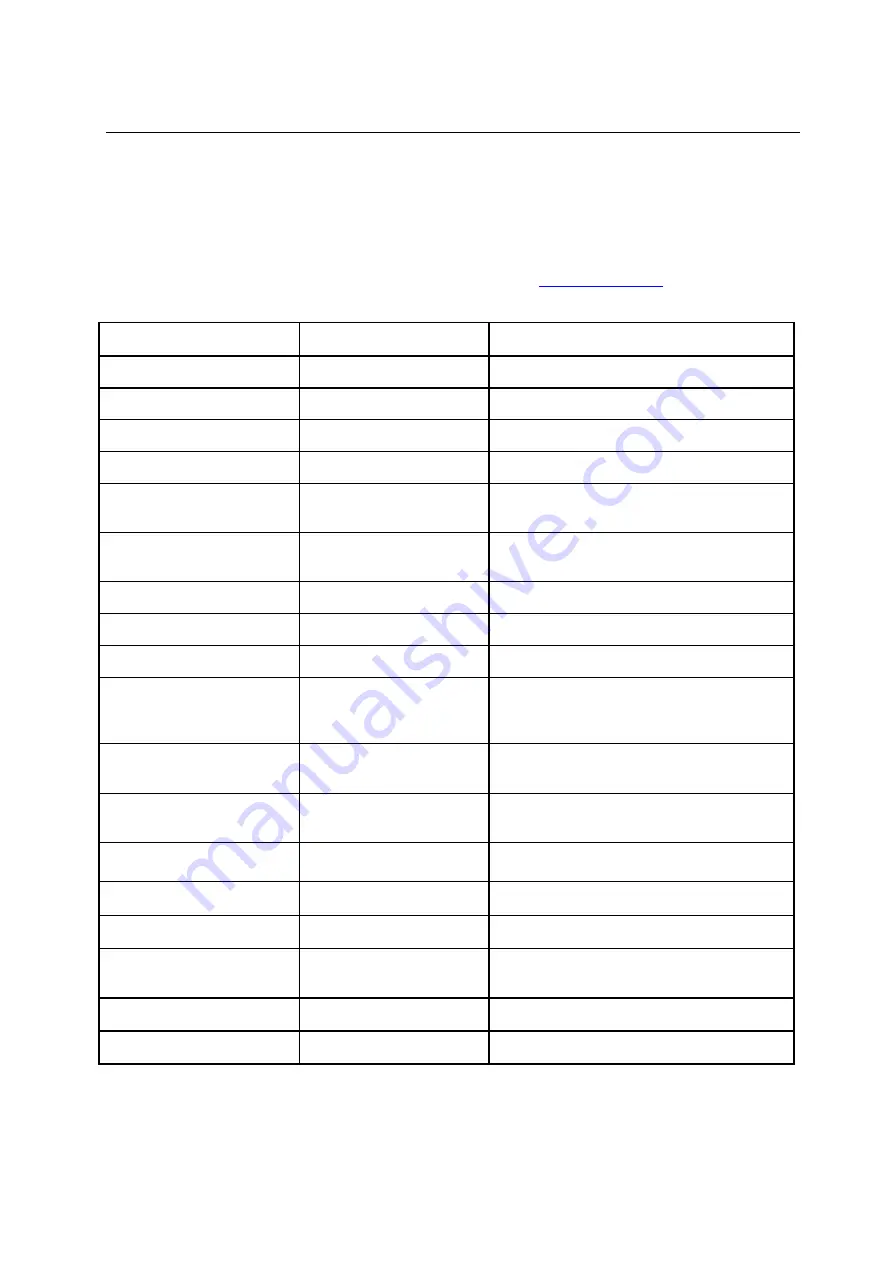
15
Forming Difficulties Formech FM660
The purpose of the following section is to help the user in overcoming some problems frequently
encountered in thermoforming. Please remember that the majority of thermoforming faults are caused
by incorrect machine setting or poor mould design.
This section is a guide only and cannot impart the practical experience and skill that any user will
eventually attain. You can find a more comprehensive trouble-shooting guide in the Formech training
Manual located in the support section of the Formech web page.
PROBLEM
CAUSE
REMEDY
Lack of definition
Material too cold
Increase heating time/temp.
Mould too cold
Warm mould
Insufficient vacuum
Adjust vacuum timings
Check vent holes on mould
Is mould restricting vacuum flow? Are
vacuum tracks in mould adequate?
Webbing (small pleats at
corners of mouldings)
Incorrect pre-stretch
height
Adjust pre-stretch flow and/or time. Check
panels for leaks
Incorrect heater zoning
Adjust problem zones
Material overheated
Reduce heating time
Vacuum speed too fast
Regulate to suit
Mould design/position
Increase tapers or radii. Use plug assist.
Move cavities further apart (Multiple
moulds)
Webbing
Excess material
Reduce material size or use 'dummy'
moulds
Shrinkage of moulding
(after removal from mould)
Product removed from
mould too quickly
Increase timings to allow longer mould
contact
Increase cooling time
Moulding too thin in areas
Incorrect heater zoning
Decrease temperature in problem zones
Too much pre-stretch
Decrease flow or timing
Cold spots
Check elements are working. Are there
any draughts?
Mould too cold
Warm mould
Material not consistent
Consult supplier