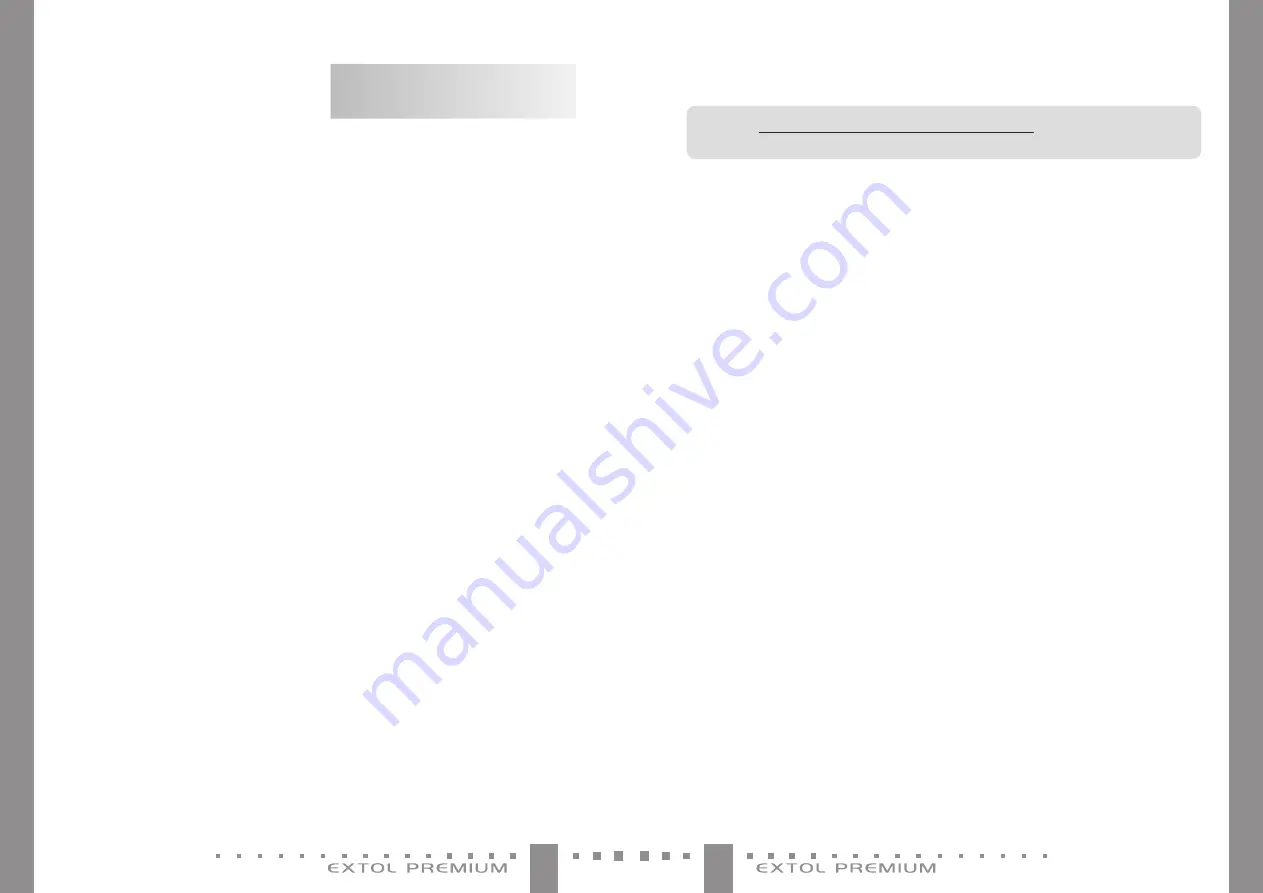
83
82
EN
EN
The formula for determining the flow rate of the com-
pressor for a given pressure is the following:
(Pressure in the pressure vessel
×
volume of the pressure vessel
×
60)
= Flow rate in L/min
Time for pressurisation to the given pressure in seconds
Example:
The time for pressurising the compressor‘s pressure
vessel with a volume of 24 litres to a pressure of 3 bar is
33 seconds.
The flow rate of the compressor for this pressure is thus
calculated from the aforementioned formula in the
following manner:
(3 bar × 24 litres × 60)/33 seconds = 131 L/min.
The flow rate of the compressor at a pressure of 3 bar is
131 L/min.
If the time for pressurising the pressure vessel of the
same compressor to a pressure of 8 bar is 1 minute 55
seconds (115 seconds), the above formula can be used to
calculate that the flow rate at a pressure of 8 bar is:
(8 bar × 24 litres × 60) / 115 seconds = 100 L/min.
From the above-described it is evident that the
flow rate (performance) of the compressor greatly
depends on the operating pressure, which applies
to all compressors without exception, as it is the
result of physical laws, where growing air pressure
in the pressure vessel leads to greater compression
of air pushed out of the pneumatic cylinder into the
pressure vessel and thereby also its volume. With
growing pressure in the pressure vessel, therefore,
the volume of the air supplied by the pneumatic
cylinder to the pressure vessel decreases due to the
effect of greater compression.
b) The air hose must have an inner diameter of at least
8 mm, otherwise it will not provide sufficient air
supply to the sander, thus preventing it from achie-
ving its maximum performance. Likewise, the air hose
should preferably be the unwindable type, as a spiral
hose reduces air flow through its greater resistance.
