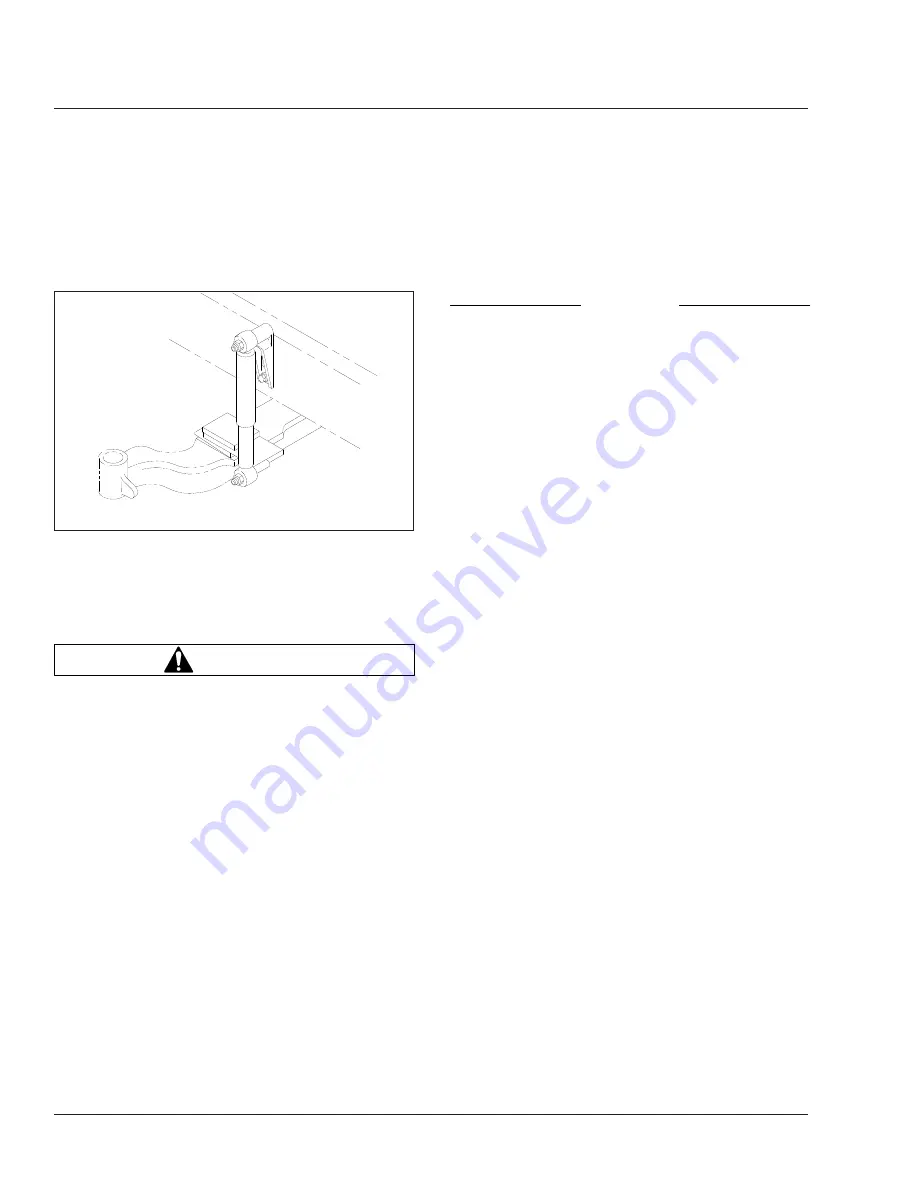
Inspect the shock absorber for oil leakage. If the
shock absorber is damaged or leaking, replace it with
a new one. See
Group 32
of the
Century Class
Trucks Workshop Manual
for replacement
instructions.
Rear Suspension Check
Freightliner Spring Suspension
WARNING
Do not replace individual leaves of a damaged leaf
spring assembly; replace the complete spring as-
sembly. Visible damage (cracks or breaks) to one
leaf causes hidden damage to other leaves. Re-
placement of only visibly damaged parts is no as-
surance that the spring is safe. Failure to replace
a damaged spring assembly could cause an acci-
dent, resulting in serious personal injury or prop-
erty damage.
Replace worn, cracked, or damaged spring
brackets. Failure to do so could result in bracket
breakage, possibly leading to loss of vehicle con-
trol and resulting in personal injury or property
damage.
1.
Inspect the forward and rear spring brackets and
equalizer brackets for wear, cracks, and other
damage. If any of these conditions exist, replace
the damaged bracket(s). See
Group 32
of the
Century Class Trucks Workshop Manual
for in-
structions.
2.
Inspect the tandem-axle frame crossmember and
gussets for wear, cracks, and other damage. If
any of these conditions exist, replace the dam-
aged parts. See
Group 32
of the
Century Class
Trucks Workshop Manual
for instructions.
NOTICE
Failure to replace the suspension crossmember or
gussets if they are cracked, worn, or otherwise
damaged could result in damage to the vehicle
chassis.
3.
Without detaching the torque arms, attempt to
move (by hand) each radius-rod end up, down,
in, and out. If there is any movement, replace the
torque arm. If a torque arm needs to be re-
placed, see
Group 32
of the
Century Class
Trucks Workshop Manual
for instructions.
4.
Inspect the weld seams between the torque arm
tube and the shorter bushing tubes. If there are
cracks, replace the torque arm. Do not weld the
torque arm for any reason.
5.
Inspect the rubber bushing ends. See
. Re-
place the torque arm for any of the following rea-
sons:
•
if there are gaps between the rubber bush-
ing and the pin or outer steel sleeve;
•
if either bushing end contacts a torque arm
pin mounting bolt;
•
if there are cracks in the bushing;
•
if part of the rubber bushing extends be-
yond the outer circumference of the outer
bushing sleeve.
6.
Block up the frame enough to take chassis
weight off the springs. Attempt to move the
equalizer up and down, using a pry bar between
the top of the equalizer and top of the equalizer
bracket; apply hand pressure only. See
. If
movement at the center of the equalizer exceeds
1/8 inch (3 mm), replace the equalizer bushings.
See
Group 32
of the
Century Class Trucks
Workshop Manual
for instructions.
7.
With the vehicle unloaded, attempt to move the
equalizer side to side, using a pry bar between
the equalizer and frame rail. Apply hand pressure
only. See
. If clearance between the equal-
izer assembly and any frame component or fas-
tener is less than 1/8 inch (3 mm), replace the
f320465
11/27/95
Fig. 2, Direct-Acting Shock Absorber (front suspension
shown)
Suspension
32
Century Class Trucks Maintenance Manual, January 2016
32/2
Summary of Contents for Argosy COE 2011
Page 1: ...Maintenance Manual CENTURY CLASS STI 341 1 A24 00691 000...
Page 3: ......
Page 5: ......
Page 11: ......
Page 33: ......
Page 35: ......
Page 41: ......
Page 43: ......
Page 45: ......
Page 47: ......
Page 49: ......
Page 53: ......
Page 63: ......
Page 67: ......
Page 69: ......
Page 77: ......
Page 79: ......
Page 91: ......
Page 103: ......
Page 111: ......
Page 113: ......
Page 123: ......
Page 125: ......
Page 129: ......
Page 135: ......
Page 149: ......
Page 159: ......
Page 161: ......
Page 165: ......
Page 167: ......
Page 175: ......
Page 179: ......
Page 183: ......
Page 191: ......
Page 193: ......