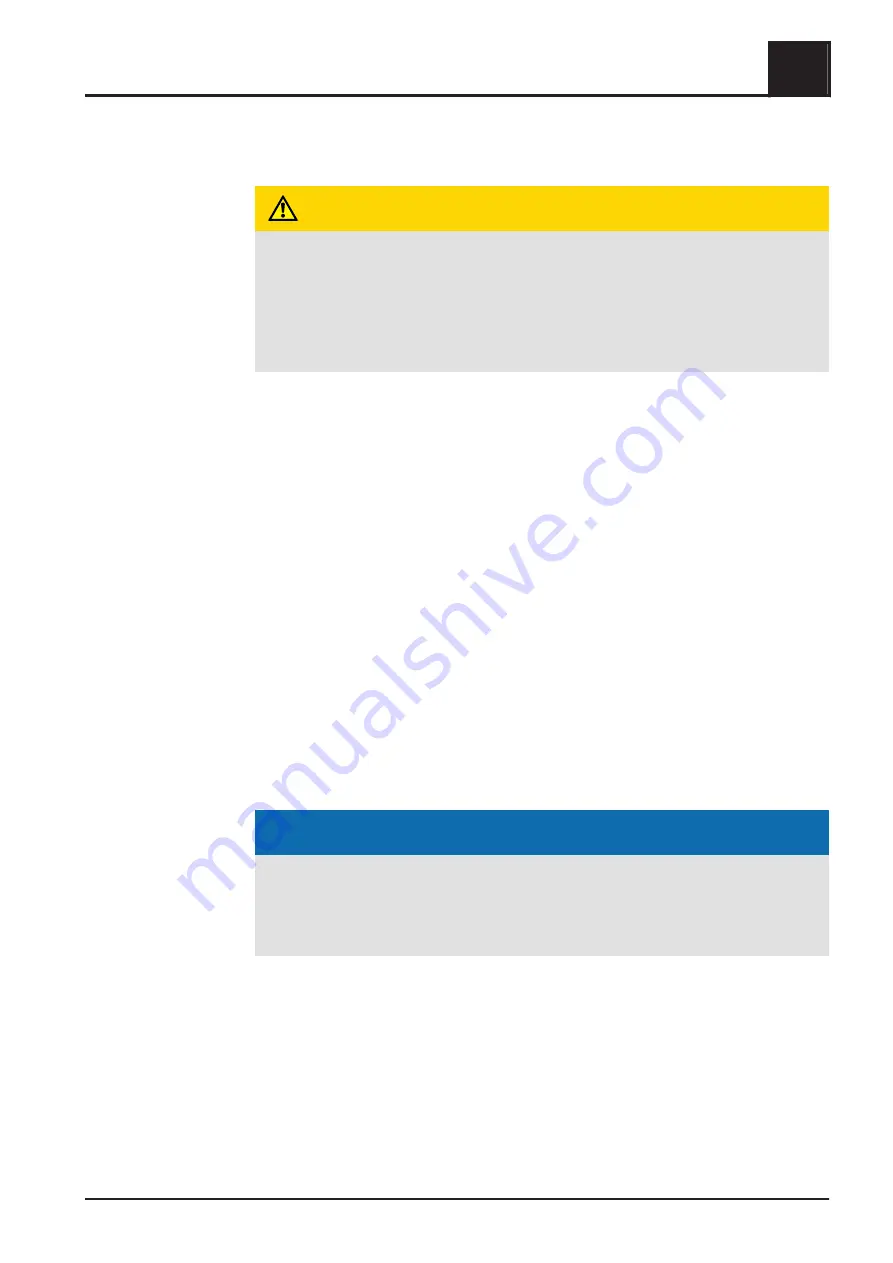
5.6 Maintenance work by technicians
CAUTION
If maintenance work is carried out by untrained personnel:
Risk of personal injury and damage to property!
The following applies for maintenance:
❒ Observe the instructions and information in the manuals
❒ Only allow appropriately qualified personnel to work on the system
Only qualified staff are permitted to carry out maintenance work in this chapter:
▪ Heating technicians / building technicians
▪ Electrical installation technicians
▪ Froling customer services
The maintenance staff must have read and understood the instructions in the
documentation.
NOTICE! We recommend a yearly inspection by Froling customer services or an
authorised partner (third party maintenance).
Regular maintenance and servicing by a heating specialist will ensure a long, trouble-
free service life for your heating system. It will ensure that your system stays
environmentally-friendly and operates efficiently and cost-effectively.
In the course of this maintenance the entire system is inspected and optimised,
particularly regulation and control of the boiler. The emission measurement carried out
can also be used to draw conclusions about the combustion performance of the boiler.
For this reason, FROLING offers a service agreement, which optimises operating
safety. Please see the details in the accompanying guarantee certificate.
Your Froling customer service office will also be happy to advise you.
NOTICE
All national and regional regulations relating to regular testing of the system must
be observed. Please be advised that, in Austria, commercial systems with a rated
heat output of 50 kW or more must be regularly tested at yearly intervals in
accordance with the Heating Plant Regulations (Feuerungsanlagen-Verordnung).
Servicing the system
5
Maintenance work by technicians
Operating Instructions PE1 Pellet 7-35 / PE1 Pellet Unit 7-20 | B1001020_en
59