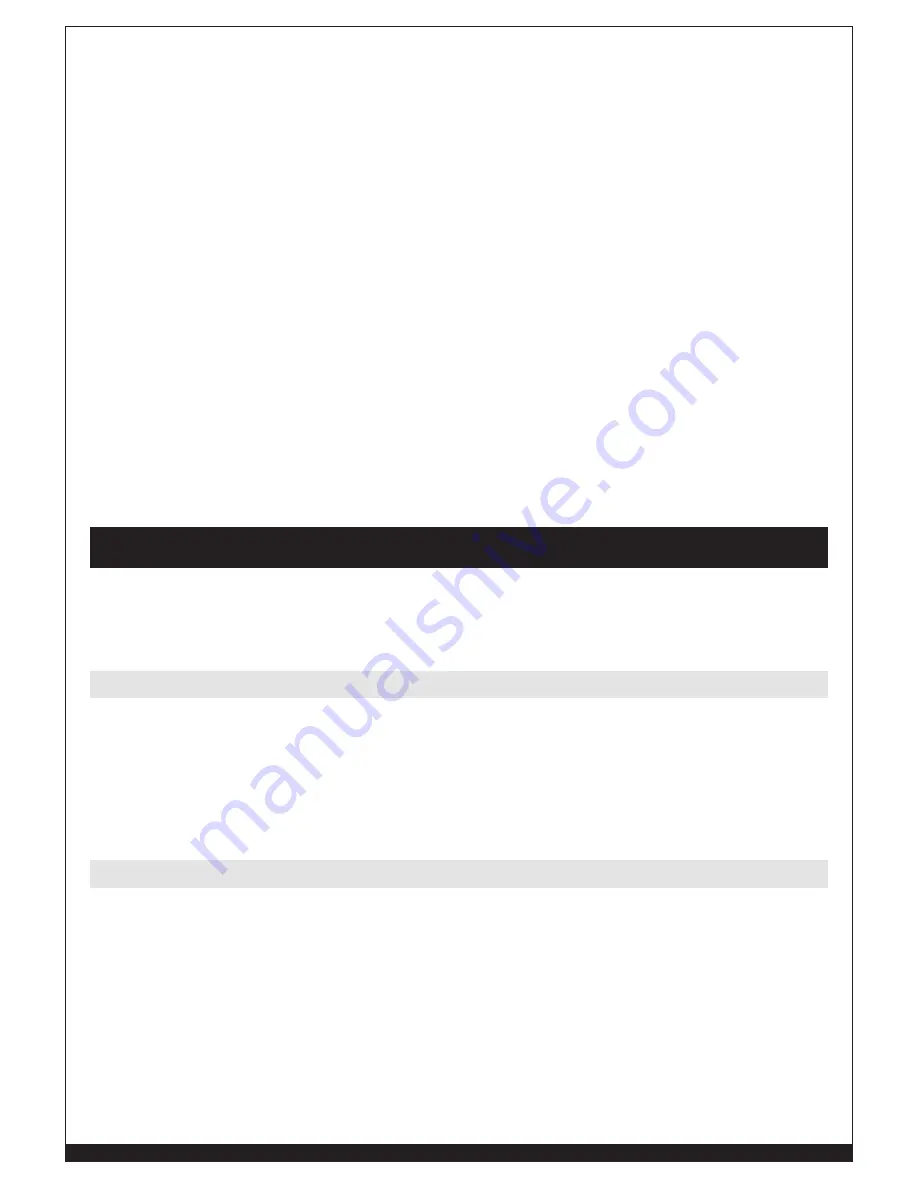
13
WWW.FORNEYIND.COM
tension roller is applying enough force on the wire to prevent it from slipping out of the drive
assembly.
8. Let go of the wire.
9. Plug the welder’s power cord into the AC power source. Adjust the settings on the front panel
per the setup chart on the inside panel door of the welding machine.
10. Pull the trigger on the welding gun to feed the wire through the gun assembly. When at least
an inch of wire sticks out past the end of the gun, release the trigger.
11. Install the supplied contact tip.
NOTE
: Due to inherent variances in flux-cored welding wire,
it may be necessary to use a welding tip one size larger than your flux-core wire if poor
feeding or jams occur.
12. Slide the contact tip over the wire (protruding from the end of the gun). Screw the contact tip
into the end of the gun and hand tighten securely.
13. Install the nozzle on the gun assembly.
14. Cut off the excess wire that extends past the end of the nozzle.
15. Set the wire drive tension.
a. Pull the trigger on the gun.
b. Turn the wire drive tension adjustment knob clockwise, increasing the drive tension until
the wire seems to feed smoothly without slipping.
NOTE
: If TOO MUCH tension is applied
you can crush the wire and create wire feeding problems. If TOO LITTLE tension is applied,
the wire will slip on the drive rolls and wire will not feed.
16. When the drive tension is set correctly, there should be no slippage between the wire and the
drive roller. But if an obstruction occurs along the wire feed path, the wire should then slip on
the drive roller.
Operation of this welder consists of selecting and adjusting operating controls for optimum voltage
(welding heat) and wire speed settings.
Your new flux core (FCAW) wire feed welder is designed for maintenance and sheet metal fabrication.
The welder consists of a single phase power transformer and a built-in control/feeder. This welder is
capable of welding with 0.030” (0.8 mm) and 0.035” (0.9 mm) self-shielding flux-core wire. The use
of 0.030” wire is recommended. Now you can weld sheet metal from 18 gauge up to 3/16 inch thick
with a single pass. You can weld 1/4 inch steel with beveling and multiple pass techniques.
Variations in input power, welding position, and wire will affect the weld characteristics. Use the voltage
settings and wire speed indicated as a starting point, then adjust for variables such as stick out, travel
speed, weld angle, cleanliness of metal, etc.
WARNING:
Read all instructions and warnings supplied with this welder before attempting to use or
service it. Also read all warnings and cautions on the welder.
Operation
Description
Suggested Settings
Summary of Contents for 125 FC
Page 25: ...25 WWW FORNEYIND COM Wiring Diagram...
Page 27: ...27 WWW FORNEYIND COM...