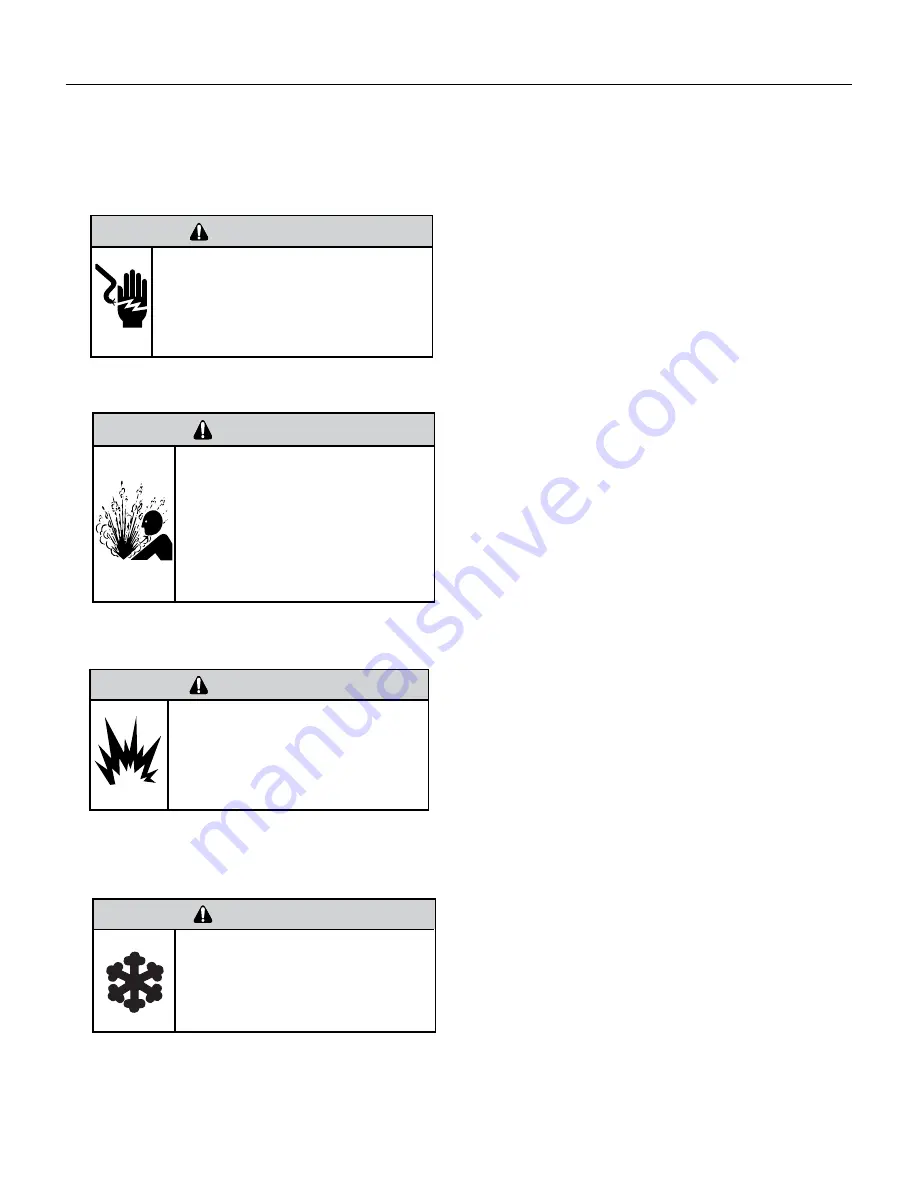
79
PB
COMPONENT TESTING
Compressor Replacement
WARNING
ELECTRIC SHOCK HAZARD
Turn off electric power before service or
installation. Extreme care must be used, if it
becomes necessary to work on equipment with
power applied.
Failure to do so could result in serious injury or
death.
WARNING
HIGH PRESSURE HAZARD
Sealed Refrigeration System contains refrigerant
and oil under high pressure.
Proper safety procedures must be followed,
and proper protective clothing must be worn
when working with refrigerants.
Failure to follow these procedures could
result in serious injury or death.
1. Be certain to perform all necessary electrical and refrigeration
tests to be sure the compressor is actually defective before
replacing.
2. Recover all refrigerant from the system though the process
tubes.
PROPER HANDLING OF RECOVERED REFRIGERANT
ACCORDING TO EPA REGULATIONS IS REQUIRED
. Do not use
gauge manifold for this purpose if there has been a burnout. You
will contaminate your manifold and hoses. Use a Schrader valve
adapter and copper tubing for burnout failures.
3.After all refrigerant has been recovered, disconnect suction and
discharge lines from the compressor and remove compressor. Be
certain to have both suction and discharge process tubes open to
atmosphere.
4. Unbolt the compressor at 3 places. Replace grommets under
mounting bolts if they are worn out.
5.Carefully pour a small amount of oil from the suction stub of the
defective compressor into a clean container.
6.Using an acid test kit (one shot or conventional kit), test the oil
for acid content according to the instructions with the kit.
7.If any evidence of a burnout is found, no matter how slight, the
system will need to be cleaned up following proper procedures.
8.Install the replacement compressor.
9. Pressurize with a combination of R-410A and nitrogen and leak
test all connections with an electronic or Halide leak detector.
Recover refrigerant and repair any leaks found.
9a. If leak detector is unavailable remove all refrigerant from
system and pressurize with nitrogen to 350 psi. Check that system
holds pressure.
Repeat Step 9 to insure no more leaks are present
10. Evacuate the system with a good vacuum pump capable
of a final vacuum of 200 microns or less. The system should
be evacuated through both liquid line and suction line gauge
ports. While the unit is being evacuated, seal all openings on
the defective compressor. Compressor manufacturers will void
warranties on units received not properly sealed. Do not distort
the manufacturers tube connections.
11. Recharge the system with the correct amount of refrigerant.
The proper refrigerant charge will be found on the unit rating
plate. The use of an accurate measuring device, such as a
charging cylinder, electronic scales or similar device is necessary.
WARNING
EXPLOSION HAZARD
The use of nitrogen requires a pressure
regulator. Follow all safety procedures and
wear protective safety clothing etc.
Failure to follow proper safety procedures
could result in serious injury or death.
FREEZE HAZARD
Proper safety procedures must be followed,
and proper protective clothing must be worn
when working with liquid refrigerant.
Failure to follow these procedures could
result in minor to moderate injury.
CAUTION
Summary of Contents for FRESHAIRE PVH09K3FA
Page 98: ...98 WIRING DIAGRAMS Figure 801...