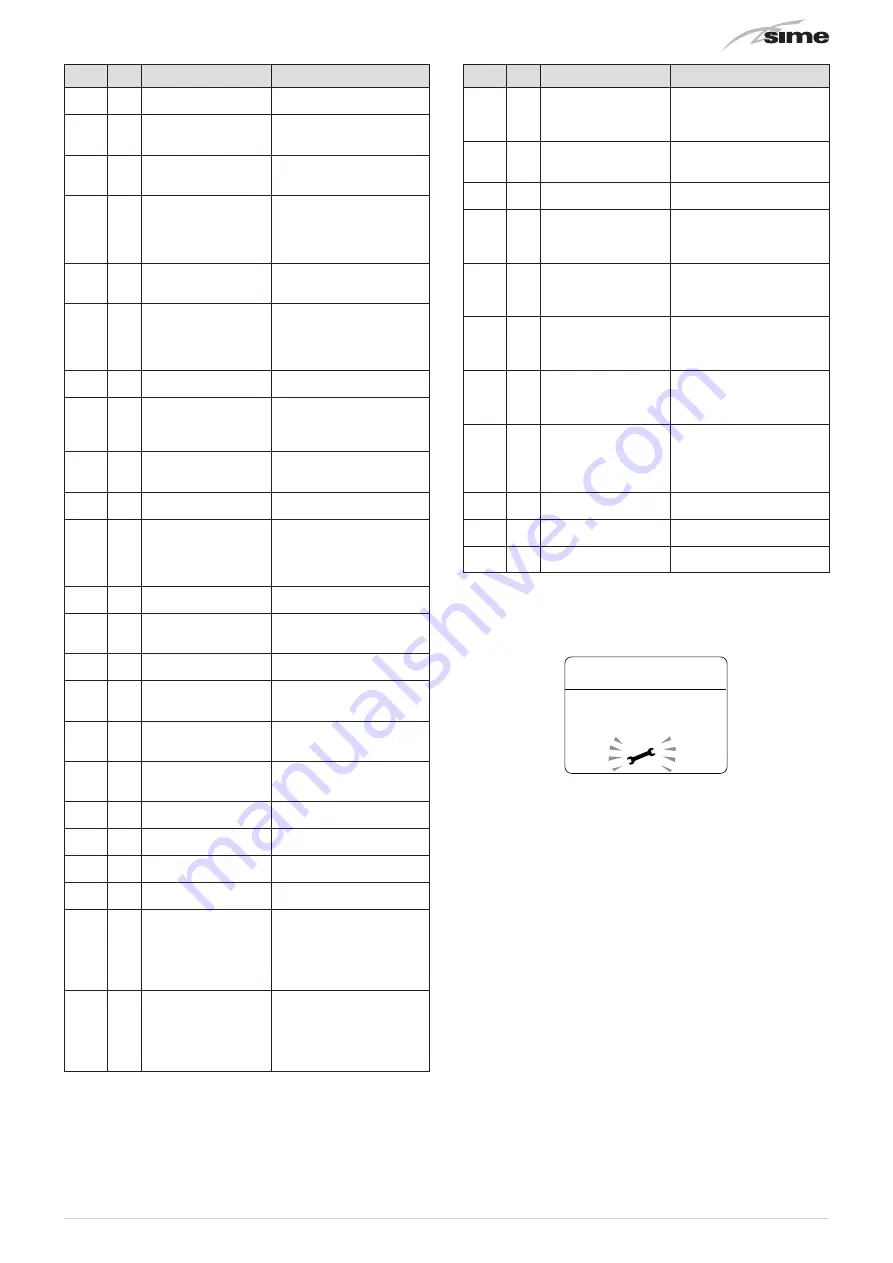
47
Type
No. Fault
Solution
ALL
11 Gas valve modulator
disconnected
- Check the electrical con-
nection
ALL
12
Incorrect configuration
of the open /sealed
chamber
- Set the parameter tS 0.4
(Combustion configuration)
to 0
ALL
13 Smoke probe inter-
vention
- Check the sensor is
working
- Replace the smoke probe
ALL
14 Smoke probe fault
- Replace the smoke probe
- Check the electrical con-
nection of the smoke probe
- Contact the Technical
Assistance Centre
ALL
15 Fan check cable dis-
connected
- Check the connection cable
between the fan and the
board
ALL
18 Condensate level fault
- Check for any clogging in
the pipe which takes the
condensate to the siphon
- Check that the siphon is
not clogged
ALL
28 Maximum number of
consecutive releases
- Contact the Technical
Assistance Centre
ALL
30 Return sensor (SR)
fault
- Replace the return probe
- Check parameters
- Contact the Technical
Assistance Centre
ALL
37 Fault due to low net-
work voltage
- Check the voltage
- Contact your network
provider
ALL
40 Incorrect network
frequency detected
- Contact your network
provider
ALL
41 Flame loss more than 6
consecutive times
- Check the detection
electrode
- Check the gas supply (open
valve)
- Check mains gas pressure
ALL
42 Button fault
- Check that buttons are
working
ALL
43 Open Therm communi-
cation fault
- Check the electrical
connection of the remote
control
ALL
44 No flame valve opening
time sum anomaly
- Replace the board
ALL
62 Self-calibrating proce-
dure is required
- Carry out the self-cali-
brating procedure (see the
specific section)
ALL
70 HP high pressure time
max. interventions
- Decrease setting PAR 46
- Contact the Technical
Assistance Centre
ALL
72 Incorrect positioning of
the delivery sensor
- Check that the delivery
sensor is attached to the
delivery pipe
ALL
77 EV current max/min
absolute limits error
- Check gas valve and board
ALL
78 EV current upper limit
error
- Check gas valve and board
ALL
79 EV current lower limit
error
- Check gas valve and board
ALL
80 Fault on the valve
control logic line
- Check/replace the connec-
tion cable to the gas valve
ALL
81 Block due combustion
during start-up
- Check for blockage in
chimney or recirculation
- Bleed the air from the gas
circuit
- Check for any dirt on the
air evaporator
ALL
82
Block due to numerous
combustion control
failures
- Check electrode
- Check outlets
- Check air diaphragm
- Check gas calibration
- Check for any dirt on the
air evaporator
Type
No. Fault
Solution
ALL
83 Irregular combustion
(temporary error)
- Check for blockage in
chimney
- Check for any dirt on the
air evaporator
ALL
84
Flow rate reduced for
(presumed) low pres-
sure on mains gas
- Check gas flow rate
ALL
88 Internal error (board
component protection) - Replace the board
ALL
89 Unstable combustion
feedback signal error
- Check electrode
- Check outlets
- Check air diaphragm
- Check gas calibration
ALL
90 Combustion set cannot
be reached error
- Check electrode
- Check outlets
- Check air diaphragm
- Check gas calibration
ALL
92
System has reached
maximum air cor-
rection error (at the
minimum flow rate)
- Check electrode
- Check outlets
- Check air diaphragm
- Check gas calibration
ALL
93 Combustion set cannot
be reached error
- Check electrode
- Check outlets
- Check air diaphragm
- Check gas calibration
ALL
95 Flame signal micro
interruptions error
- Check electrode
- Check board
- Check electric power
supply
- Check gas calibration
ALL
96 Block due to clogging
in smoke outlet
- Check for blockage in
chimney
ALL
98 SW error, board start-
up
- Contact the Technical
Assistance Centre
ALL
99 General board error
- Contact the Technical
Assistance Centre
8.7.1
Maintenance request
When it is time to perform maintenance on the boiler, the
c
symbol shows on the display.
Contact the technical assistance service to organise the neces-
sary work.