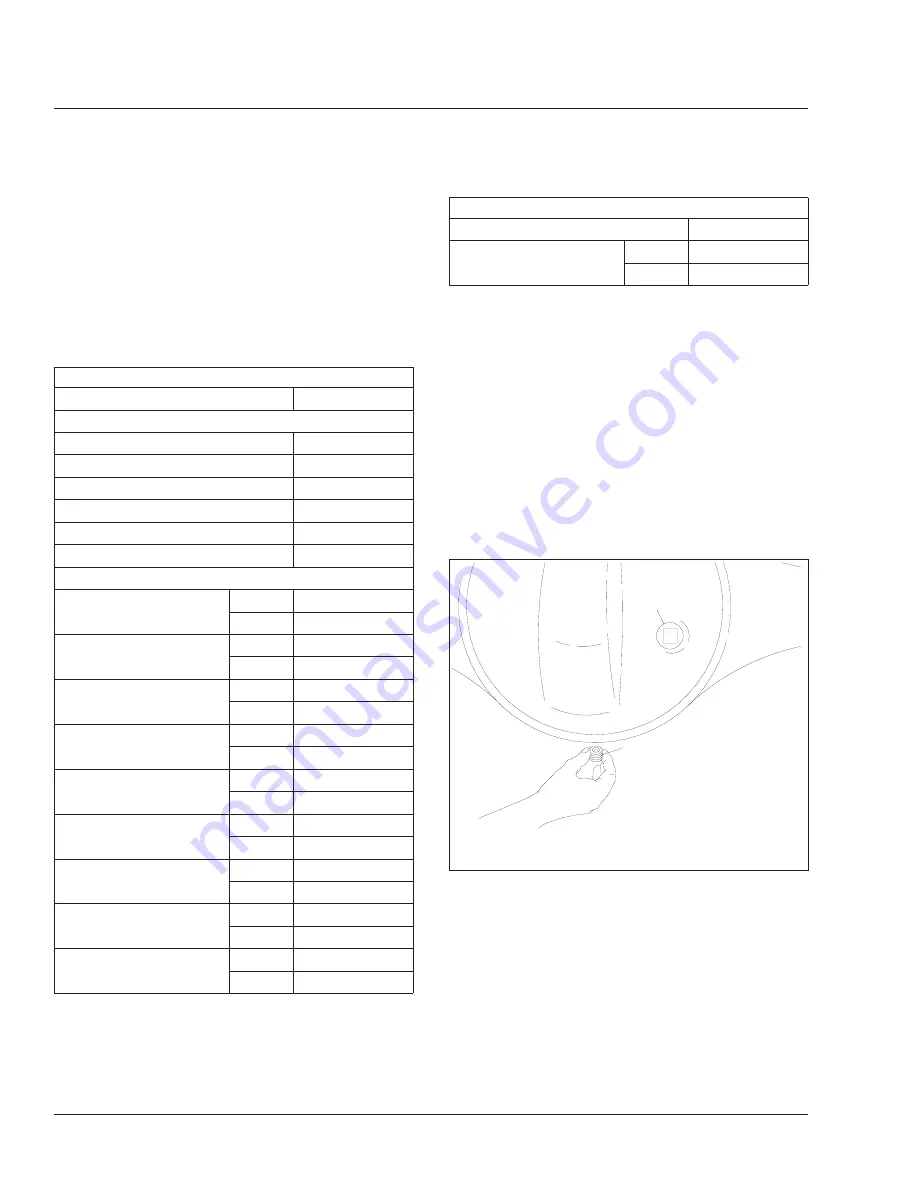
7.
Whenever the interaxle differential housing has
been drained, add an additional 2 pints (0.9 L) of
the recommended lubricant directly into the inter-
axle differential housing.
8.
Remove the chocks, then drive the vehicle, un-
loaded, for 1 or 2 miles (2 or 3 km) at speeds
not to exceed 25 mph (40 km/h), to thoroughly
circulate lubricant throughout the carrier and
housing assemblies.
Meritor Drive Axle Lubricant Capacities
Axle Model
Capacity
*
: pt (L)
Single-Drive, Single Reduction
RS–21–160
39.5 (18.7)
RS–23–160
39.5 (18.7)
RS–23–161
37.2 (17.6)
RS–23–185
47.3 (22.4)
RS–23-186
47.3 (22.4)
RS–26-185
46.0 (22.0)
Tandem-Drive, Single Reduction
MT–40–143MA–N
Forward
30.2 (14.3)
Rear
25.8 (12.2)
RT–40–145, RT–40–145A,
RT–40–145P
Forward
30.2 (14.3)
Rear
25.8 (12.2)
RT–40–160
Forward
39.1 (18.5)
Rear
39.4 (16.3)
RT–44–145, RT–44–145P
Forward
29.3 (13.9)
Rear
25.1 (11.9)
RT–46–160, RT–46–160P
Forward
39.1 (18.5)
Rear
34.4 (16.3)
RT–46–164EH/P
Forward
38.0 (18.0)
Rear
33.0 (15.0)
RT–50–160
Forward
38.0 (18.0)
Rear
33.0 (15.0)
RT–52–185
Forward
56.1 (26.5)
Rear
36.1 (17.1)
RT–58–185
Forward
56.1 (26.5)
Rear
36.1 (17.1)
Meritor Drive Axle Lubricant Capacities
Axle Model
Capacity
*
: pt (L)
RT–70–380
Forward
54.4 (25.7)
Rear
53.1 (25.1)
*
Quantities listed are approximate. Fill axle until lubricant is level with bot-
tom of fill hole with vehicle on level ground.
Table 4, Meritor Drive Axle Lubricant Capacities
Dana® Spicer®
IMPORTANT: The use of friction modifiers is not
approved in Dana drive axles.
1.
Park the vehicle on level ground, set the parking
brakes, and chock the tires.
2.
Clean the fill plug and the area around it. In the
axle housing rear cover, remove the plug from
the oil fill hole (or standpipe, if installed in the oil
fill hole); see
3.
Place a drain pan under the rear axle drain plug;
see
. Drain the oil at normal operating tem-
perature, 150°F to 200°F (65°C to 93°C). At this
temperature, the oil will run more freely and en-
sure that the axle is flushed.
NOTE: Some tandem-drive axles are equipped
with a cylindrical magnetic strainer, located
below the lube pump on the front of the power
f350018a
05/27/93
1
2
1.
Oil Fill Plug
2.
Oil Drain Plug
Fig. 4, Dana Spicer Axle Housing Drain and Fill Plugs
Rear Axle
35
122SD and Coronado 132 Maintenance Manual, February 2016
35/4