The hose should be as short as possible with respect
to feasible options. The longer the hose, the greater
the pressure loss at the hose outlet, which may also
reduce the performance of the sander. To demonstra-
te, we‘ll provide an example available from literature,
where if the inner diameter of an air hose is 10 mm,
then at a hose length of 5 m the inflow pressure of 6.0
bar is reduced by 1.7 bar at the outlet, and at a hose
length of 15 m it is reduced by 2.2 bar. The pressure
loss at the hose outlet resulting from the length of the
hose must be compensated for by a greater pressure
at the hose inlet and precisely set using a pressure
regulator at the inlet to the pneumatic tool to prevent
exceeding the maximum operating pressure.
In the event that a long hose is used, an impact wave
may result when the pneumatic tool is started.
•
ATTENTION
y
In order to achieve the require task (performance) of
the pneumatic tool, it is always necessary to take into
consideration the individual parts of the entire pneu-
matic system, i.e. sufficient flow rate of the compressor,
its type and the necessary inner diameter of the conne-
cted air hose - sufficiently powerful tools. If, for exam-
ple, the air hose has an inner diameter of, for example
6 mm and the compressor is sufficiently powerful, it
will not be possible for such a system to provide the
sufficient power for the pneumatic tool, because by its
limited inner diameter, the hose will limit the necessary
air supply to pneumatic tools, e.g. air impact wrench,
which have a large air consumption.
y
Pressurised air has different dynamic properties and
behaviour than hydraulic fluid, e.g. transmission of
power and, therefore, in the case when a system based
on hydraulic fluid works for a certain process, the use of
pressurised air of the same pressure may not necessa-
rily be sufficient, and it is necessary to verify the given
process by means of a practical test.
III. Recommended
accessories
AIR HOSE
y
For maximum performance of the sander, an air hose
with an inner diameter of at least 8 mm must be used;
further information about the hose is available in
chapter Technical specifications.
ADDITIONAL INFORMATION TO THE
AFOREMENTIONED
a) The compressor must have a sufficient flow rate
to cover the air consumption of the sander at the
max. operating pressure of 6.3 bar. In the event that
the flow rate is insufficient, the sander will exhibit
a lower speed/power. In the case of sufficiently long
breaks, the insufficient flow rate of a compressor can
be compensated for during shorter work periods with
pneumatic tools by a larger pressure vessel on the
compressor, which serves as an air storage reservoir.
The flow rate of the compressor is significantly
dependent on pressure. The higher the operating
pressure of the compressor, the greater is the loss
also of the flow rate. Normally, due to commercial
reasons only the flow rate is specified for a certain
compressor, omitting the operating pressure, because
in an attempt to achieve better sales, commercially it
is more important to provide the higher values of the
compressor‘s flow rate despite the fact that this flow
rate may correspond to an operating pressure of only
2-3 bar. A compressor has the highest flow rate value
at low operating pressure values and conversely the
lowest with the highest operating pressure.
•
ATTENTION
The value that is most predicative, i.e. most accura-
tely describes the performance of the compressor, is
the flow rate value at an operating pressure of the
compressor of 6 to 8 bar because pneumatic tools,
e.g. an air impact wrench, to achieve high performan-
ce (torque), consumes a large amount of air at the
maximum permitted operating air pressure of 6.3 bar,
otherwise bolts will not be sufficiently tightened or
loosened.
There exists a simple method for quickly and easily
verifying the performance of a compressor and
for determining the flow rate levels at various
pressures, and to thereby compare compressors
of the same pressure vessel volumes from various
manufacturers and, thereby, determine which is
better at a corresponding price level.
COMPARISON OF COMPRESSOR
PERFORMANCE FROM VARIOUS
MANUFACTURERS
•
ATTENTION
y
It is always necessary to compare compressors with the
same pressure vessel volume and, likewise, to assume
that a two-piston compressor with the same pressure
vessel volume will be more powerful than a single-pis-
ton compressor.
The most predicative value for the performance of
a given compressor is gained by measuring the time it
takes to pressurise the compressor‘s pressure vessel to
a pressure of 8 bar with the air outflow shut off.
Measure the time that it takes to pressurise the
compressor‘s pressure vessel to a pressure of
8 bar with the air outflow shut off.
For this measurement, use a stopwatch, e.g. on
your mobile phone as it is necessary to also mea-
sure seconds.
y
The higher performance compressor is the one
able to pressurise the pressure vessel to a pressu-
re of 8 bar in the shortest time.
y
The pressurisation speed is not linearly correlated, and
depends on the pressure in the compressor‘s pressure
vessel, meaning that pressurising a pressure vessel
from 2 to 3 bar takes less time than to pressurise from
7 to 8 bar, because when the motor is pushing out the
piston it needs to act against a greater air pressure in
the pressure vessel and the time required to pressurise
the pressure vessel is thus indicative of the compres-
sor‘s performance.
Determining the flow rate of a compressor
Measure the time that it takes to pressurise the
compressor‘s pressure vessel from the atmospheric
pressure to a pressure of 3, 4, 5, 6, 7, 8 bar with the
air outflow shut off.
y
The flow rate of the compressor for the given opera-
ting pressure can easily be calculated from one of the
formulae provided below. For this calculation, it is nece-
ssary to know the volume of the compressor‘s pressure
vessel and the time in seconds that it took to pressurise
the pressure vessel to the monitored pressure.