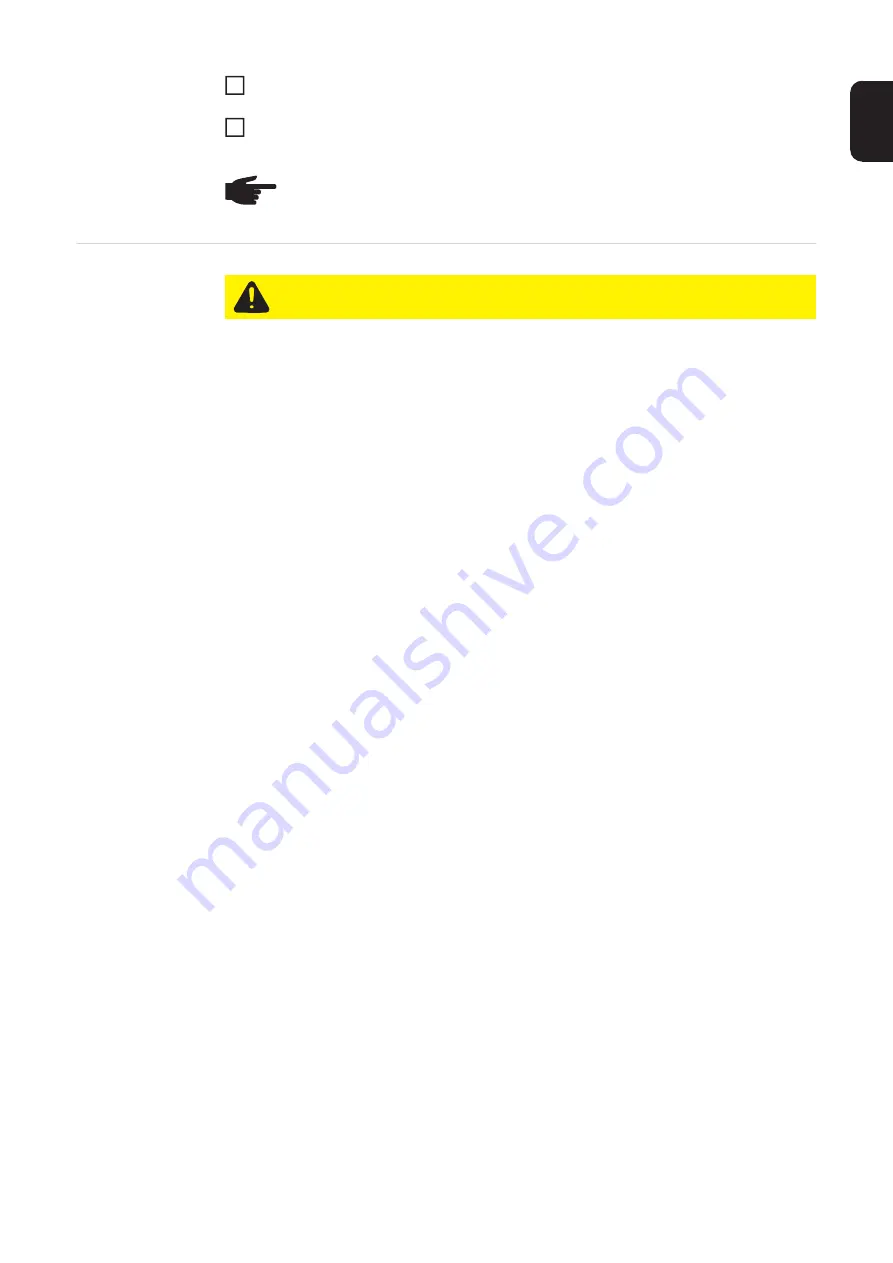
29
EN
Switch mains switch of the power source(s) in position “I” - the cooling pump starts op-
eration.
Check coolant flow until proper flow is ensured. If necessary, deairate coolant circula-
tion.
Changing the
welding torch
NOTE!
During welding check coolant flow at regular intervals - a proper return
flow must be visible in the filler neck.
2
3
CAUTION!
Excess pressure will damage the cooling unit. Before blowing out the
welding torch with compressed air, undo the screw cap on the fill nozzle.