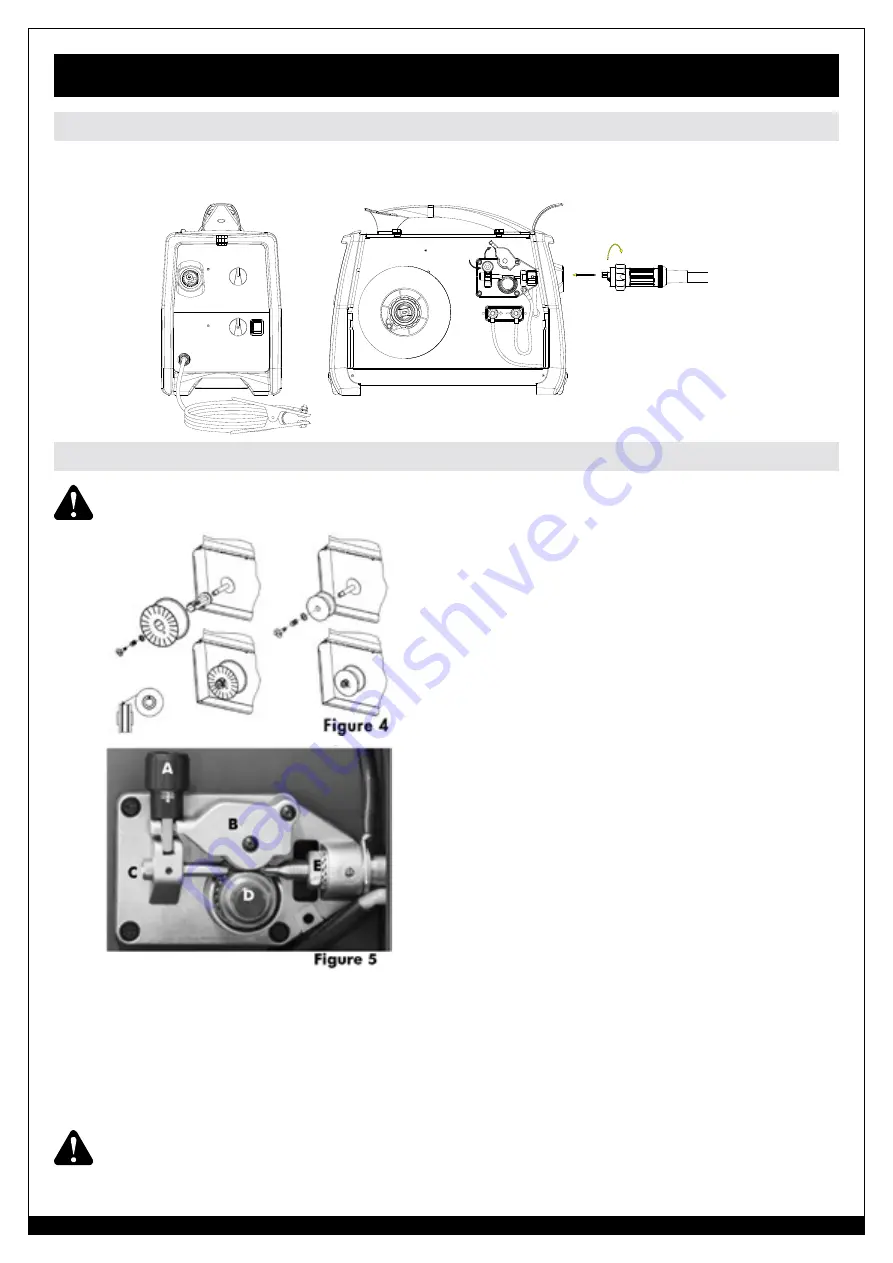
12
WWW.FORNEYIND.COM
• Connect the standard MIG torch to the threaded connector on the front of the welder, tighten
firmly by hand.
Ensure the gas and electrical supplies are disconnected. Before proceeding, remove the nozzle
and the contact tip from the torch.
• Open the side panel.
• Loosen the nut of the spool holder (brake drum)
and remove the spring and the external ring. (Fig.4)
• Remove the plastic protection from the spool (4) and
place the wire spool on on the spool holder.
• Mount the external ring, the spring and the
plastic lock nut again. These parts form the braking
system of the wire spool speed. NOTE: Do not
tighten the nut too much, excessive pressure strains
the wire feeding motor, while too little pressure does
not allow the immediate stop of the wire spool at the
end of the welding.
• Loosen and lower the plastic knob (A) (Fig.5). Open
the pressure arm (B) of the feeder
• Disconnect the wire from the edge of the wire spool
being careful to keep tension on the end of the wire.
Cut off a short section of the end of the wire to insure
a straight end. Insert the straight end into the wire inlet
guide (C) past the wire feed roll and into the wire liner.
Lower pressure arm (B) and lift pressure adjustment
knob (A) into place. Connect the input power cord and turn on the welder. Press the torch trigger
and observe the wire feeding into the torch liner. Adjust the pressure on the wire with knob (A)
to insure smooth feeding without slippage. Do not over tighten the pressure adjustment as it
may damage the motor. Close the welder side panel. Remove the nozzle and contact tip from
the welding torch. Straighten the torch cable to remove any coils or kinks. Squeeze and hold the
torch trigger until the wire appears at the end of the torch neck. Turn off the welder and install
the contact tip and nozzle.
WARNING:
Keep the torch straight. When feeding a new wire through the liner, make sure
the wire is cut cleanly (no burrs or angles) and that at least 2 cm from the end is straight (no
curves). Failure to follow these instructions could cause damage to the liner.
MIG, “GMAW” - Fluxcore wire, “FCAW” Welding
Torch Connection
Wire Loading
Summary of Contents for 190 MIG
Page 21: ...21 WWW FORNEYIND COM...
Page 23: ...23 WWW FORNEYIND COM...