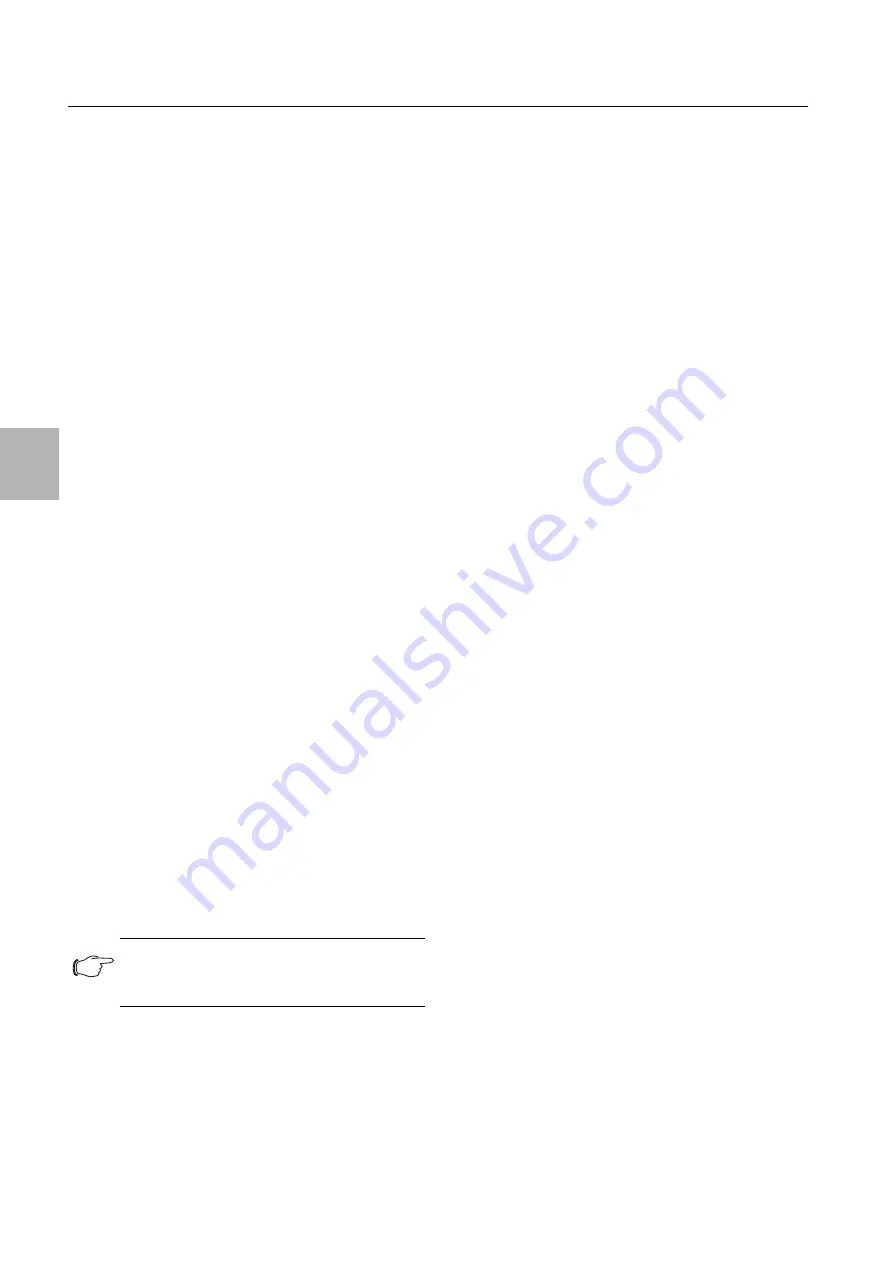
6 Installation
6
24
Rittal Liquid Cooling Package
5. Before soldering the last connection, open one
screwed union, to prevent overpressure in the piping
system. Upon soldering retighten the connection!
6. As an alternative to soldering you may use crimping.
However, limit crimped connections to annealed
pipes with a diameter of max. 20 mm! After cutting
the pipes, slightly open the pipe to the correct inside
diameter. The crimps must be tightened to the cor-
rect torque using a torque wrench.
Low-temperature insulation of the liquid lines
1. Liquid cooling outside of the building with low-tem-
perature insulation to DIN 4140 made from UV-re-
sistant HT/Armaflex or an equivalent material.
2. A wall thickness of 9 mm is recommended.
Low-temperature insulation of the hot-gas line
1. The gas line must be insulated indoors (contact haz-
ard protection).
Leak test / conducting the leak test
The system must undergo leak testing as a complete
system. Following completion of the system, the test
should be carried out at the site of installation.
Multiple techniques may be used to test for leaks, de-
pending on the manufacturing conditions, such as pres-
surisation with inert gas, or leak detection using radioac-
tive gas. In order to avoid emissions of hazardous sub-
stances, the pressure test may be carried out with inert
gas such as nitrogen, helium or carbon dioxide. Oxy-
acetylene and hydrocarbons must not be used for safety
reasons. Air and gas mixtures are to be avoided, since
certain mixtures may be hazardous.
A vacuum technique may be used for a rough indication
of leaks. In order to ensure proper functioning of the
cooling system, the manufacturer must specify suitable
criteria for the vacuum technique.
The manufacturer must select a test method which al-
lows suitable results to be achieved in accordance with
the requirements outlined below.
Connections must be checked with a detector or using
a technique with a detection sensitivity as described in
EN 1779 with a bubble test (application of liquid) if the
test pressure is 1 x PS.
The manufacturer must verify that the test method used
complies with the aforementioned requirements.
EN 1779:1999 may be used as a basis for this test.
The detector must be calibrated at regular intervals as
per the manufacturer's instructions.
Any leak detected must be repaired and subjected to a
further leak test.
1. Systems with dry nitrogen should be tested at an
overpressure of at least 28 bar. The Rotalock valves
on the intake and pressure sides of the compressors
must be closed. This ensures the compressor is not
subjected to the test pressure.
2. Check the system for tightness. We recommend to
inspect all connections for tightness, including
screwed joints, by spraying with Nekal spray.
Evacuating
1. Upon successful pressure testing, the air still re-
maining in the system must be removed. To do so,
connect a vacuum pump and evacuate the system
to a pressure of <0.3 mbar (absolute pressure).
2. If at all possible evacuate from both ends of the
compressor, that is from the intake and the pressure
side.
3. Fill the system with dry nitrogen and repeat the evac-
uation. This removes air and remaining moisture
from the system.
Filling with refrigerant, cooling system in a vacuum
1. The system must only be filled gravimetrically (i.e. by
weight) using refrigerant as the liquid in the liquid
line. Fill liquid R410A only until the fill quantity corre-
sponds as precisely as possible to the maximum fill
weight as per the rating plate. Thereafter switch the
unit on and, while it runs, continue filling carefully
and slowly from the intake side of the compressor,
until no more bubbles are visible at the sight glass.
The maximum fill weight as per the rating plate must
not be exceeded.
2. Note the refrigerant volume filled in on the rating
plate.
3. Refrigerant filling volumes for unit and condenser
see technical data. Determine the refrigerant filling
volume for the piping system from the individual
lengths and interior diameters of the refrigerant lines.
4. The weight of the refrigerant volume actually filled in
is determined during filling by means of a refrigerant
bottle.
6.3
Connecting the condensate discharge
Any condensate which may develop is collected in the
condensate collecting tray (fig. 9, item 8) beneath the
heat exchanger.
Note:
Lower test pressures are admissible, provid-
ed there is an equivalent detection sensitivity.