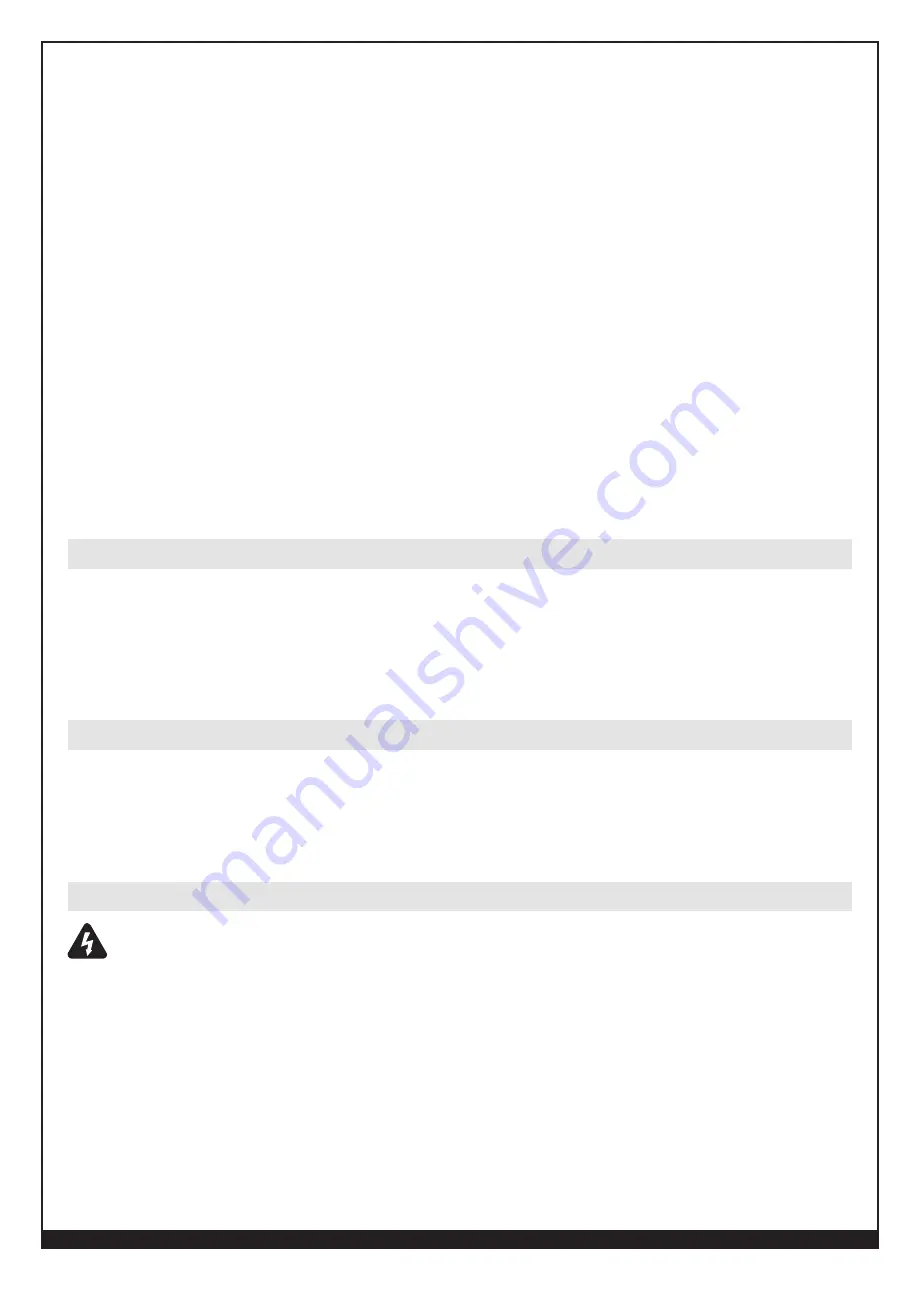
8
WWW.FORNEYIND.COM
• Keep cylinders away from areas where they may be subjected to physical damage or accidentally struck. Keep them
a safe distance from any source of flame, sparks, or heat.
• Do not weld or cut in an area where the air may contain flammable dust (such as grain dust), gas, or liquid vapors
(such as gasoline).
• Do not handle hot metal, such as the workpiece or electrode stubs, with bare hands.
• Wear leather gloves, heavy long sleeve shirt, cuff-less pants, high-topped shoes, helmet, and cap. As necessary, use
additional fire-resistant protective clothing to cover and protect the upper and lower body. Hot sparks or metal can
lodge in rolled up sleeves, pant cuffs, or pockets. Sleeves and collars should be kept buttoned and pockets eliminated
from the shirt front.
• Have fire extinguisher equipment handy for immediate use. A portable chemical fire extinguisher, type ABC, is
recommended.
• Wear ear plugs when welding overhead to prevent spatter or slag from falling into ear.
• Make sure welding area has a good, solid, safe floor, preferably concrete or masonry, not tiled, carpeted, or made of
any other flammable material.
• Protect flammable walls, ceilings, and floors with heat resistant covers or shields.
• Check welding area to make sure it is free of sparks, glowing metal or slag, and flames before leaving the welding
area.
• Wear garments free of oil or other flammable substances such as leather gloves, thick cotton shirts with no synthetic
materials, cuffless trousers, closed toed shoes. Keep long hair pulled back.
• Remove any combustibles such as lighters and matches before doing any welding.
• Follow requirements in OSHA and NFPA for hot work and have an extinguisher nearby.
High Frequency Radiation
• High Frequency (H.F) can interfere with radio navigation, safety services, computers and communication equipment.
• It is the user’s responsibility to have a qualified electrician promptly correct any interference problem resulting from the
installation. Electrician should regularly check and maintain installation.
• Stop using the equipment if notified by the FCC about interference.
• Keep H.F. source doors and panels tightly shut and keep spark gaps at correct setting.
Arc Welding
•
Computers and computer driven equipment can be harmed with electromagnetic energy.
•
Be sure all equipment is compatible with electromagnetic energy.
•
Keep welding cables short to reduce interference.
•
Follow manual to install and ground machine.
•
If interference continues, shield the work area or move the welding machine.
WARNING: ELECTRIC SHOCK CAN KILL!
To reduce the risk of death or serious injury from shock, read,
understand, and follow the safety instructions. In addition, make certain that anyone else who uses this welding
equipment, or who is a bystander in the welding area understands and follows these safety instructions as well.
IMPORTANT! TO REDUCE THE RISK OF DEATH, INJURY, OR PROPERTY DAMAGE, DO NOT
ATTEMPT OPERA TION
of this welding equipment until you have read and understand the following safety summary.
• Do not, in any manner, come into physi cal contact with any part of the welding current circuit. The welding current
circuit includes:
a. the workpiece or any conductive material in contact with it,
b. the ground clamp,
c. the electrode or welding wire,
d. any metal parts on the electrode holder, or TIG torch.
• Do not weld in a damp area or come in contact with a moist or wet surface.
• Do not attempt to weld if any part of clothing or body is wet.
• Do not allow the welding equipment to come in contact with water or moisture.
Electric Shock