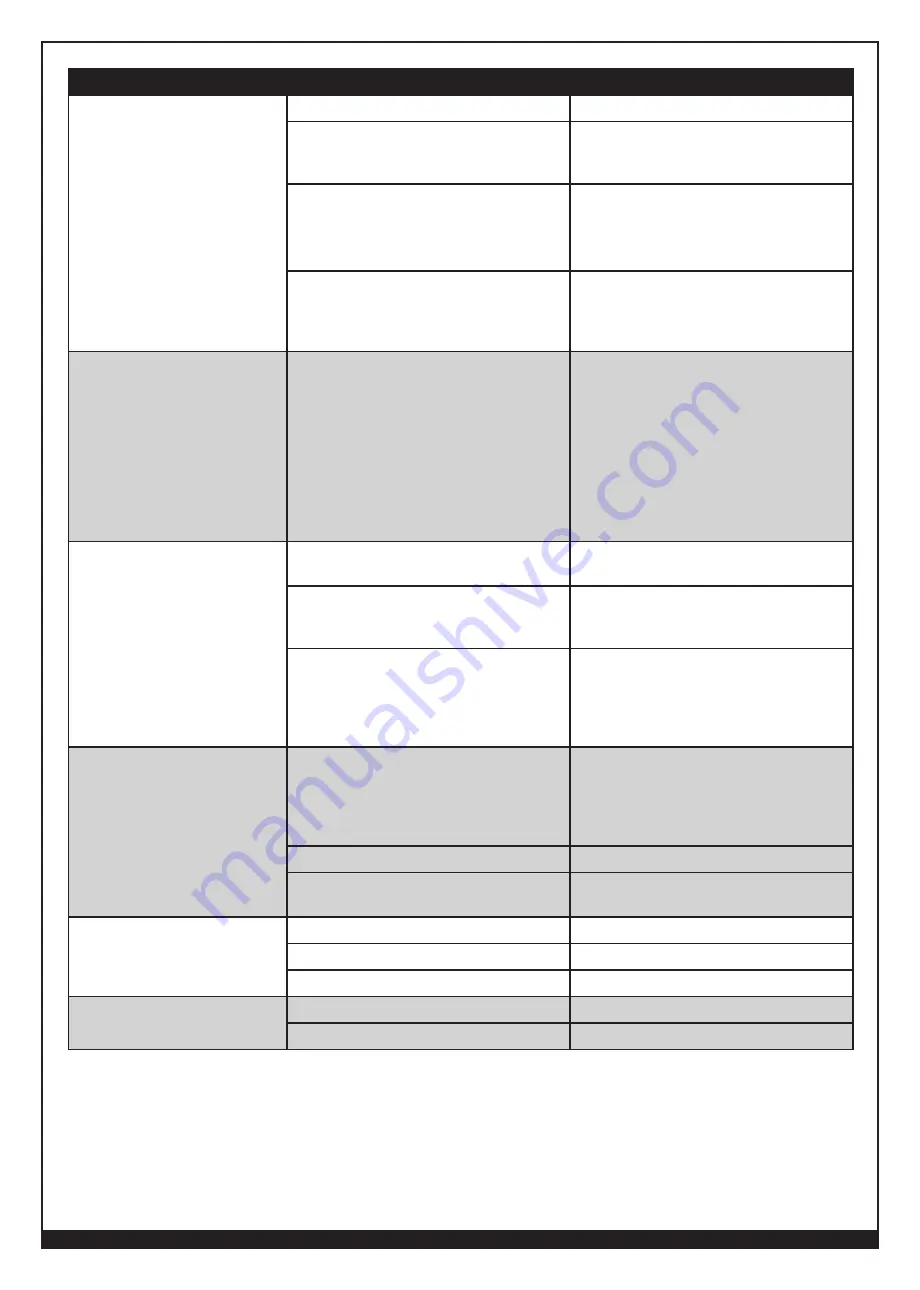
19
WWW.FORNEYIND.COM
PROBLEM
POSSIBLE CAUSE
POSSIBLE SOLUTION
Low output or non-penetrating
weld.
Weld parameters too low.
Adjust welding parameters
Too long or improper extension cord.
Use a proper extension cord (#12 AWG
wire or heavier, no longer than 25 ft.). See
“Extension Cords”, page 11.
Poor ground connection or torch/electrode
connection.
Reposition clamp and check cable to
clamp connection.
Check connection of ground cable, torch
or electrode holder
Input power too low.
Have a qualified electrician verify the
voltage at your outlet. If the voltage is
appropriate, verify that the circuit wiring is
sufficient for the circuit breaker size.
Ground clamp, ground cable, and/
or welding cable get hot.
Bad ground or loose ground connection.
Check connection of ground cable, torch or
electrode holder.
Check connection of the ground cable to the
ground clamp. Tighten cable connection to
ground clamp if needed.
Ensure the connection between the ground
clamp and workpiece is good and on clean,
bare (not painted or rusted) metal.
Make sure cable is not damaged.
Frequent circuit breaker trips.
Machine is drawing too much amperage
due to use of larger size electrode.
Use a smaller electrode.
Machine is not the only piece of electrical
equipment on the circuit.
Make sure the welder is on a dedicated
circuit or is the only thing plugged into a
circuit.
Circuit breaker is incorrect/insufficient for
use with this machine.
Verify that the circuit breaker for the circuit
is a 20A time-delay (slow-blow) breaker
for 120V and a 50A for 230V. If it is not,
have a qualified electrician install the proper
breakers.
Poor quality welds.
Insufficient gas at weld area.
Check that the gas is not being blown
away by drafts and, if so, move to a more
sheltered weld area. If not, check gas
cylinder contents, gauge, regulator setting,
and operation of gas valve.
Rusty, painted, oily or greasy workpiece.
Ensure workpiece is clean and dry.
Poor ground connection or torch/electrode
connection.
Check ground clamp/workpiece connection
and all connections to the machine.
Difficult arc start.
Amperage is too low.
Increase amperage setting.
Make sure base metal is clean.
Properly clean base metal.
Make sure electrode is not damaged.
Replace electrode if needed.
Arc is wandering (TIG).
Tungsten is too large.
Use a smaller tungsten.
Gas flow is too high.
Reduce gas flow.