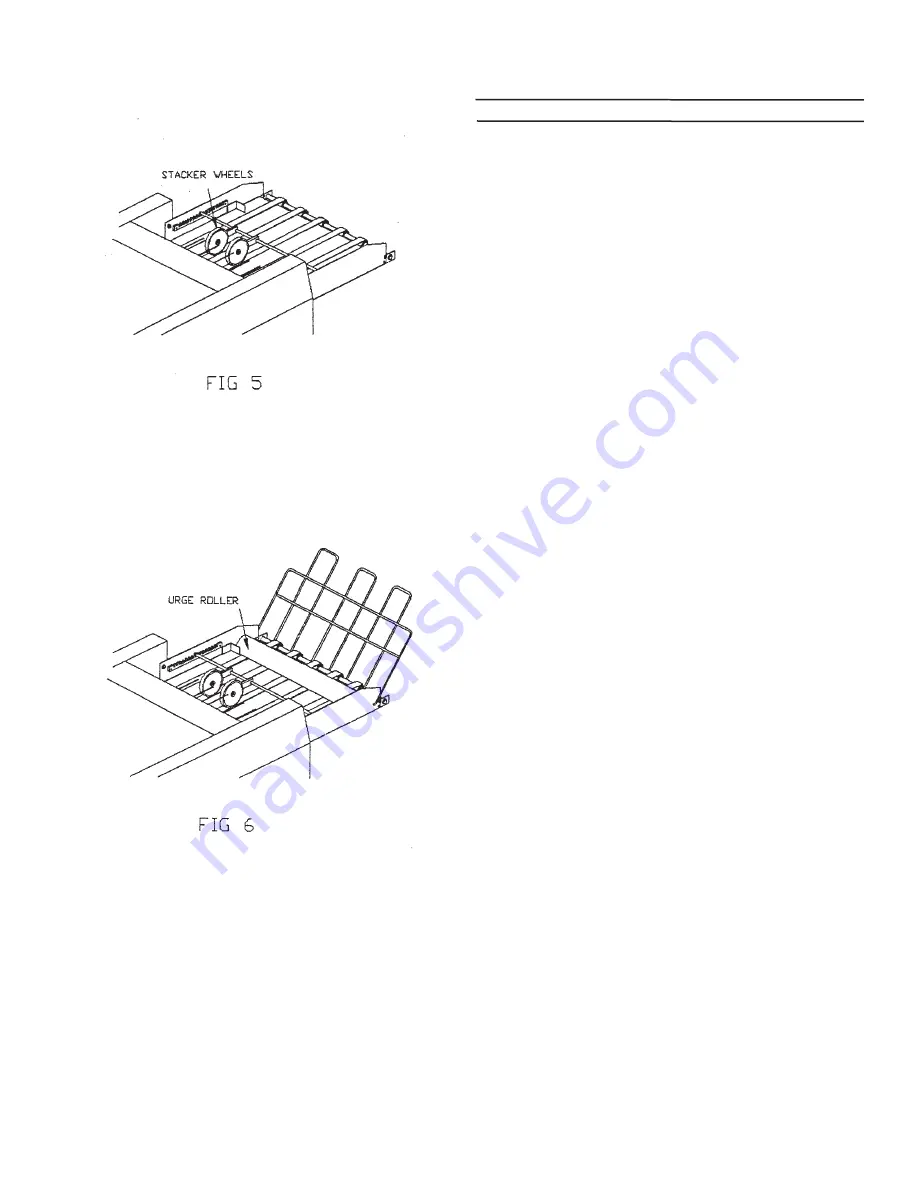
3
6. Place the stacker wheel assembly on the stacker wheel
adjustment rack. (Fig. 5)
7. Place urge roller on stacker tray so that it rests on the stacker
grill. (Fig.6)
ASSEMBLY INSTRUCTIONS FOR
INFEED BRUSH ASSEMBLY
FOR FD546-40 AND FD546-50 ONLY
Tools Required:
Medium Phillips Screwdriver
Parts Required:
1 - Infeed Brush Assembly
(Packed with Burster)
4 - 6-32 Phillips Pan Head Screws
(Packed in Accessory Box)
1. Unpack the infeed brush assembly and inspectfor damage.
2. Place the infeed brush assembly, with the bar on top to the
infeed end of the burster.
3. Align the holes in the infeed brush assembly with the threaded
holes in the burster side frames.
4. Insert all four screws without tightening them, once they are all
in, tighten them with a medium phillips screwdriver.