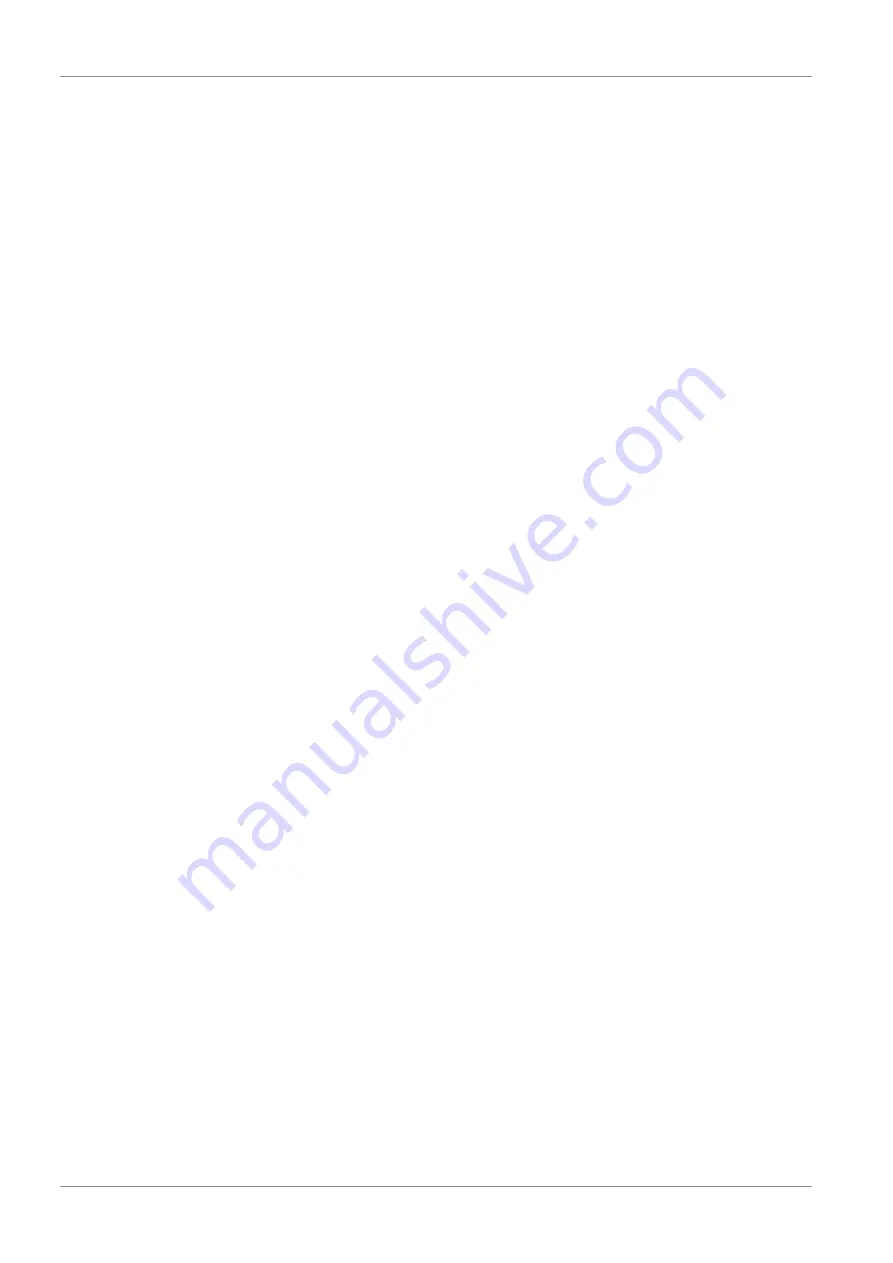
1 | General
4
B1510622_en | Operating instructions Firewood boiler S4 Turbo
1 General
Thank you for choosing a quality product from Froling. The product features a state-of-
the-art design and conforms to all currently applicable standards and testing
guidelines.
Please read and observe the documentation provided and always keep it close to the
system for reference. Observing the requirements and safety information in the
documentation makes a significant contribution to safe, appropriate, environmentally
friendly and economical operation of the system.
The constant further development of our products means that there may be minor
differences from the pictures and content. If you discover any errors, please let us
know: [email protected].
Subject to technical change.
Warranty and Guarantee Conditions
Our sale and delivery conditions will be applicable. These conditions have been made
available to customers, and customers have been made aware of them at the time of
order completion.
You can also find the guarantee conditions on the enclosed guarantee certificate.
1.1 Operating principle
The Froling S4 Turbo is a wood boiler for the non-condensing combustion of firewood.
The fuel loading chamber is filled with fuel via the fuel loading door located behind the
heat insulated door on the front of the boiler. The combustion grate, through which the
combustion gases are sucked into the combustion chamber by the induced draught
fan, is located below the fuel loading chamber. When the induced draught fan is used,
the combustion air around the pre-heating chamber door is sucked in and channelled
to the fuel via regulating flaps on the side air boxes (primary and secondary air). The
boiler water and flue gas temperature are regulated by the induced draught fan. The
primary air is used to adjust the boiler to the fuel and set the required output. The
secondary air is used to set the combustion performance by way of the Lambda probe
and servo-motor. The flue gas travels through the heat exchanger to the flue gas
outlet. In order to optimise heat transfer and for cleaning purposes, the heat
exchanger pipes are fitted with an Efficiency Optimisation System (WOS), which can
be operated using a lever or activated via a drive. The ash deposits at the bottom of
the combustion chamber and below the heat exchanger pipes can be removed via the
combustion chamber door on the front of the boiler.