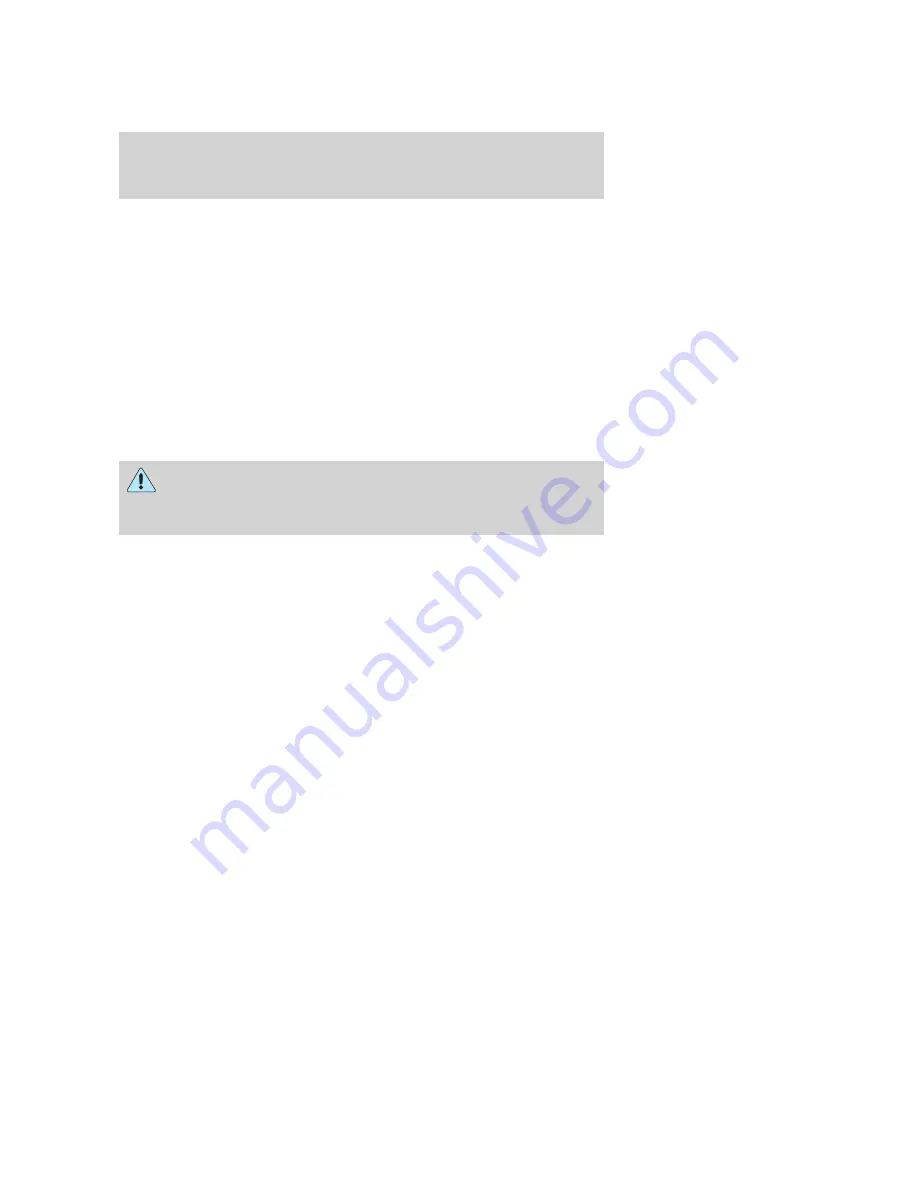
Air induction system
Once each year, perform a complete inspection of the air induction
system. In areas where road salt is used, the inspection consists of
disassembling the joints of each aluminum component and inspecting for
salt build-up and presence of chlorine that can cause aluminum particles
to flake off and enter the engine combustion chambers.
If evidence of corrosion is found (usually at the pipe connections), use a
wire brush to clean the inside of the pipes and inside the rubber hoses.
If the intake pipes are pitted at the joint ends, use RTV silicone to seal
the joints. Be certain that no excess material is on the inside of the pipes
that can be pulled into the engine. If the service condition of the pipes,
hoses or clamps is questionable, replace the defective part(s).
Be sure that prior to reassembly all dust and debris has been cleaned out
of the pipes and couplings with a clean, damp rag.
WARNING:
To reduce the risk of personal injury or death when
performing maintenance to any turbocharged engine with engine
air inlet piping disconnected, a turbocharger compressor air inlet
protective shield should be installed over the turbocharger air inlet.
CHASSIS-MOUNTED CHARGE AIR COOLER
The charge air cooler should be inspected daily. With the engine off,
visually inspect the charge air cooler core assembly for debris and
clogging of external fins. Prior to engine operation, remove any debris
blocking the core.
•
Turbocharger-to-charge air cooler
•
Charge air cooler-to-intake manifold pipe
•
Mounting bracket
•
Chassis-mounted charge air cooler core
Air intake piping inspection
•
Check for accumulation of salt deposits (where applicable). If present,
disassemble and clean the complete air intake piping system. If the
intake piping is pitted, use RTV silicone to seal joints against leakage.
•
Check for loose hoses and clamps.
•
Check for ruptured or collapsed hoses.
•
Check air filter housing for cracks.
2009 Low Cab Forward Truck
(lcf)
Supplement
USA
(fus)
Maintenance and Specifications
161