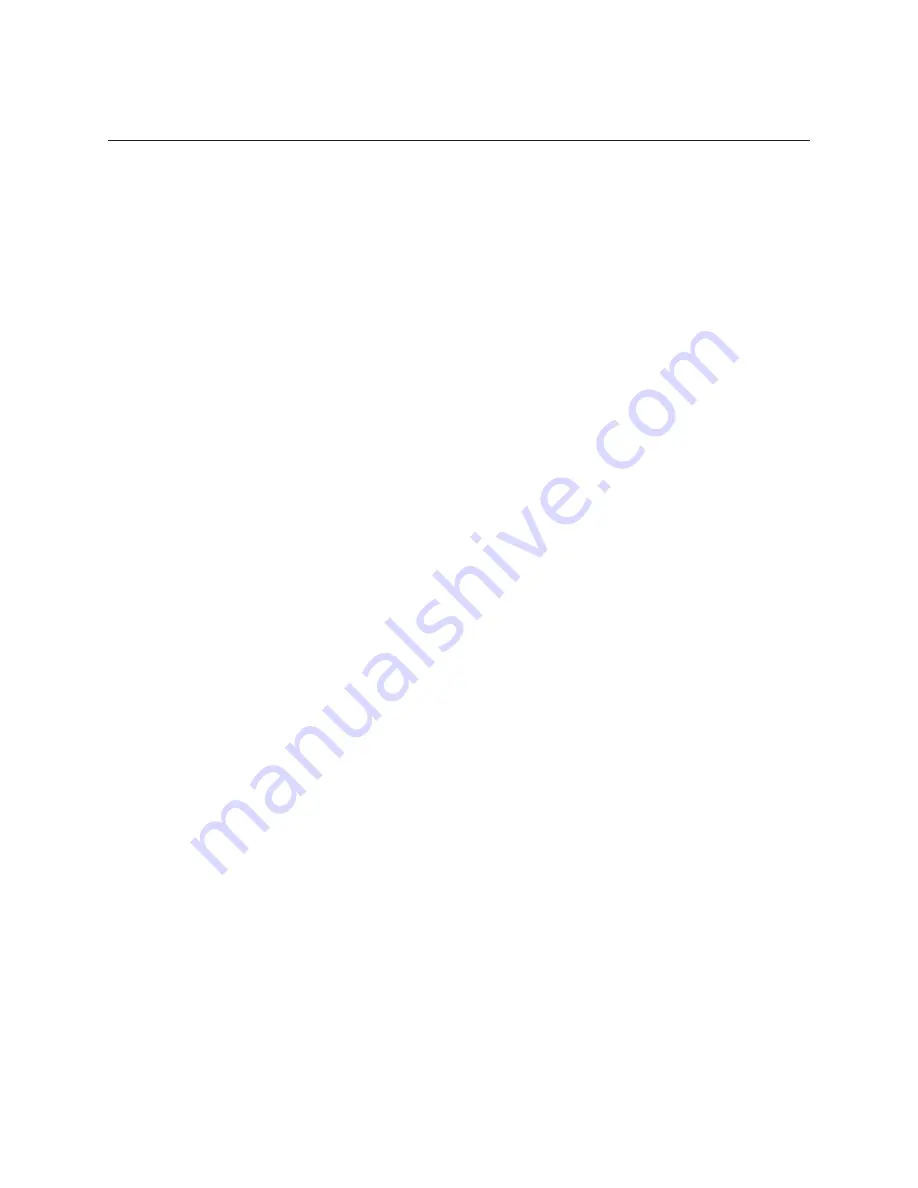
F
riStam
P
umPS
36
t
roubLeShooting
p
robLem
c
auSe
S
oLution
Pump not turning
Interruption of electrical power.
Reset circuit breaker,
check fuses.
Keys sheared or missing.
Replace.
Coupler or belts are not connected.
Replace or adjust.
Pump shaft or gears sheared.
Replace.
Wrong rotation.
Reverse.
Relief valve not properly adjusted.
Adjust valve.
Pump not priming
Valve closed in suction line.
Open valve.
Suction line clogged or restricted.
Clear suction line.
Air leak in connections or seal.
Repair leak.
Pump speed too slow.
Increase speed.
Suction line does not remain flooded. Install foot valve.
Air lock.
Bleed suction line.
Excessive clearances in pump.
Replace out of tolerance
parts.
NIPA low.
Increase suction pressure.
Insufficient flow
Speed too low.
Adjust speed as required.
Air leak.
Repair leak.
Noisy operation
Cavitation.
Increase NIPA.
Viscous product.
Slow pump, reduce product.
High vapor pressure, high temp.
Reduce temperature.
Leaks in piping or pump.
Repair leaks.
Dissolved gas in product.
Reduce discharge pressure.
Mechanical noise.
Check tolerances.
Excessive weight from piping,
Support piping.
pump body distorted.
Excessive discharge pressure.
Reduce discharge pressure.
Worn bearing.
Replace bearing.
Worn gears.
Replace gears.
Rotor-to-rotor contact.
Time rotors, replace twisted
shafts, replace worn gears.
Pump overloads
Viscosity of product higher than
Reduce pump speed,
expected. increase piping size.
Higher pressure than expected
Reduce pump speed,
increase piping size.
Play between gears
Worn gear teeth.
Replace gear.
Gear loose on shaft.
Inspect gear key, keyway and
shaft. If all are undamaged,
retighten the gear retaining
nut.
Check for backlash.