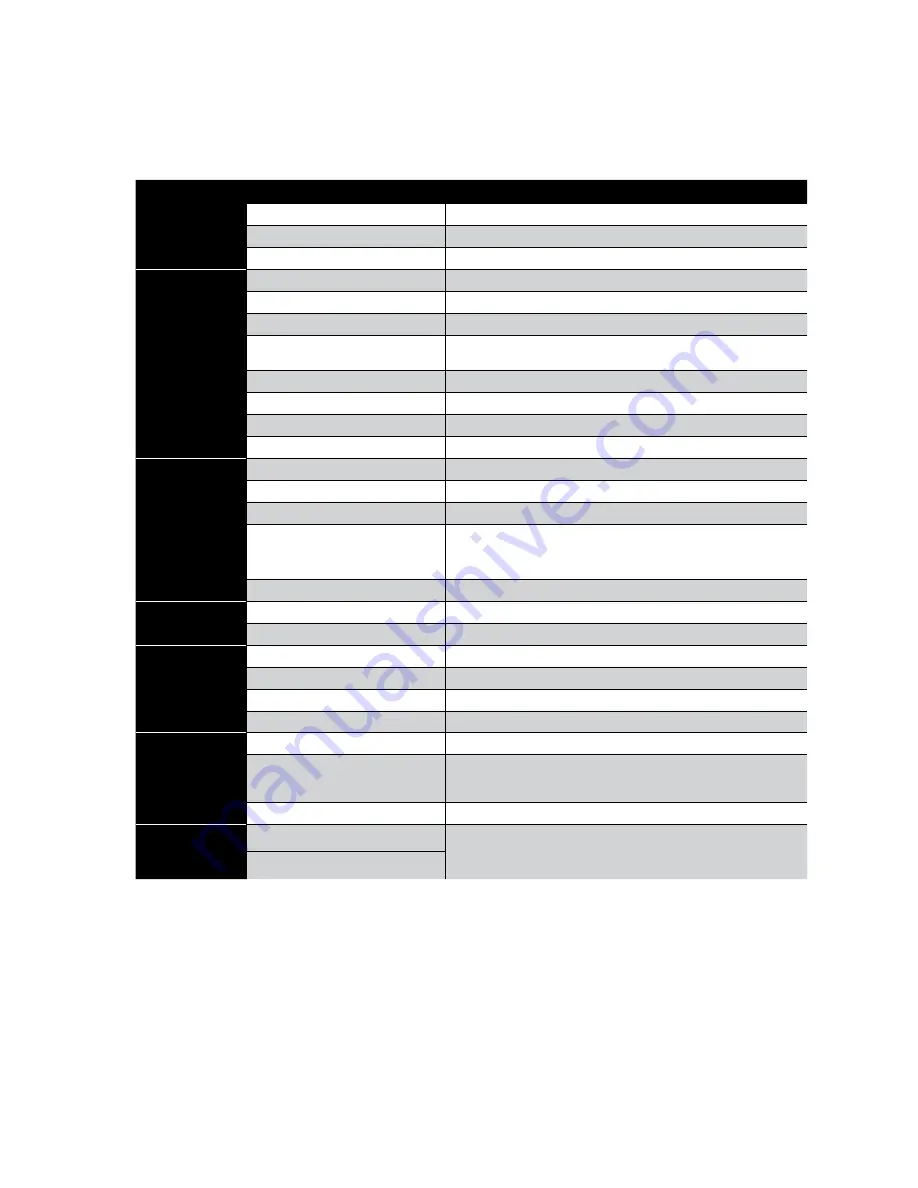
40
SubDrive/MonoDrive
Specifications - SubDrive2W
SubDrive2W
Model No.
NEMA 1 (indoor)
Not Available
NEMA 3R (indoor/outdoor)
Model 5870203223
NEMA 4 (outdoor)
Not Available
Input from
Power Source
Voltage
207-260 VAC
Phase In
Single-Phase
Frequency
60/50 Hz
Current (max)
14 Amps (RMS)
(For circuit breaker sizing)
Power Factor
0.7 (approximate)
Power (idle)
20 Watts
Power (max)
1900 Watts
Wire Gauge Size(s)
Consult Federal, State, and Local codes for branch circuits installations
Output to Motor
Voltage
Adjusts with Frequency
Phase Out
Single-Phase (2-wire)
Frequency Range
30-60 Hz
Current (max)
6 Amps (RMS) 1/2 hp, 0.37 kW system
8 Amps (RMS) 3/4 hp, 0.55 kW system
10.4 Amps (RMS) 1 hp, 0.75 kW system
Wire Gauge Size(s)
NEMA 3R #6 - #18 * ga.
Pressure
Setting
Factory preset
50 psi (3.4 bar)
Adjustment Range
25-80 psi (1.7 - 5.5 bar)
Operating
Conditions
(A)
Temperature (at 230 VAC input)
-13 °F to 125 °F (-25 °C to 50 °C)
Relative Humidity (NEMA 1)
Not Available
Relative Humidity (NEMA 3R)
10-95%, non-condensing
Relative Humidity (NEMA 4)
Not Available
Controller Size
(B)
(approximate)
NEMA 1 (indoor)
Not Available
NEMA 3R
12 1/4” x 16 1/2” x 9”
(31.1 x 41.9 x 22.9 cm)
15.0 lbs (6.80 kg)
NEMA 4 (outdoor)
Not Available
For Use With
(C)
Pump (60 Hz)
1/2 hp pump/motor with 244505 - series
3/4 hp pump/motor with 244507 - series [default]
1 hp pump/motor with 244508 - series
FE Motor Rating
Notes:
(A) Operating temperature is specified at full output power when installed as described in Controller Location Selection on pg. 22.
(B) Refer to pg. 43 for detailed Mounting Dimensions.
(C) If a pump other than the default rating is used, refer to pg. 13 for Drive Configuration.
* Refer to pg. 28 for detailed Circuit Breaker and Wire Sizing.
Summary of Contents for MonoDrive
Page 45: ...SubDrive MonoDrive 45 Notes ...
Page 46: ...46 SubDrive MonoDrive Notes ...