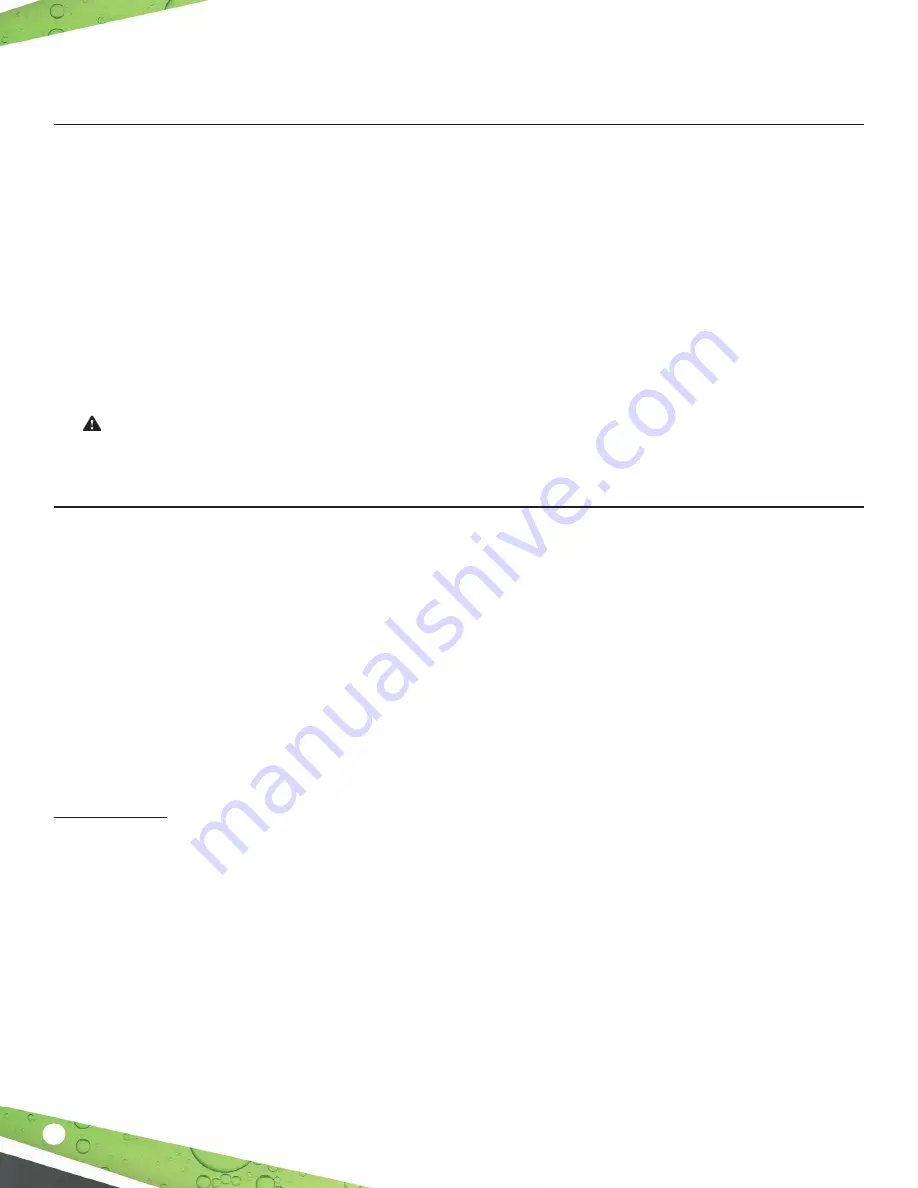
6
STP-SCIIIC:
For 240 Volt hook signal; 380-415 Volt, 3 phase, 50Hz ¾ , 1 ½ , 3 and 5 Horsepower pumps.
Installation Instructions
1.
Install STP per applicable Installation and Owner’s Manual.
2. Remove cover of STP-SCIIIC and mount base to wall or other surface.
3.
Connect input power of 380-415V for STP-SCIIIC to L1, L2, L3 and Ground wire to terminals.
(See Figure 2.) On High Capacity Pumps (3HP & 5HP) there is no need to connect the Thermal Overload
wires (blue) coming from the pump as long as an STP-SCIIIC is being used and is calibrated properly.
4.
Connect dispenser hook signal or other equipment to terminals, 240V supply and return for STP-SCIIIC.
5.
Using an ohmmeter, confirm M1, M2 & M3 have continuity to pump. Also, make sure M1 to Ground, M2 to
Ground, and M3 to Ground are not shorted.
6.
Connect motor leads to M1, M2 and M3, and Ground wire to terminals.
7.
Set SW1 Poles 4 and 5 for the motor Horsepower rating (see Table 3).
8. For Stand Alone installation, set (SW1) poles 1-3 per Table 2 (Factory Set). If installed as Master-Slave and/
or Alternating Circuit go to “Master-Slave/Alternating Circuit” section.
9.
Attach cover of controller to base. Then go to “Calibration” section to complete installation.
WARNING
Always replace the cover of the STP-SCIIIC before applying power. Failure to do so could
result in severe injury or death.
Calibration
Note:
It is recommended to calibrate all manifolded Master and Slave controllers at the same time.
1.
Turn on power supply to the STP-SCIIIC. The green light indicator will come on steady, the red light
indicator will flash 8 times and an audible alarm will sound, thus indicating the controller is Uncalibrated.
Note:
The audible alarm will sound each time the red light indicator flashes. During the calibration process,
do not silence the alarm. Once the calibration process has been completed, an alarm can be silenced when an
abnormal condition is present by briefly depressing the push button. See “Troubleshooting Guide” for details.
2. Press and hold the push button on the bottom of the box until all three light indicators blink alternately.
This will take approximately 10 seconds. At this point the push-button should be released.
3.
The handle on the dispenser should then be lifted to turn the pump on (for more than 16 seconds). After
16 seconds the controller will take a “snapshot” of the voltage, current and power. The three lights will
quit alternating and only the green light should remain flashing. This will indicate the calibration has been
completed and the dispenser handle can then be turned off. If the controller(s) will not calibrate, see the
“Troubleshooting Guide” section.
Calibration Tips
The “snapshot” values will be used as the nominal values. The calibration process will be aborted if not
completed within 10 minutes or if the push button is depressed during calibration. The calibration must be
done at zero flow. If an electronic line leak detector is being used, it is important that the STP-SCIIIC be in the
calibration mode (all three lights flashing alternately) before the dispenser handle is turned on. Otherwise, the
STP-SCIIIC will not turn on and the line leak detector will likely detect a fault. If the line leak detector shows a
fault, it will not provide a dispenser hook signal to the STP-SCIIIC and it will not be possible to calibrate the STP-
SCIIIC until the line leak detector is reset.
Note:
All STP-SCIIICs must be calibrated prior to operation.
Note:
All three indicator lights will flash alternately in calibration mode.
Note:
When calibrating system and dispensers that are blenders, both STP-SCIIICs must be calibrated
simultaneously by selecting the mid-grade at the dispenser.
Note:
The calibration data is retained in non-volatile memory (i.e. it is saved in the event of power loss to the
controller).