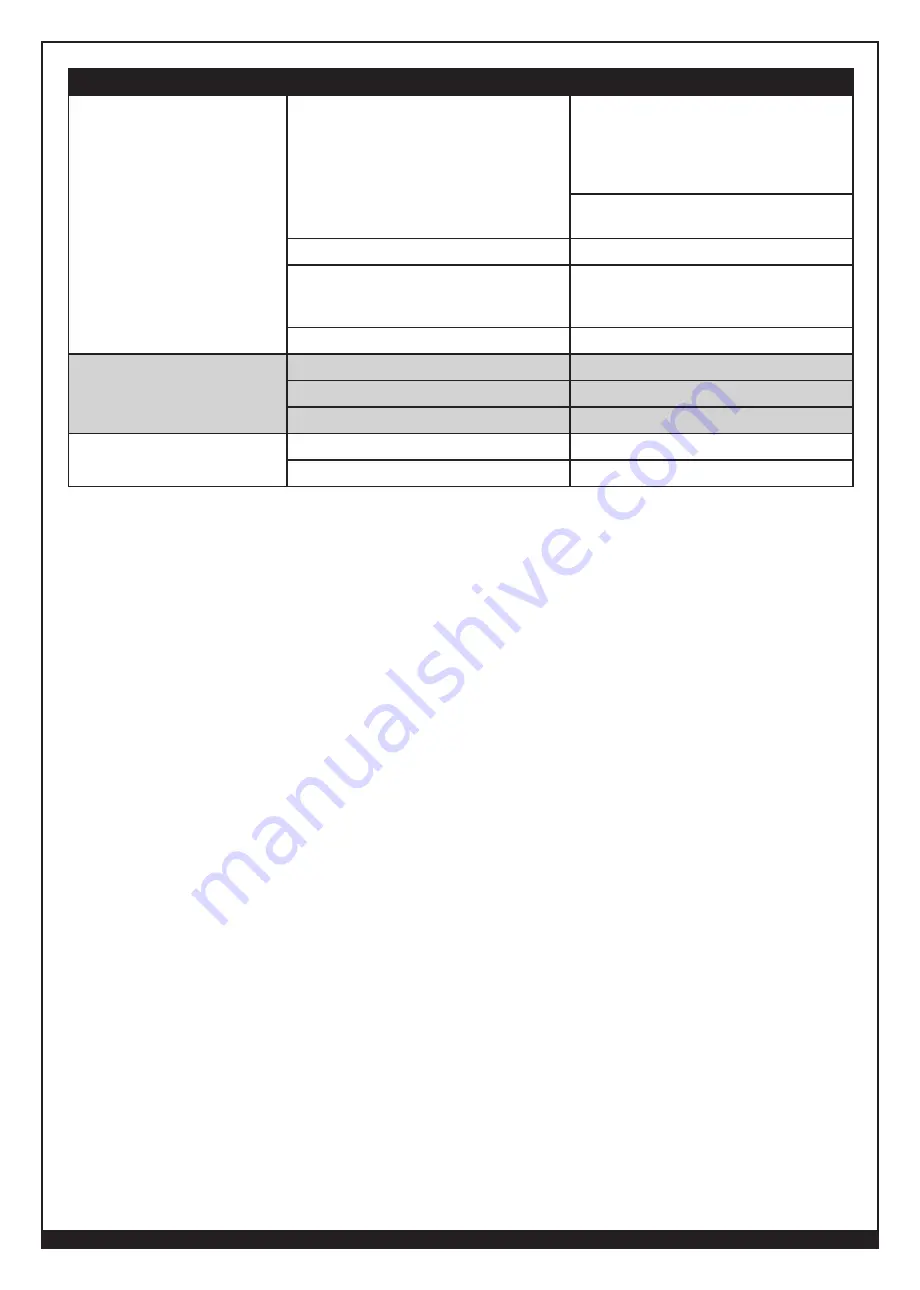
20
WWW.FORNEYIND.COM
PROBLEM
POSSIBLE CAUSE
POSSIBLE SOLUTION
Poor quality welds.
Insufficient gas at weld area.
Check that the gas is not being blown
away by drafts and, if so, move to a more
sheltered weld area. If not, check gas
cylinder contents, gauge, regulator setting,
and operation of gas valve.
Make sure gas connections are tight and
there are no leaks
Rusty, painted, oily or greasy workpiece.
Ensure workpiece is clean and dry.
Poor ground connection or torch/electrode
connection.
Check ground clamp/workpiece
connection and all connections to the
machine.
Incorrect settings.
Check welding parameters and polarity.
Difficult arc start.
Amperage is too low.
Increase amperage setting.
Make sure base metal is clean.
Properly clean base metal.
Make sure electrode is not damaged.
Replace electrode if needed.
Arc is wandering (TIG).
Tungsten is too large.
Use a smaller tungsten.
Gas flow is too high.
Reduce gas flow.