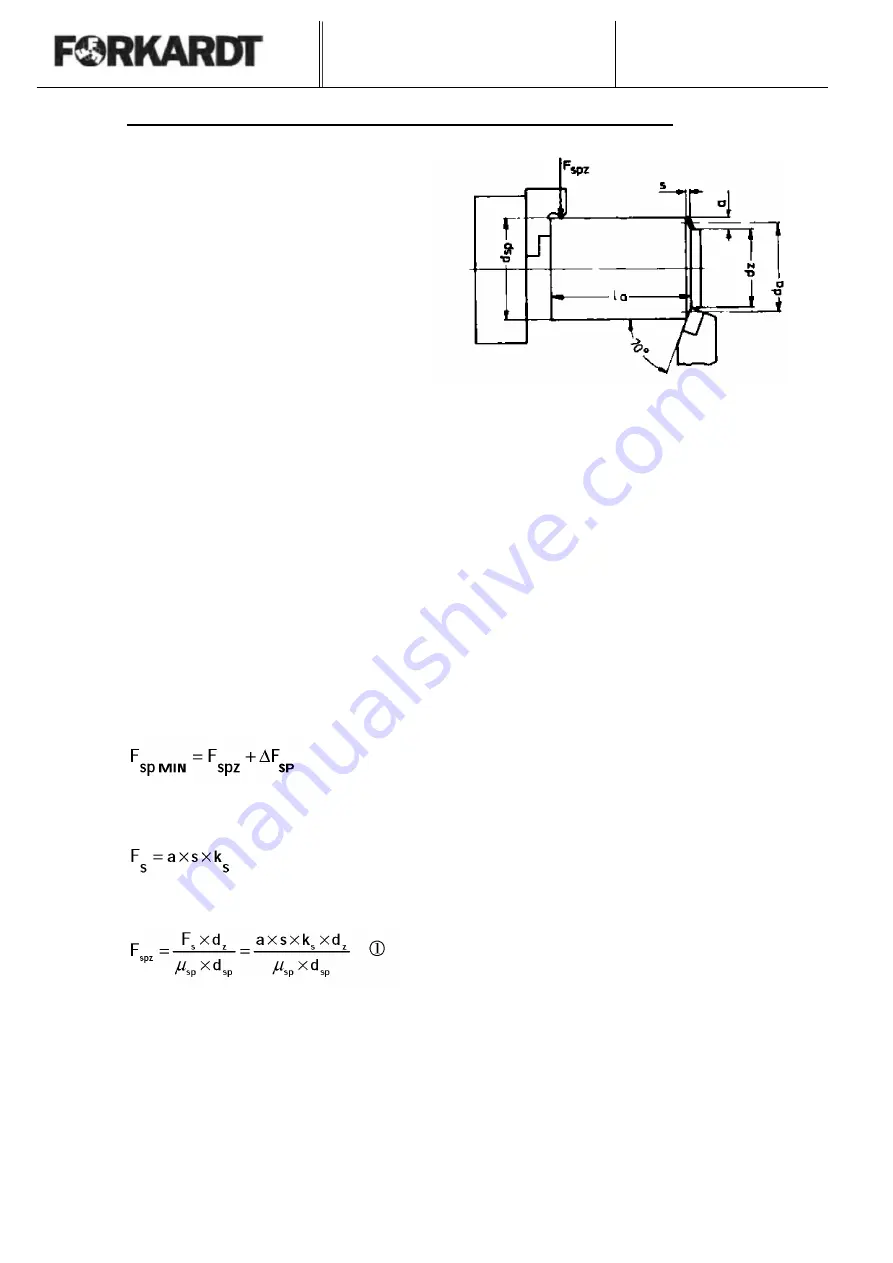
Table of contents
3QLCLM
Edition: 04/2014
26
Determination of the gripping force Fspz required for the machining process
The gripping force required for each
application has to be determined. If this
gripping force cannot be provided by the
chuck with the factors of safety given by the
guidelines of the German Association of
Engineers VDI 3106, then the permissible
spindle speed or the permissible chip cross-
section has to be determined.
An example:
A solid steel work piece (i.e. without bore) has to be machined. The gripping diameter dsp=60mm, the
turning diameter dz =60mm and the cut requires a tangential cutting force F
s
=1200daN at a spindle
speed of 2760 rpm.
Soft jaws turned to the gripping diameter are used to avoid damaging the work piece. This gives a
gripping coefficient of |i
sp
=0.1. A safety factor S
z
is allowed for the cutting data with S
z
=2.
T
he reduction in gripping force ΔFsp amounts to 2000daN.
This example shows:
When
taking into account the reduction in gripping force ΔF
sp
the minimum static gripping force
required is
= 2000 + 2000 = 4000daN. The main variable affecting the gripping force is the tangential cutting force
Fs, which can be determined from the chip cross-section and the specific cutting force.
The gripping force necessary for the machining operation is given by: