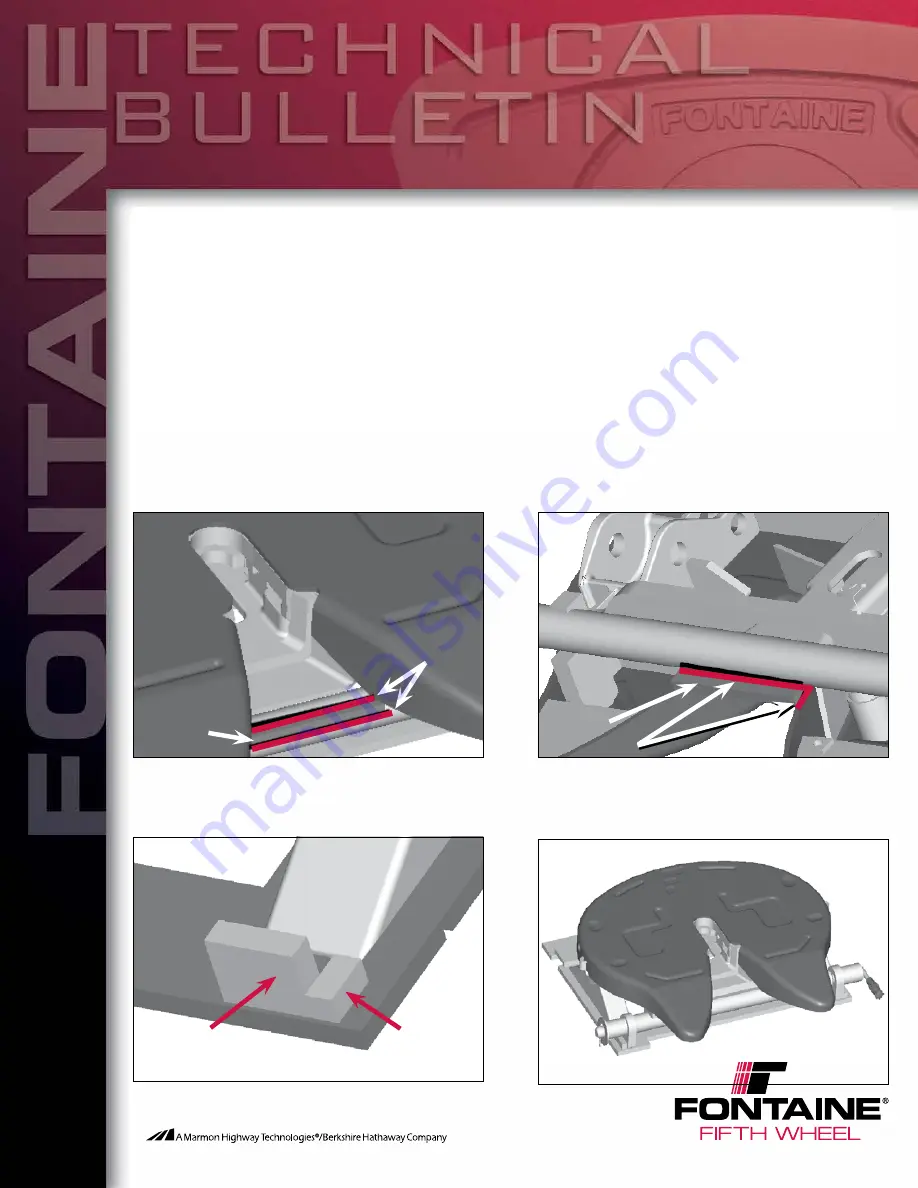
5
3520 Industrial Way • Jasper, AL 35501 • www.fifthwheel.com • 800-874-9780 • Email: [email protected]
Throat Plate Installation
FIGURE 13
Weld Here
Spacer
FIGURE
14
Throat Plate Installation
Weld Here
Spacer
FIGURE 16
Correct Position of Tube Supports
Rocker Limit Block and Guide Bar
FIGURE 15
Rocker Limit
Block
Guide
Block
6. Insert the 5/8" x 1" x 8.25" flat spacer bar behind tube. Next, tack the bar into position. Finally, weld a 3/16"
minimum fillet weld to throat plate, spacer and tube as shown in Figures 13 and 14.
7. Remove the Rocker Limit Blocks and Guide Bars (see Figure 15) from the lower assembly. Grind or burn blocks
off and grind all excess material until surface is flat.
8. Place top plate back on the bracket and set a level on top of top plate (figure 16).
9. Slide one shaft support onto shaft making sure the notched end of the shaft support is towards the front of top
plate and the tube of the shaft support is facing away from fifth wheel.
10. Slide shaft into tube and into the other shaft support making sure the notched end of shaft support is towards
the front of the wheel and the tube of the shaft support is facing away from fifth wheel as shown in Figure 16.
11. Trim ends of shaft supports, if necessary, so that top plate is sitting level.