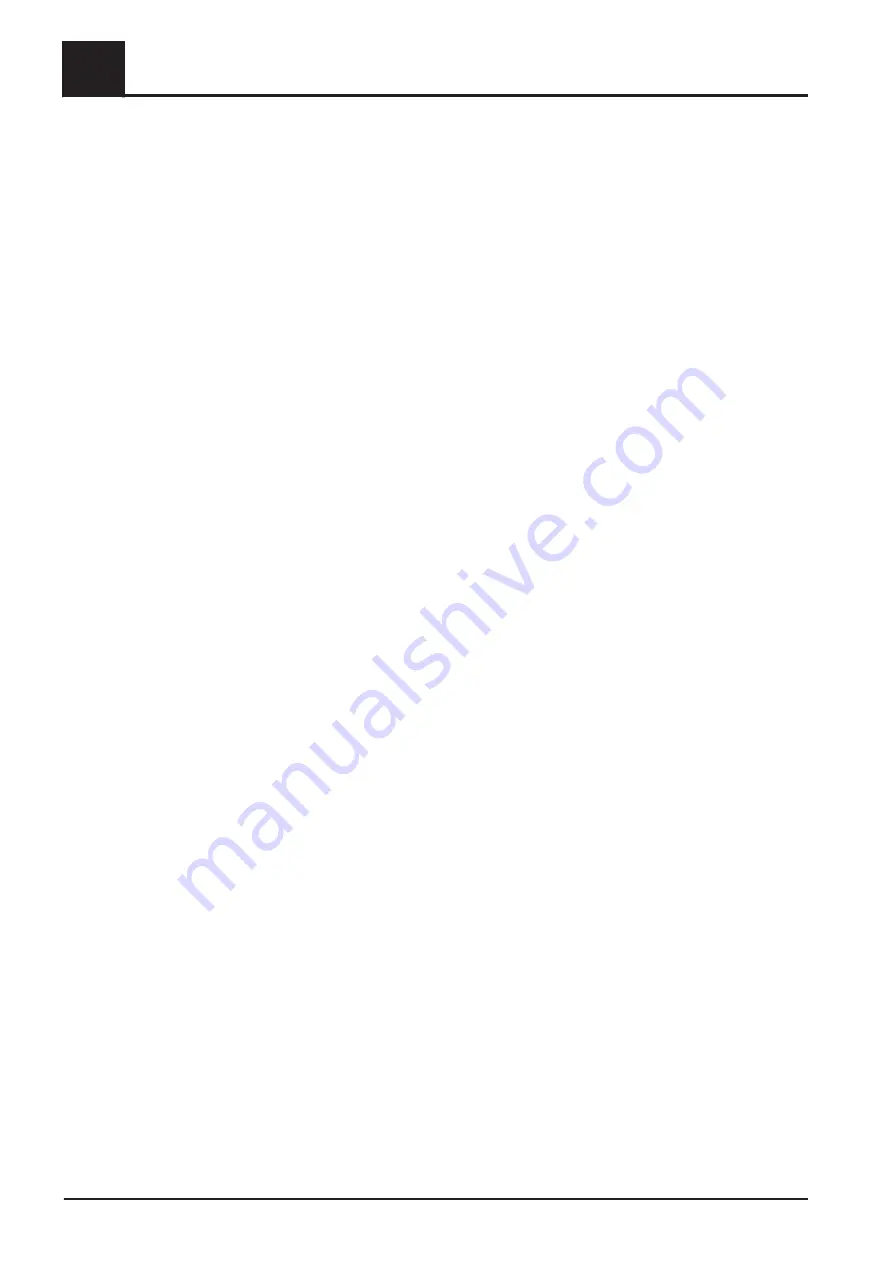
Table of contents
The Clean Air Act 1993 and Smoke Control Areas
Qualification of operating staff
Protective equipment for operating staff
Hydraulic chamber safety switch
Notes for operating a heating system
Installation and approval of the heating system
General information for installation room (boiler room)
Requirements for central heating water
Notes for using pressure maintenance systems
Chimney connection/chimney system
Filling/refilling the store with fuel
Loading of fuel for a partially emptied store with rotary agitator
Loading wood chips in an empty store (not under pressure)
Blowing in pellets for a store with pellet screw
Blowing in fuel for a partially emptied store with rotary agitator
Blowing in fuel for an empty store with rotary agitator
Table of contents
2
Froling GesmbH | A-4710 Grieskirchen, Industriestraße 12 | www.froeling.com