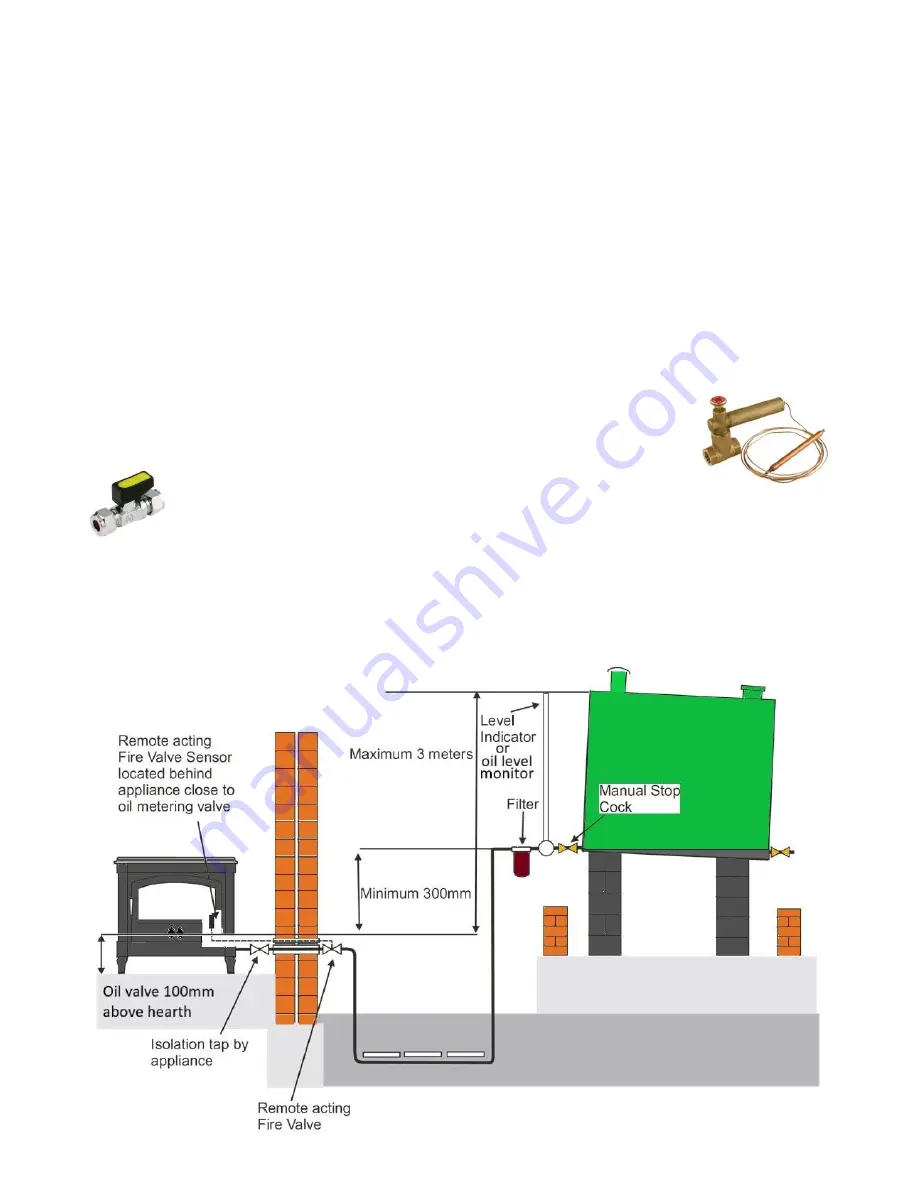
Fuel and Fuel Oil Storage
All the stoves are calibrated for commercial Class C2 kerosene to B.S. 2869: suitable for vaporising pot burners.
Type of Tank
We strongly advise not to fit a second-hand oil tank as contaminated fuel may do irreparable damage to the installation
and as it is impossible to determine whether or not an oil tank is free from contaminates by visual inspection.
A polyethylene tank, will never rot or rust, are maintenance free and it is possible to render them inconspicuous with
suitable permanent screening.
All tank and oil supply pipe installations should follow BS 5410: Part 1: 1997.
An isolating valve must be fitted directly to the tank outlet, allowing for the maintenance of the other components
in the pipeline.
A metal bowl oil filter mounted to allow adequate room for the removal of the sediment bowl and filter element
without difficulty should be fitted in the pipeline to the property. We recommend a replaceable cartridge filter with
a water separation bowl is installed.
Before the pipeline enters the building, a remote acting fire valve should be fitted which will cut
off automatically the oil supply in the unlikely event of a fire within the property.
A manual isolation valve should be positioned as close to the stove as possible to enable all supply to be
turned off for stove maintenance and if the appliance is to be out of service for more than a few weeks.
Where the stove is positioned higher than the fuel storage tank, an oil lift pump with integral reservoir will be required.
Where the stove is positioned to give a head to oil greater than 3.5 meters a constant level valve should be fitted.
Tiger loop systems are not suitable.