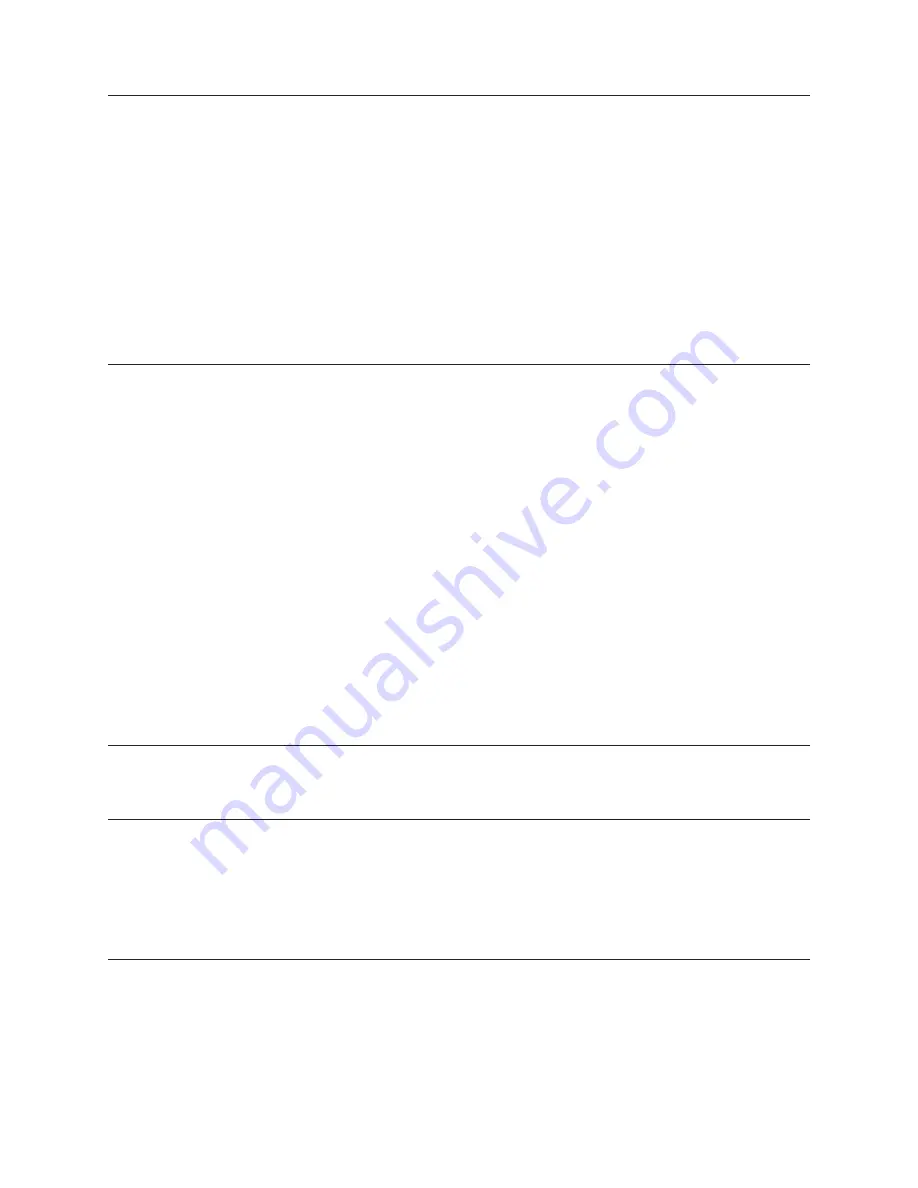
FL2 S
erieS
P
umP
9
S
tart
-
up
c
heck
-
LiSt
1. Make sure that the pump and piping system are clear of any foreign matter.
Do not use the
pump to flush the system
.
2. Make sure that the pump and drive are properly lubricated. Check the lubrication section
(page 4) in this manual for the pump. See instructions from the drive manufacturer for the
drive.
3. Check to make sure that all guards are in place and secure.
4. Check for proper pump and drive rotation. Make sure that the pump is flooded with product
when checking the rotation. Running the pump dry even momentarily can cause seal damage.
5. Check that all valves on the discharge side are open to prevent over-pressurizing the pump.
Do not rotate the shafts with the cover removed. Rotors and housing could be damaged.
c
Leaning
r
ecommenDationS
When you are running products or cleaning solutions with different temperatures, you need
to allow enough time for all of the wetted components inside the pump to reach a steady-state
temperature before you start the pump. If your process does not allow you to stop the pump
during this transition, you need to install rotors that provide larger clearances. Please contact
your Fristam representative for assistance.
If the process lines are to be cleaned with the pump, use a by-pass loop around the FL2 pump
during the CIP mode to maintain pip velocity. Once the wetted components are at a steady
temperature, the pump can be started and run around 100 RPM with a backpressure of at least
10 PSI. As the product viscosity increases, the required backpressure may need to be increased
as well.
Contact Fristam if you have any questions.
r
ecommenDeD
p
reventive
m
aintenance
r
ecommenDeD
t
orque
v
aLueS
Table A2, page 5.
r
ecommenDeD
S
eaL
m
aintenance
Visually inspect the mechanical seal regularly for leakage.
Annually replace the mechanical seal under normal conditions.
Replace the mechanical seal as often as required under severe conditions (abrasive product,
dry running, etc.).
e
LaStomer
i
nSpection
Inspect all elastomers when performing pump maintenance. We recommend replacing elasto-
mers (o-rings and gaskets) during mechanical seal replacements.
Model 15: If the rotor bolt o-ring, rotor washer o-ring, or rotor o-ring fails, the threaded hole
on the end of the shaft and the rotor bolt threads will need to be cleaned. We recommend
removing the rotors and rotor bolts/washers while the pump is being CIP’d. This will ensure
that the internal threads are cleaned before production resumes. We recommend cleaning the
external threads on the rotor bolt with a wire brush.