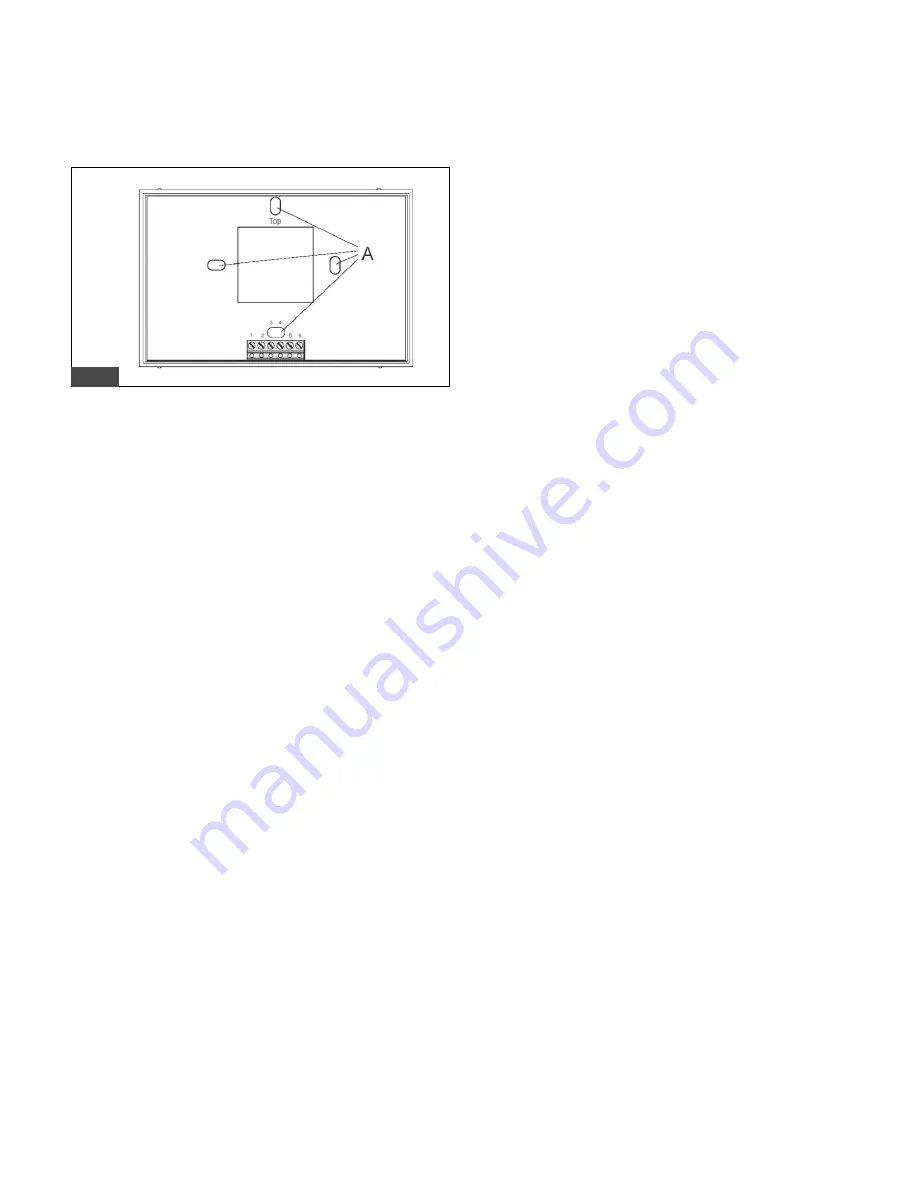
20
21
3.2.11.
“OPEN THERM”
remote control installation (option)
The heating unit can be connected to an
Open Therm
remote
control (delivered as optional equipment). Position the remote
control on an inside wall of the premises, far from heat sources or
draughts. Detach the rear part of the plastic casing (grey) from the
front one (white), by means of a screwdriver, and fix the rear part to
the wall using the holes A (pic.8).
pic. 8
WARNING
The remote control is not to be connected to the 230V power
main.
The remote control wires are not to be routed together with the
power main cables.
In order to connect the remote control, employ two-wire cables
with the following characteristics:
- max length:
40 m;
- max. impedance:
2 x 4 Ω/m
- in order to avoid interferences it is possible to implement interla-
ced wires or with a sheath.
An electronic board, code 0SCHEREM00 is provided with the
remote control kit, and it to be used to connect the remote control
to the boiler.
Refer to the instruction delivered with the electronic board, code
0SCHEREM00, for its installation.
The connection of the remote control to the heating units to be
implemented by connecting position 1 and 2 of the remote control
to the OT-BUS 06 terminal board of the 0SCHEREM00 board (see
electric layout charts). The OT-BUS 06 terminal board is protected
against false polarity, that is the connections can be switched.
Now close the remote control.
WARNING
When connecting the remote control, selector 11 is to be set
to the COMFORT � position, and the programmable timer,
when available, has to have both channels, 1 and 2, program-
med as permanently ON (see 1.2.3 paragraph).
3.2.12. External probe installation
The heating unit can be connected to an external probe for ou-
tdoor temperature measurement (standard for BV and RV models,
as option for B and R models), and “sliding temperature” function
operation (see 1.2.2.3 paragraph)
Refer to the heating unit layout charts when choosing the type
of external probe.
The external probe wires are NOT to be routed together with
the power main cables.
Position the external probe on an outside wall facing North – North
/ East.
Do not install the probe in the windows areas, near ventilation
openings or heat sources.
In order to assure correct heating unit operation, employ only
manufacturer supplied probes.
3.3. Filling up the heating system
When all system connections are performed, the CH circuit can be
filled.
The procedure is to be carefully performed, following the steps
below indicated:
- open all radiator air purging valves and the automatic relief valves
on the heating unit;
- remove the front panel (for model R), or its lower part (for models
B), of the heating unit by pulling it toward the outside;
- turn the loading tap counter-clockwise in order to allow water
into the system;
- close the radiator air purging valves as soon as water comes out;
- check the gauge to show a pressure of 1-1,3 bars;
- close the loading tap and open all radiator air purging valves
again;
- switch on the heating unit and allow the system to reach working
temperature, then switch it off and repeat the air bleeding proce-
dure;
- allow the system to cool down and check the water pressure to
be 1-1,3 bars.
3.4. Starting up the heating unit
3.4.1. Preliminary checks
Prior to starting up the heating unit perform the following checks:
- the flue gas discharge pipe and the air intake pipe are installed
correctly: while the heating unit is working, no leakage of
combustion products from any of the seals is to be detected;
- the power supply voltage is 230 V - 50 Hz;
- the system is correctly filled with water (water pressure gauge
reading 1-1,3 bar);
- any cut-off valves in the CH and DHW systems are open;
- the fuel supply tap is open;
- the master switch is ON;
- the safety valve is not blocked;
- no water leaks are detected;
3.4.2. Switching on and off
For instructions on how to switch the heating unit on and off, refer
to the “Instructions for the user”.
3.4.3. Burner adjustment
After starting up the heating unit it is necessary to adjust the bur-
ner (see paragraph 4.4), checking that:
- fuel oil pressure;
- CO
2
concentration;
- Bacharach index;
- flue gas temperature;
are in compliance with the values indicated in the technical data
chart (see4.4 paragraph).