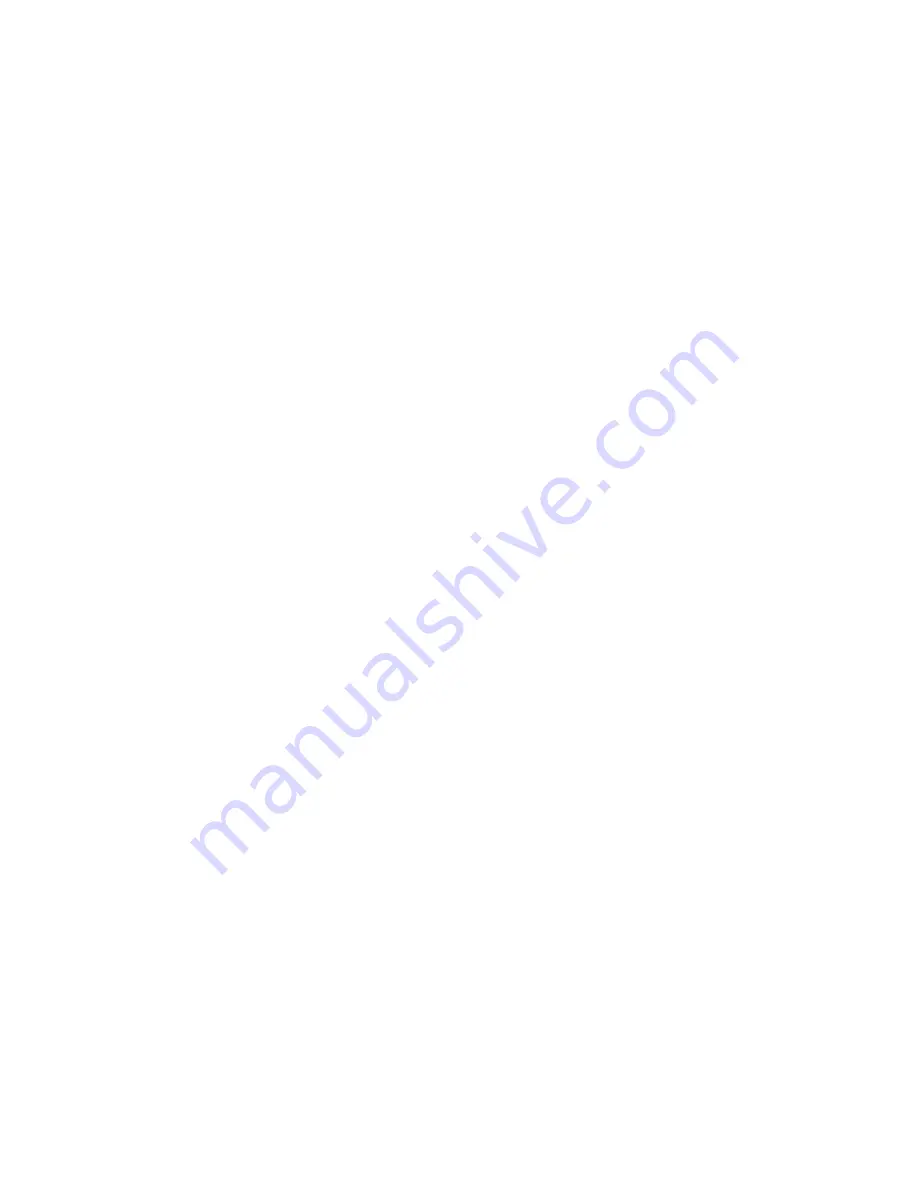
11
Recommended daily dispenser cleaning
1. Remove all debris from drain pan.
2. Pour 1 gallon (4L) hot water into drain pan to keep drain lines clear.
Recommended weekly dispenser cleaning
1. Remove drain pan and grille and wash with Solution A. Rinse thoroughly.
2. Remove nozzles and diffusers from valves, soak for at least 10 minutes in cleaning Solution A, rinse,
sanitize with Solution B and reinstall.
3. Pour a solution of one cup (8oz/237ml) household bleach mixed with one gallon (3.8L) hot water into
drain pan to help prevent algae growth in drain lines.
Recommended quarterly dispenser cleaning
1. Remove top from dispenser and turn power switch to OFF position.
2. Remove ice from storage area.
3. Remove dispense chute cover, chute, auger motor assembly, auger and auger tube (see Service section).
4. Remove drain pan, grille and dispense wheel (see Service section).
5. Clean all components and bin storage area with Solution A, rinse thoroughly with clear water and sanitize
with Solution B.
6. Remove nozzles and diffusers from valves, soak for at least 10 minutes in cleaning Solution A, rinse,
sanitize with Solution B and reinstall.
For units with integral ice-water bath beverage cooling only:
1. Remove dispenser lid and counter access panel opposite ice tower side.
2. Disengage service drain tube (on utility connection side of dispenser) from mounting bracket.
3. Pull bath service drain tube down through beverage line opening in counter and drain water bath into a bucket.
4. Use a bottle brush to clean coils with Solution A, rinse and sanitize with Solution B.
5. Reposition ice water bath drain tube in up position so water does not drain out.
6. Pour Solution A into ice water bath until it flows out of bath overflow drain.
7. Turn power ON to unit and dispense a small cup of ice to activate pump.
8. Allow pump to run for two minutes to clean pump and pump lines.
9. Turn power OFF.
10. Drain bath and replace drain tube in mounting bracket in up position to avoid siphoning water bath water.
Putting unit back in service after quarterly cleaning
1. On units with integral beverage cooling, fill ice water bath with water until water spills out of
bath overflow drain.
2. Reassemble components.
3. For manual load units, fill unit with an approved ice (see important cautions on page 4).
4. For automatic load units with R400A/W (R404A refrigerant) icemakers, turn bin signal switch(es) and
dispenser power switch to ON position and allow storage area to fill.
5. Dispense and discard all ice, verifying dispenser is functioning properly.
Recommended quarterly cleaning of optional icemaker.
Units equipped with optional icemakers require cleaning of icemaker system at least every six months, and more
often if local water conditions dictate. Failure to clean icemaker system will result in decreased performance and
potential damage to icemaker. Refer to Icemaker Installation, Operation and Service Manual.