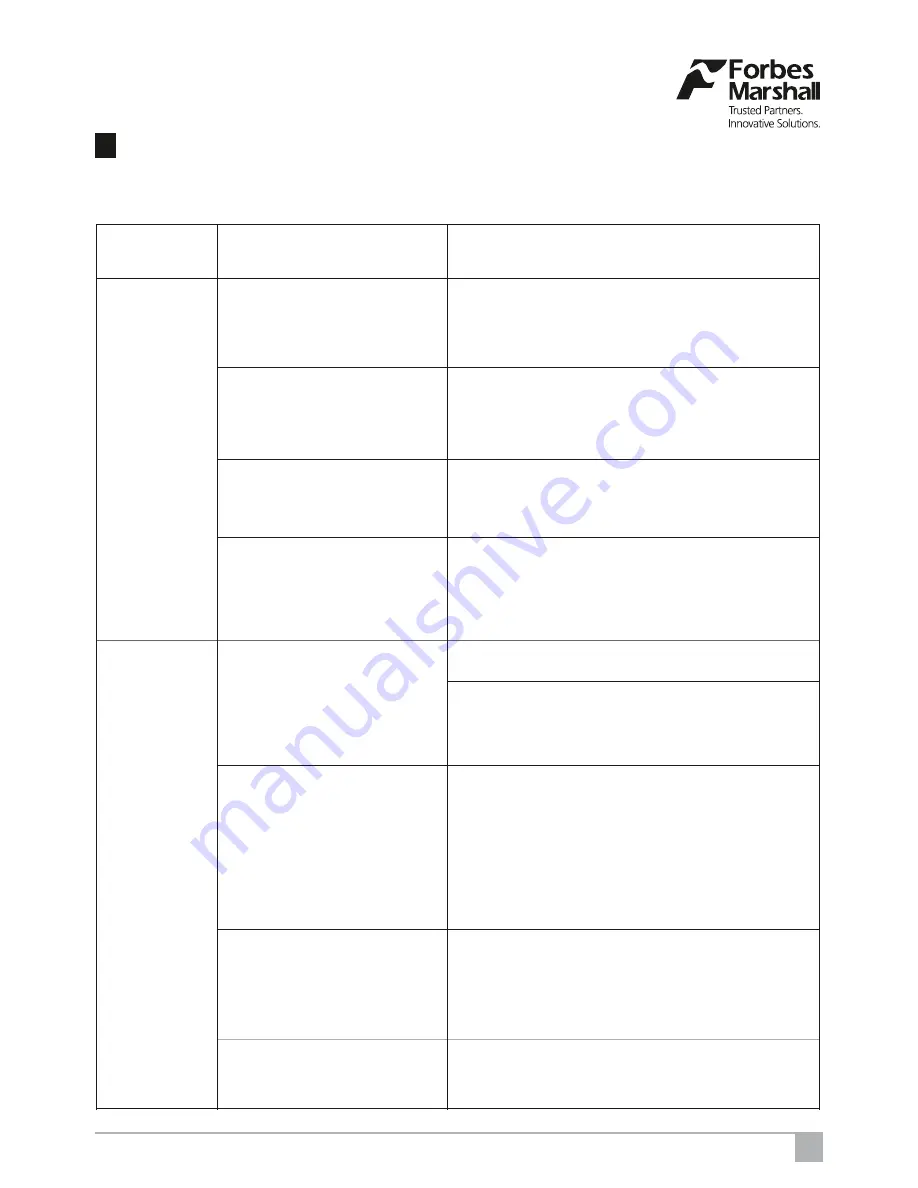
11
FMTD64
8.
Troubleshooting:
If the expected performance is unachievable after installation of the Forbes Marshall
thermodynamic trap, check the following points for appropriate corrective measures.
Failure Mode Possible Cause
Remedy
No
condensate is
discharged
(blocked).
Inlet drip leg or strainer
screen is clogged with rust or
scale.
Flush inline drip leg and clean strainer screen. If
strainer screen is rusted, replace with new
strainer screen.
Differential pressure is low.
Verify inlet and outlet pressure of the steam trap.
Minimum differential pressure required is 0.25
bar g
Air – Binding problem.
Loosen cap and tighten to suitable torque.
Steam trap body is hot but no
condensate discharge.
To release flash steam locked (trapped) inside the
steam trap, pour water on cap of the steam trap
to check it discharge condensate.
Steam
leakage.
Steam Leaking continuously.
Ensure bypass valve is fully closed.
Check installation i.e. cap to be on top and fluid
flow direction same as arrow on the steam trap
body
Foreign material or oil film on
disc or body seat.
Clean both disc and body seat, flatness on disc
and body seating faces can be improved by
lapping individually on flat surface or glass plate.
Note:
The total amount of metal from body seat
face removed should not exceed 0.25mm
(0.01”).
Disc stuck to the cap.
Give a light tap on top of the cap and check if
step (inner surface of the cap) is worn out. If step
is worn out replace with new steam trap.
Back pressure exceeds
allowable value.
Outlet pressure of the steam trap should not
exceed 80% of the inlet pressure.