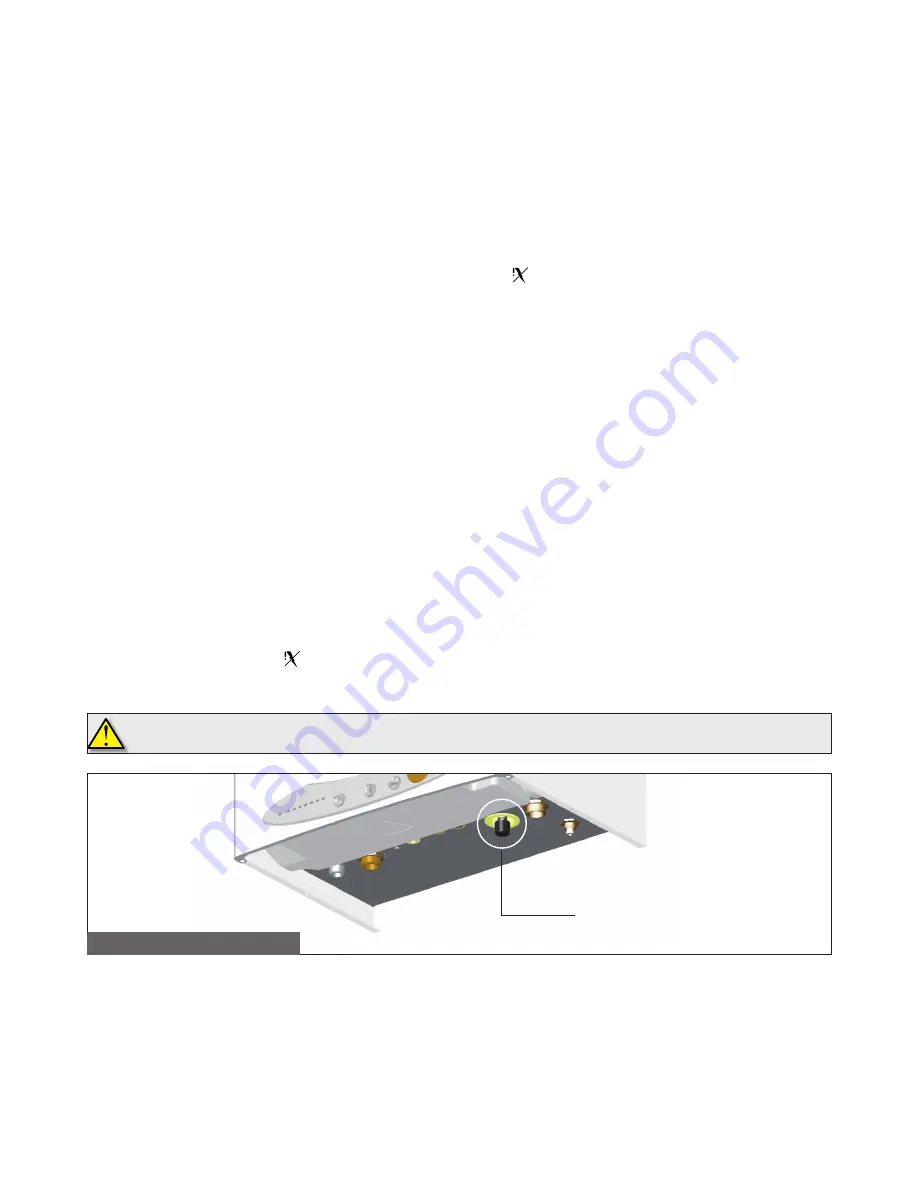
11
1.3. Boiler shut-down
If a malfunction occurs, the boiler automatically shuts down.
Refer to tables 1 and 2 for boiler status.
In order to determine the probable causes of the malfunction, refer to section 6 - Troubleshooting - at the end of this manual (in addition to
tables 1 and 2).
Follow the procedure described for the type of shut-down.
1.3.1. Burner shut-down
When the burner shuts down because the flame has gone out, light 5 (red) starts flashing. If this happens, proceed as follows.
• Check that the gas stopcock is open, and make sure the gas main is actually providing service by lighting a gas-powered kitchen appliance
such as a kitchen range or oven.
• Once the presence of gas has been verified, reset the burner by turning knob 9
to the RESET position for 2 seconds, and then to the
desired operating mode. If the boiler does not shut down, and you have performed the reset procedures three times, contact an authorized
Service Centre or a qualified service engineer.
Should frequent burner shut-down occur, a recurrent malfunction may be present. Contact an authorized Service Centre or a qualified service
engineer.
1.3.2. Shut-down due to overheating
When the CH water gets too hot, the boiler shuts down, and light 3 (red) starts flashing.
If this happens, contact an authorized Service Centre or a qualified service engineer.
1.3.3. Shut-down due to incorrect draught (clogging) of the flue system
If the burner shuts down due to a malfunction of the flue system (models CTN and RTN ) or the air intake and/or flue discharge piping (models
CTFS or RTFS), light 4 starts to flash. If this happens, contact a Service Centre or a qualified service engineer.
1.3.4. Shut-down due to low water pressure
If red shout-down light 6 comes on, it indicates low water pressure and intervention of the low water pressure switch.
Fill the boiler by opening tap А (рiс. 3): the water pressure must be 1÷1.3 bar when the boiler is cold.
In the event of low water pressure shut-down, proceed as follows:
• Turn the filling tap (pic. 3) counter-clockwise in order to let the water in.
• Leave the tap on until the water pressure gauge reads 1÷1.3 bar.
• Turn the tap off clockwise.
• Reset the burner by turning knob 9
to the RESET position for 2 seconds, and then to the desired operating mode.
If boiler shuts down frequently, it means the boiler is malfunctioning. Contact an authorized Service Centre or a qualified service
engineer.
Once the loading procedure has been completed, turn of the filling tap properly. If this isn’t done, the boiler CH safety
valve may open and water will flow out as the pressure increases.
1.3.5. Shut-down due to temperature probe malfunction
If the burner shuts down due to temperature probe malfunction, the following lights start to flash:
• Red light no. 2 and yellow light no. 8 when CH probe malfunction occurs.
• Red light no. 2 when DHW probe malfunction occurs.
• Red light no. 2 and yellow light no. 8 (flashing alternately) for external cylinder probe (models RTN and RTFS with external boiler and NTC
temperature probe).
If this happens, contact a Service Centre or a qualified service engineer.
Filling tap
pic. 3 - Filling tap