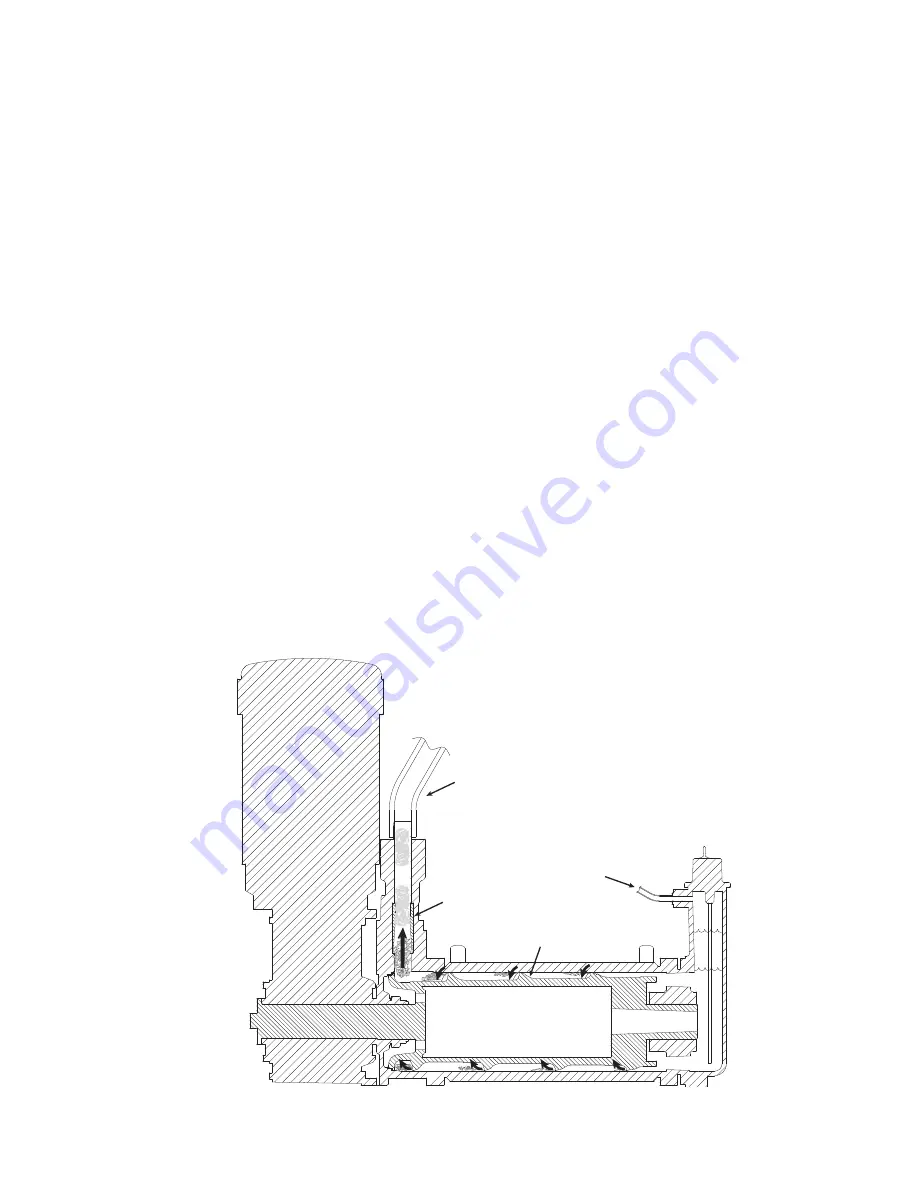
12
Service
Ice machine operation (all models)
Follett’s ice machine consists of fi ve distinct functional systems covered in detail as follows:
• Water system
• Electrical control system
• Mechanical assembly
• Refrigeration system
• Bin full
The Horizon ice machine overview
The Follett Horizon ice machine uses a horizontal, cylindrical evaporator to freeze water on its inner surface. The
refrigeration cycle is continuous; there is no batch cycle. The evaporator is fl ooded with water and the level is
controlled by sensors in a reservoir. A rotating auger (17 RPM @ 50Hz) continuously scrapes ice from the inner
wall of the evaporator. The auger moves harvested ice through the evaporator into an ice extrusion canal. The ice is
forced through a restrictive nozzle that squeezes out the water and creates the Chewblet. The continuous extrusion
process pushes the Chewblets through a transport tube into a dispenser or bin.
A solid state PC board controls and monitors the functionality of the ice machine. In addition to sequencing electrical
components, the board monitors various operational parameters. A full complement of indicator lights allows visual
status of the machine's operation. Additionally, the PC board controls the self-fl ushing feature of the ice machine. The
evaporator water is periodically drained and replenished to remove minerals and sediment.
A unique “bin full” detection system is incorporated in the Horizon ice machine. A sensor located at the ice discharge
port of the machine detects the position of the transport tube. When the bin fi lls up with ice, the transport tube
moves out of the normal running position, and the sensor turns the ice maker off. A domed housing at the end of the
transport tube contains the ice extrusion loads during shut down.
water
inlet
auger
compression
nozzle
ice
transport
tube
Harvest system diagram