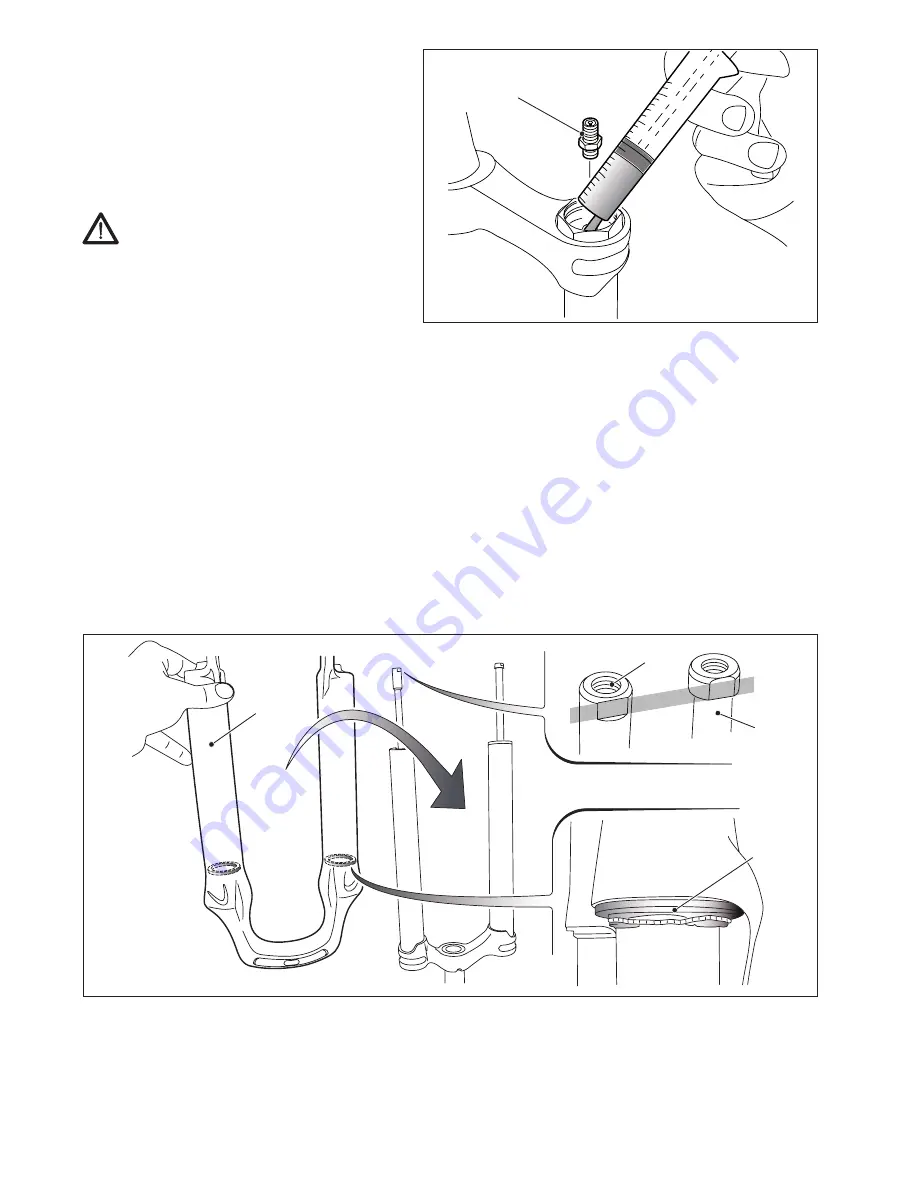
28
2
16
7
15
6
-
WARNING: Before assembling, make
sure the threads of the valve and cap
are clean and degreased.
- Apply threadlocker completely around the valve thread (
2
). Install the valve using a 10 mm
socket wrench, tightening to
5 Nm
. Use the high pressure pneumatic shock pump to inflate the
fork (as directed in paragraph 3.3) to the required pressure.
- Align the keyway on the two piston assemblies (
7-15
).
-Install the lower legs (
6
). Be extremely careful not to damage or bend the dust seals (
16
). Repla-
ce them if they are damaged in any way.
- Before placing the lower legs (
6
) against the piston assemblies(
7-15
), add
10cc
of
-Slide the lower leg (
6
) until it contacts the piston keyways (
7-15
).
Turn the fork upright and put
5cc
of oil
composed by 50% of Idemitsu OJ01 and
by 50% of Ballistol into the air cylinder
(
2
).
oil composed
by 50% of Idemitsu OJ01 and by 50% of
Ballistol
with a syringe, as shown in the figure below.
Summary of Contents for THIRTYFIVE QR15
Page 2: ......